
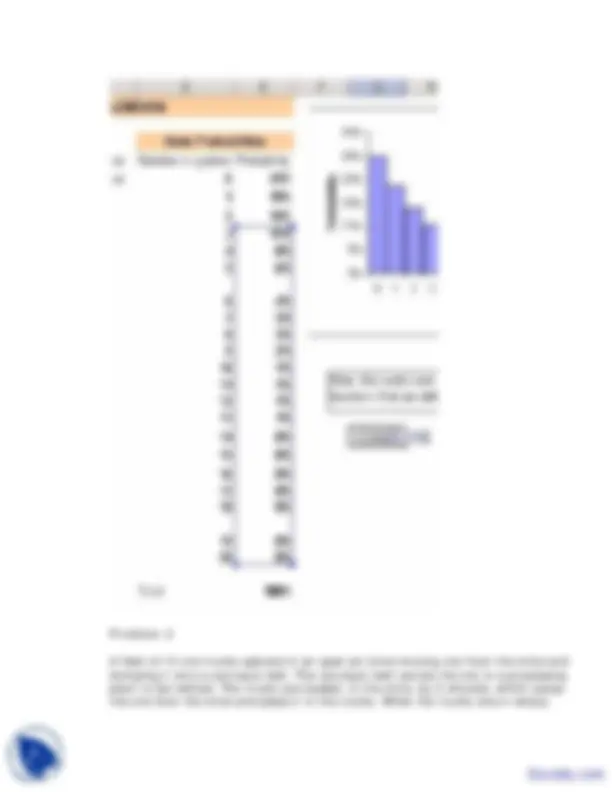
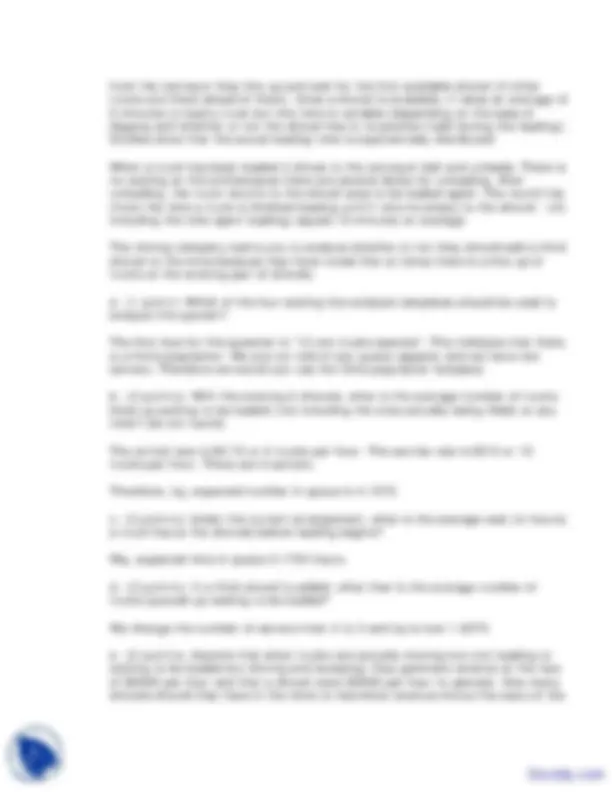

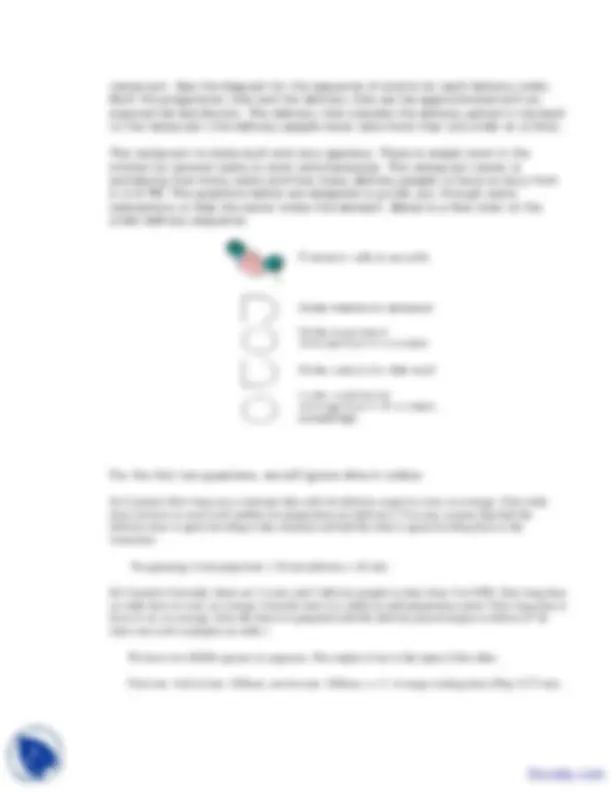
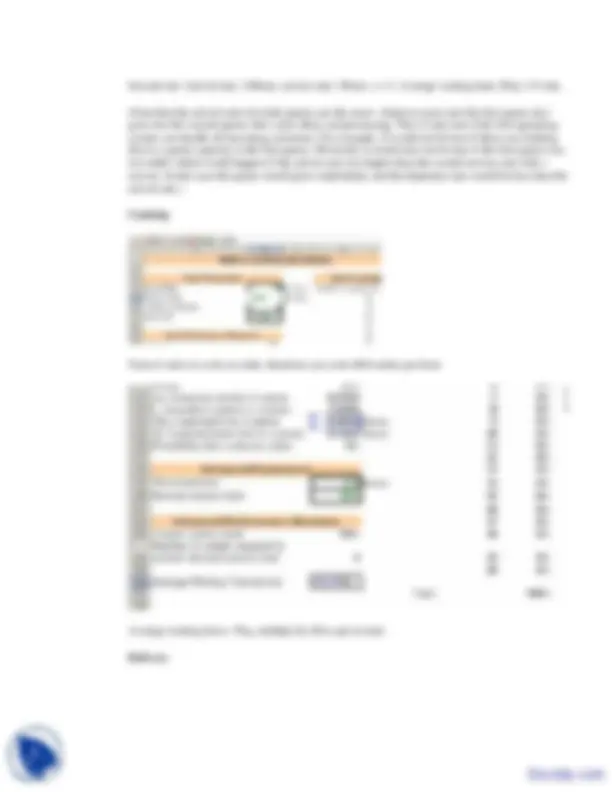


Study with the several resources on Docsity
Earn points by helping other students or get them with a premium plan
Prepare for your exams
Study with the several resources on Docsity
Earn points to download
Earn points by helping other students or get them with a premium plan
Community
Ask the community for help and clear up your study doubts
Discover the best universities in your country according to Docsity users
Free resources
Download our free guides on studying techniques, anxiety management strategies, and thesis advice from Docsity tutors
Congestion Management, Amount of Time, Number of People, Using Or Waiting, Memoryless Arrival Process, Memoryless Service Process, Expected Number, Ore Trucks, Open Pit Mine, Waiting Line Analysis.These are the important points of Lab Manual.
Typology: Study notes
1 / 13
This page cannot be seen from the preview
Don't miss anything!
NOTE: When you open this file you may receive a message asking if you would like to "Enable Macros". Always click "Yes" or the queueing formulas will not work for you. If you are not getting this message and the formulas are not working you may need to change your security settings. Go to Tools -> Macros -> Security. Select "Medium". This will ensure that you are asked about all macros in any Excel file.
Problem 1
A suburban transit station has one public telephone. During rush hours, individuals wanting to place calls arrive at the telephone booth randomly at the rate of 15 per hour. The average duration of a phone call is 3 minutes with the duration being exponentially distributed. Find:
once having arrived at the booth
Approach
This problem has m emoryless arrival process, m emoryless service process and s servers. Therefore it is a M/M/s system. We need to enter the information into the M/M/S template.
Note that it is important to make sure all of the parameters are in the same time units.
Wq, expected time in queue 0.1500 hours or 9 minutes
L, expected number in system 3.
= 1 person using the telephone and 2 or more people waiting = 3 or more people "in system"
from the conveyor they line up and wait for the first available shovel (if other trucks are there ahead of them). Once a shovel is available, it takes an average of 5 minutes to load a truck but this time is variable (depending on the ease of digging and whether or not the shovel has to re-position itself during the loading). Studies show that the actual loading time is exponentially distributed.
When a truck has been loaded it drives to the conveyor belt and unloads. There is no waiting at this end because there are several docks for unloading. After unloading, the truck returns to the shovel area to be loaded again. The round trip (from the time a truck is finished loading until it returns empty to the shovel - not including the time spent loading) equals 15 minutes on average.
The mining company wants you to analyze whether or not they should add a third shovel to the mine because they have noted that at times there is a line up of trucks at the existing pair of shovels.
a. (1 point) Which of the four waiting line analysis templates should be used to analyze this system?
The first clue for this question is "12 ore trucks operate". This indicates that there is a finite population. We are not told of any queue capacity and we have two servers. Therefore we would you use the finite population template.
b. (2 points) With the existing 2 shovels, what is the average number of trucks lined up waiting to be loaded (not including the ones actually being filled) at any time? (do not round)
The arrival rate is 60/15 or 4 trucks per hour. The service rate is 60/5 or 12 trucks per hour. There are 2 servers.
Therefore, Lq, expected number in queue is 4.1372.
c. (2 points) Under the current arrangement, what is the average wait (in hours) a truck has at the shovels before loading begins?
Wq, expected time in queue 0.1754 hours.
d. (2 points) If a third shovel is added, what then is the average number of trucks queued up waiting to be loaded?
We change the number of servers from 2 to 3 and Lq is now 1.5070.
e. (2 points) Assume that when trucks are actually moving ore (not loading or waiting to be loaded but driving and dumping) they generate revenue at the rate of $5000 per hour and that a shovel costs $3000 per hour to operate. How many shovels should they have in the mine to maximize revenue minus the costs of the
shovels? What is the total hourly profit (truck revenue - shovel costs) of the optimal configuration?
First we need to calculate the total hourly revenue. To do this we need to know how many trucks are driving and dumping. We can assume that if a truck is not waiting to be filled or in the process of being filled that the truck is working (driving or dumping). Therefore, the total number of trucks minus the expected number in system will give you the total number of trucks working.
In cell B
In cell B20 we will enter the revenue/truck/hour $
In cell B21 we will calculate the total hourly revenue
Then we highlight A30:B39 and go to Data -> Table
The row input cell is blank and the column input cell is
We can see that the optimal number of shovels to have in order to maximize net income is 4 and the resulting net income is $31,337.
Problem 3
A restaurant offers both dine-in and delivery services. During the busiest part of the day (5 – 8 PM) about 10 calls for delivery arrive per hour, according to a memoryless process (this means that times between arrivals are exponentially distributed).
It takes an average of 6 minutes for a cook to prepare an order and it takes an average of 20 minutes for a delivery person to deliver an order and return to the
restaurant. See the diagram for the sequence of events for each delivery order. Both the preparation time and the delivery time can be approximated with an exponential distribution. The delivery time includes the delivery person’s trip back to the restaurant (the delivery people never take more than one order at a time).
The restaurant is newly built and very spacious. There is ample room in the kitchen for several cooks to work simultaneously. The restaurant owner is wondering how many cooks and how many delivery people to have on duty from 5 to 8 PM. The questions below are designed to guide you through some calculations to help the owner make this decision. Below is a flow chart of the order/delivery sequence:
For the first two questions, we will ignore dine-in orders.
1) (2 points) How long can a customer that calls for delivery expect to wait, on average, if his order does not have to wait at all (neither for preparation nor delivery)? You may assume that half the delivery time is spent traveling to the customer and half the time is spent traveling back to the restaurant.
No queueing. 6 min prep time + 10 min delivery = 16 min.
2) (3 points) Currently, there are 3 cooks and 5 delivery people on duty from 5 to 8 PM. How long does an order have to wait, on average, from the time it is called in until preparation starts? How long does it have to sit, on average, from the time it is prepared until the delivery person begins to deliver it? (It takes one cook to prepare an order.)
We have two M/M/s queues in sequence. The output of one is the input of the other.
First one: Arrival rate: 10/hour, service rate: 10/hour, s = 3. Average waiting time (Wq): 0.27 min.
It takes 20 mins to deliver the order, therefore 60/20 orders can be delivered in one hour.
Average waiting time = Wq, multiply by 60 to get in mins
3) (4 points) In addition to the delivery orders, the cooks have to keep up with about 15 dine-in orders per hour. Like the delivery orders, the dine-in orders arrive in a memoryless fashion. Revise your analysis from 2) accordingly. Again, report the average time a delivery order spends waiting for
preparation and the average time a prepared order spends waiting for delivery to begin.
Cooking
Arrival rate changes to 25/hour for the first queue
First queue (cooking): Wq = 8.4 min.
Delivery
Second queue: same as before (unaffected by dine-in orders) 3.9 min.
Assume that there are dine-in orders when answering question 4 and 5.
4) (3 points) How long does it take, on average, from the time when a customer calls in a delivery order until the customer receives the order? (Assuming the situation where there are dine-in orders.)
Time between call-in and receipt of an order = time spent in the first system
Time spent in the first queue + service: 14.4 min.
Time spent in the second queue: 3.9 min.
Delivery = 10 min. (this is the service portion of the second queue)
Total: 28.3 min.
5) (3 points) Notice that the time a delivery order waits for delivery is shorter than the time it waits to be prepared (Hint! You can use this to check your answer to question 3). Because of this, the owner is