
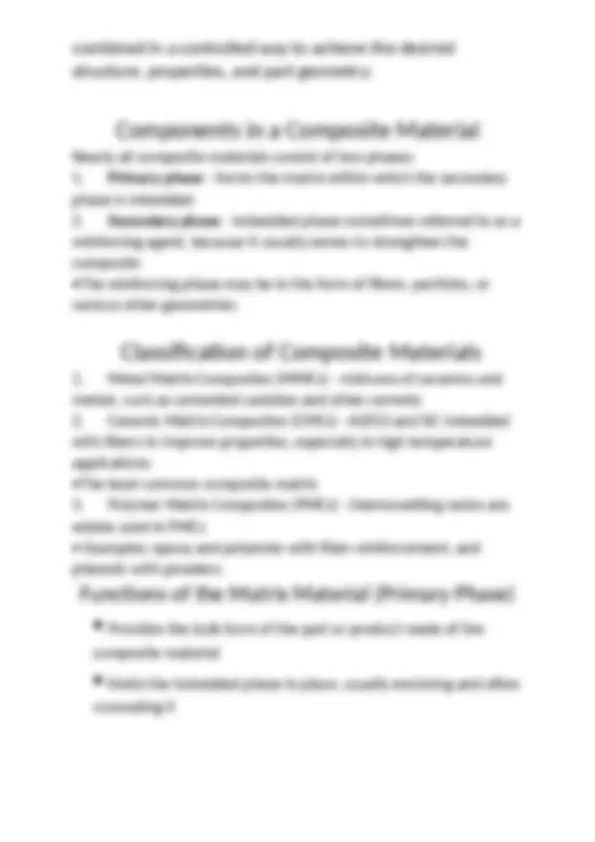
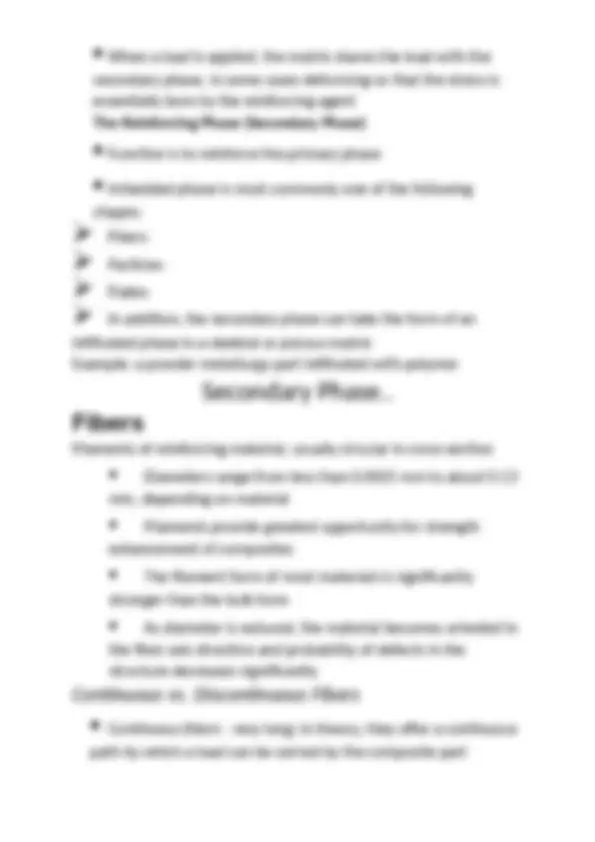
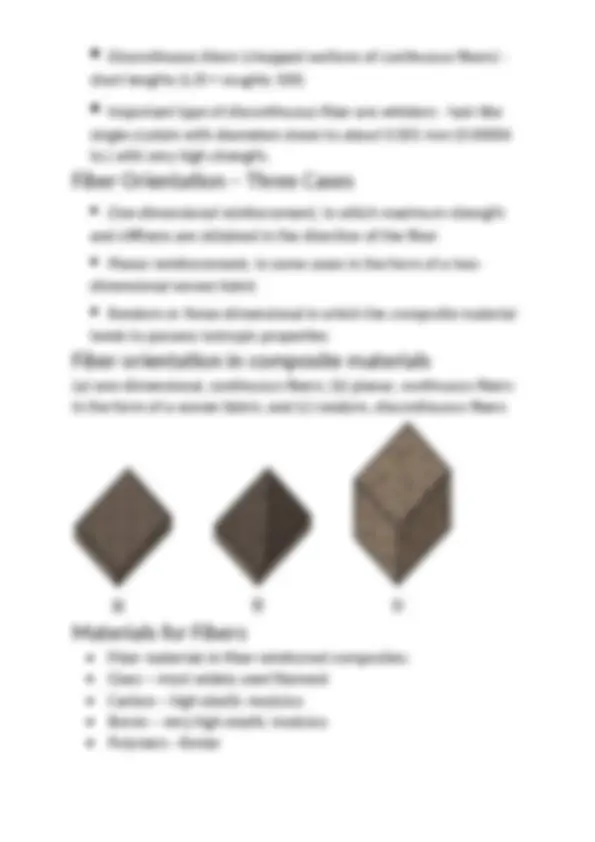
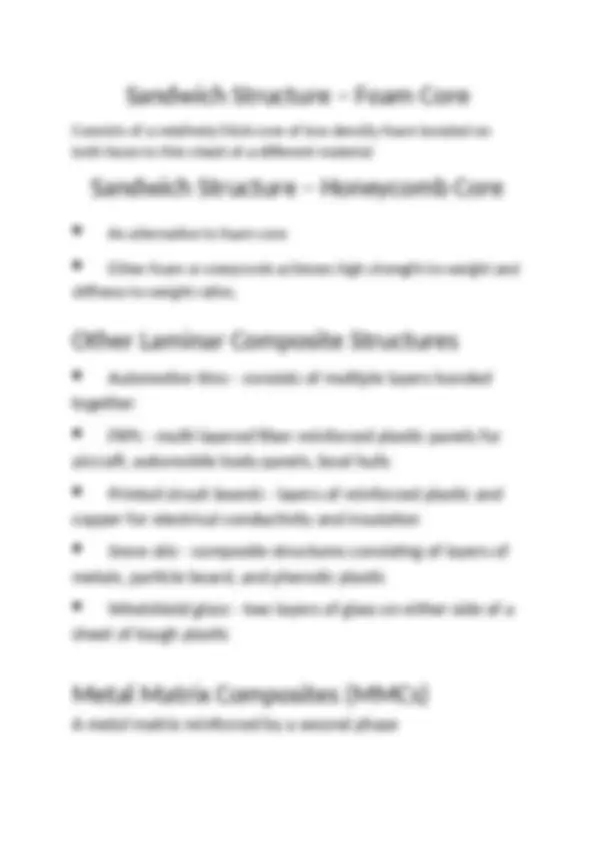
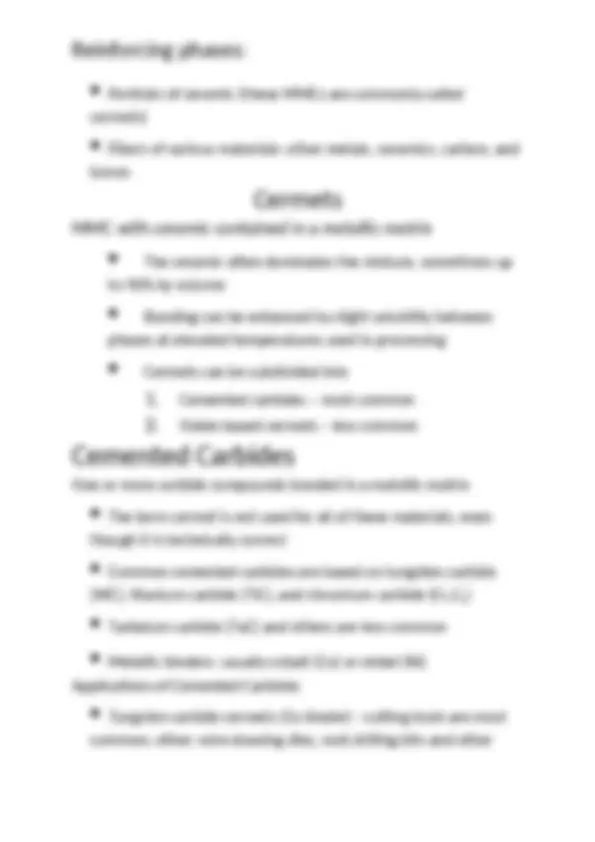

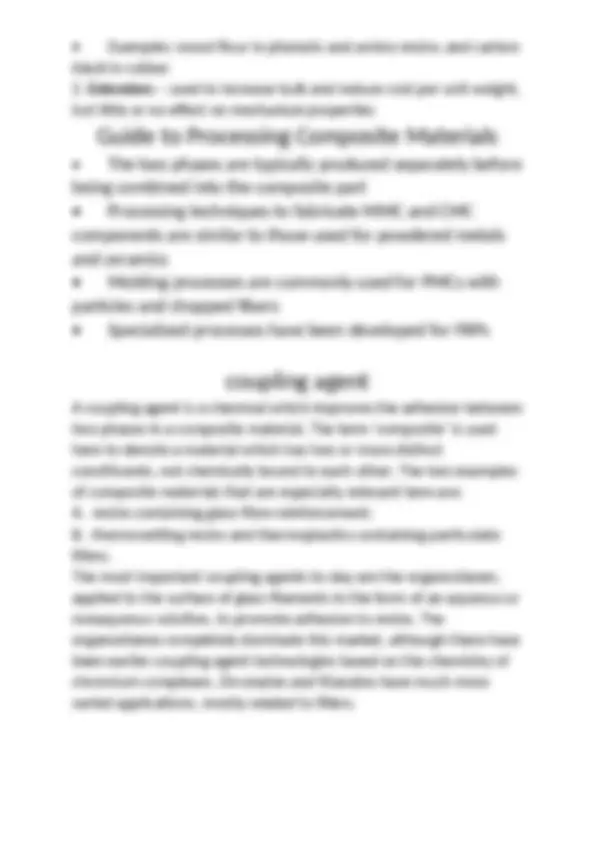
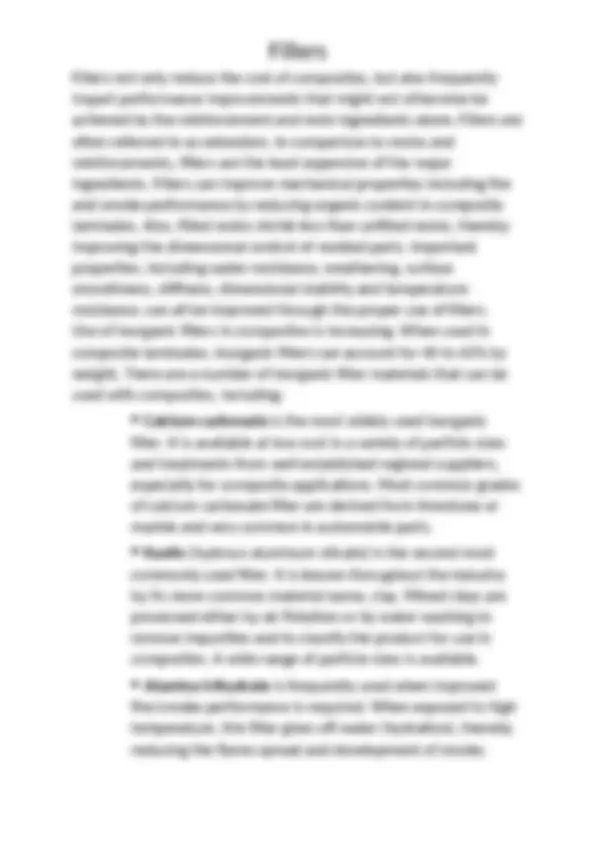
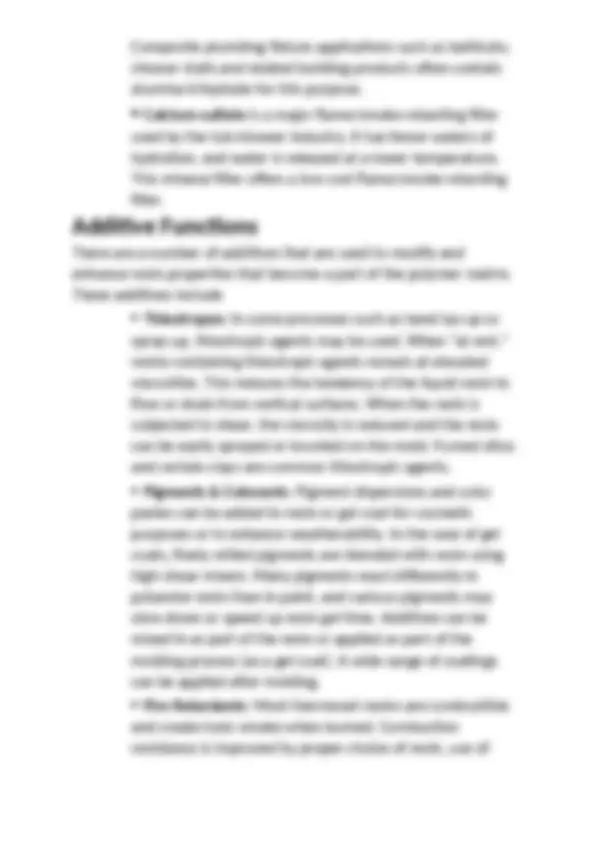
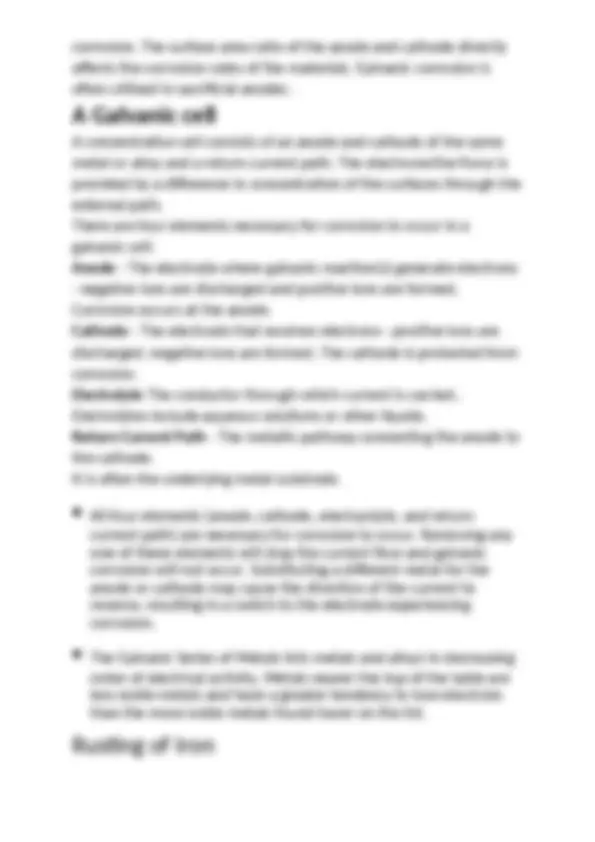
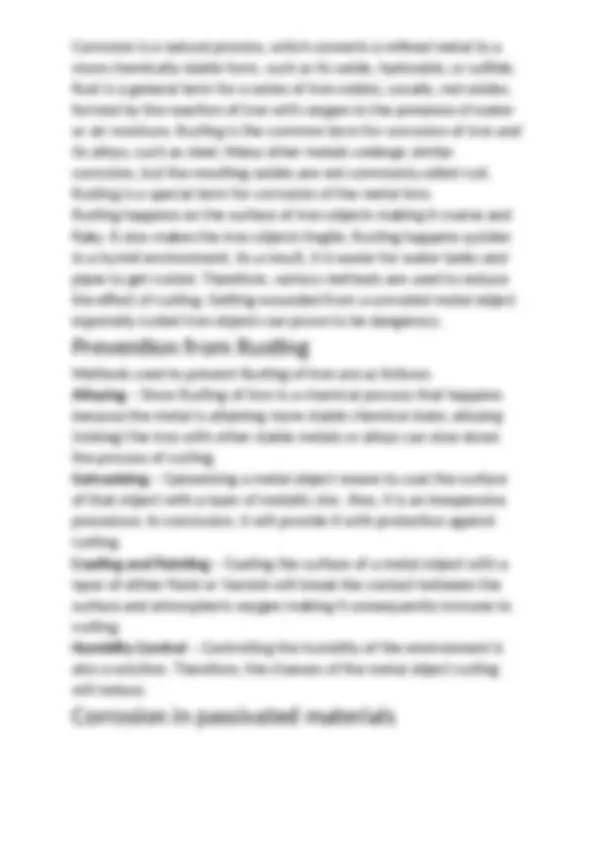
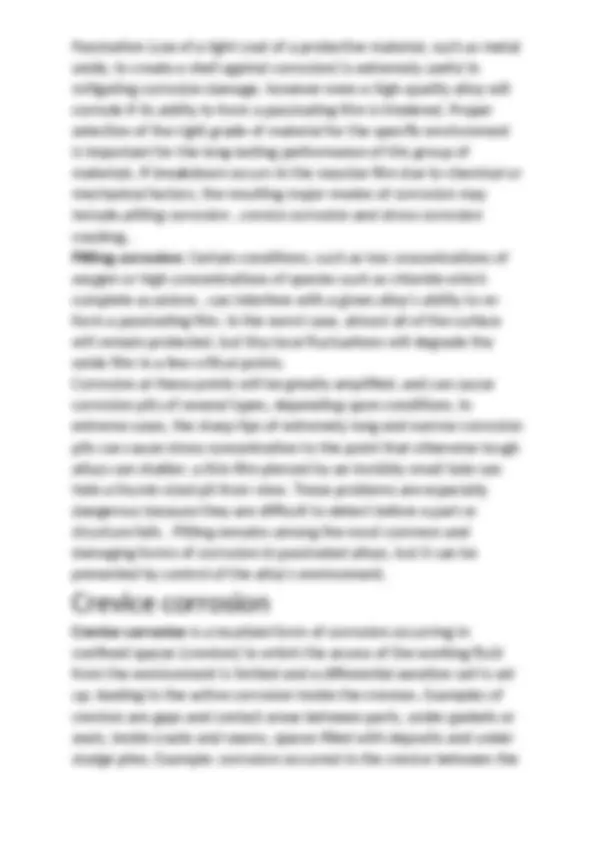
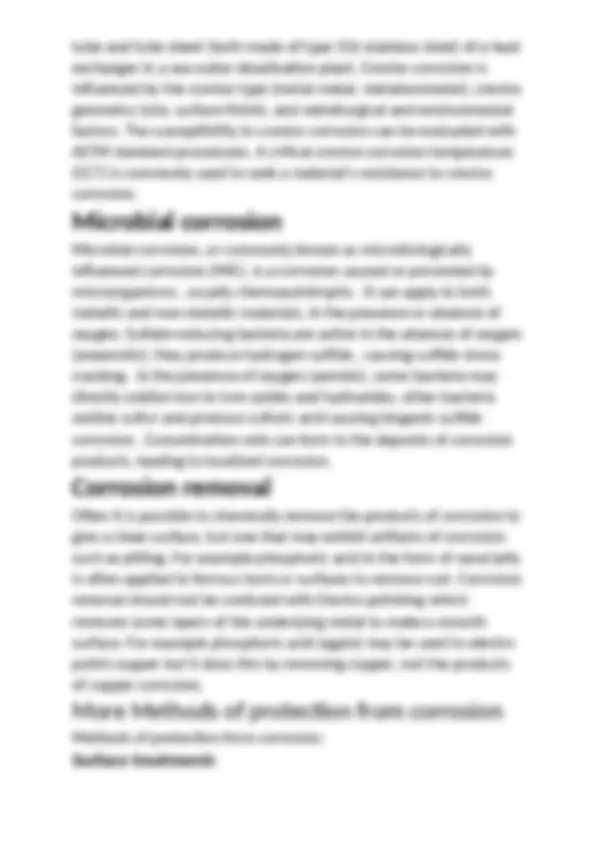
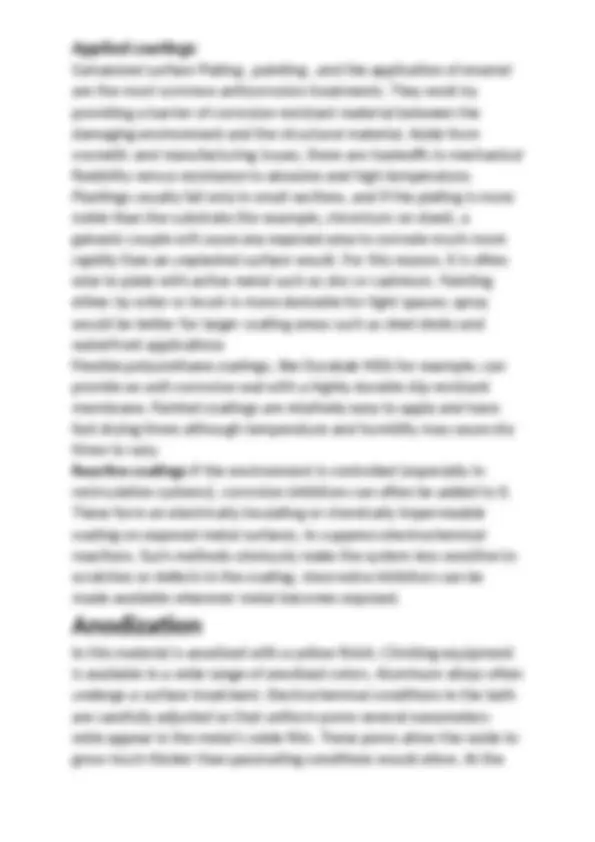
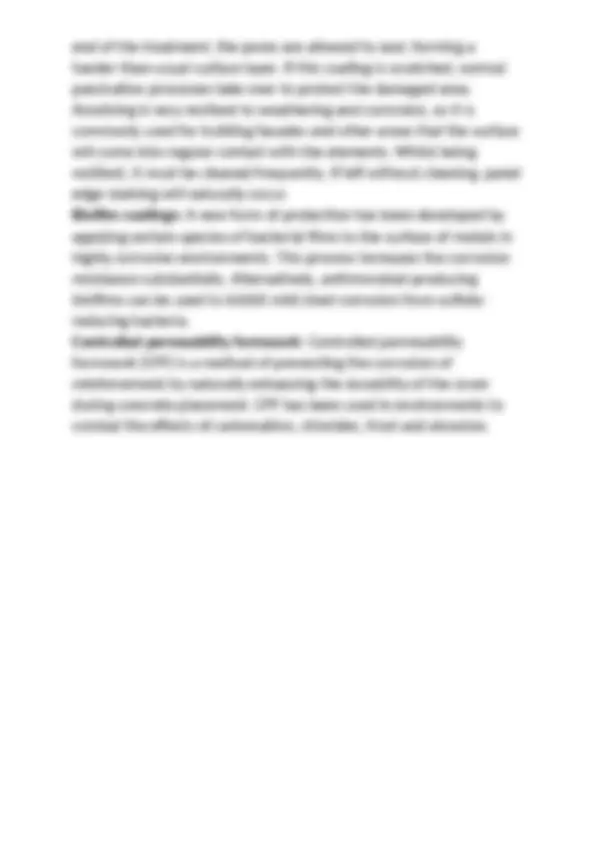
Study with the several resources on Docsity
Earn points by helping other students or get them with a premium plan
Prepare for your exams
Study with the several resources on Docsity
Earn points to download
Earn points by helping other students or get them with a premium plan
Community
Ask the community for help and clear up your study doubts
Discover the best universities in your country according to Docsity users
Free resources
Download our free guides on studying techniques, anxiety management strategies, and thesis advice from Docsity tutors
Composite Material And its usages
Typology: Lecture notes
1 / 23
This page cannot be seen from the preview
Don't miss anything!
A materials system composed of two or more physically distinct phases whose combination produces aggregate properties that are different from those of its constituents
composite)
properties differ depending on the direction in which they are measured – this may be an advantage or a disadvantage
chemicals or solvents, just as the polymers themselves are susceptible to attack
often slow and costly.
secondary phase, in some cases deforming so that the stress is essentially born by the reinforcing agent The Reinforcing Phase (Secondary Phase)
shapes:
infiltrated phase in a skeletal or porous matrix Example: a powder metallurgy part infiltrated with polymer
Filaments of reinforcing material, usually circular in cross-section
mm, depending on material
enhancement of composites
stronger than the bulk form
the fiber axis direction and probability of defects in the structure decreases significantly
path by which a load can be carried by the composite part
short lengths (L/D = roughly 100)
single crystals with diameters down to about 0.001 mm (0. in.) with very high strength.
and stiffness are obtained in the direction of the fiber
dimensional woven fabric
tends to possess isotropic properties
(a) one-dimensional, continuous fibers; (b) planar, continuous fibers in the form of a woven fabric; and (c) random, discontinuous fibers
Two or more layers bonded together in an integral piece
Consists of a relatively thick core of low density foam bonded on both faces to thin sheet of a different material
stiffness-to-weight ratios.
mining tools, dies for powder metallurgy, indenters for hardness testers
applications such as gas-turbine nozzle vanes, valve seats, thermocouple protection tubes, torch tips, cutting tools for steels
liners, spray nozzles, bearing seal rings
A ceramic primary phase imbedded with a secondary phase, which usually consists of fibers
hardness, and compressive strength; and relatively low density
strength, susceptibility to thermal cracking
of ceramics while compensating for their weaknesses
A polymer primary phase in which a secondary phase is imbedded as fibers, particles, or flakes
with carbon black, and fiber-reinforced polymers (FRPs)
A PMC consisting of a polymer matrix imbedded with high-strength fibers
Fillers Fillers not only reduce the cost of composites, but also frequently impart performance improvements that might not otherwise be achieved by the reinforcement and resin ingredients alone. Fillers are often referred to as extenders. In comparison to resins and reinforcements, fillers are the least expensive of the major ingredients. Fillers can improve mechanical properties including fire and smoke performance by reducing organic content in composite laminates. Also, filled resins shrink less than unfilled resins, thereby improving the dimensional control of molded parts. Important properties, including water resistance, weathering, surface smoothness, stiffness, dimensional stability and temperature resistance, can all be improved through the proper use of fillers. Use of inorganic fillers in composites is increasing. When used in composite laminates, inorganic fillers can account for 40 to 65% by weight. There are a number of inorganic filler materials that can be used with composites, including:
fillers or flame retardant additives. Included in this category are materials containing ATH (alumina trihydrate), bromine, chlorine, borate and phosphorus.
the word, this means electro-chemical oxidation of metals in reaction with an oxidant such as oxygen. Rusting, the formation of iron oxides is a well-known example of electrochemical corrosion. This type of damage typically produces oxides or salts of the original metal. Corrosion can also occur in materials other than metals, such as ceramics or polymers, although in this context, the term degradation is more common. Corrosion degrades the useful properties of materials and structures including strength, appearance and ability to contain a vessel's contents. Many structural alloys corrode merely from exposure to moisture in the air , but the process can be strongly affected by exposure to certain substances. Corrosion can be concentrated locally to form a pit or crack, or it can extend across a wide area more or less uniformly corroding the surface. Because corrosion is a diffusion controlled process, it occurs on exposed surfaces. As a result, methods to reduce the activity of the exposed surface, such as passivation and chromateconversion , can increase a material's corrosion resistance. However, some corrosion mechanisms are less visible and less predictable. GALVANIC CORROSION Galvanic corrosion occurs when two different metals have physical or electrical contact with each other and are immersed in a common electrolyte , or when the same metal is exposed to electrolyte with different concentrations. In a galvanic couple , the more active metal (the anode) corrodes at an accelerated rate and the more noble metal (the cathode) corrodes at a retarded rate. When immersed separately, each metal corrodes at its own rate. What type of metal(s) to use is readily determined by the galvanic series. For example, zinc is often used as a sacrificial anode for steel structures. Galvanic corrosion is of major interest to the marine industry and also anywhere water (via impurities such as salt ) contacts pipes or metal structures. Factors such as relative size of anode , types of metal, and operating conditions ( temperature , humidity , salinity , etc.) affect galvanic
Corrosion is a natural process, which converts a refined metal to a more chemically-stable form, such as its oxide, hydroxide, or sulfide. Rust is a general term for a series of iron oxides, usually, red oxides, formed by the reaction of iron with oxygen in the presence of water or air moisture. Rusting is the common term for corrosion of iron and its alloys, such as steel. Many other metals undergo similar corrosion, but the resulting oxides are not commonly called rust. Rusting is a special term for corrosion of the metal Iron. Rusting happens on the surface of iron objects making it coarse and flaky. It also makes the iron objects fragile. Rusting happens quicker in a humid environment. As a result, it is easier for water tanks and pipes to get rusted. Therefore, various methods are used to reduce the effect of rusting. Getting wounded from a corroded metal object especially rusted iron objects can prove to be dangerous. Prevention from Rusting Methods used to prevent Rusting of Iron are as follows: Alloying – Since Rusting of Iron is a chemical process that happens because the metal is attaining more stable chemical state, alloying (mixing) the iron with other stable metals or alloys can slow down the process of rusting. Galvanizing – Galvanizing a metal object means to coat the surface of that object with a layer of metallic zinc. Also, it is an inexpensive procedure. In conclusion, it will provide it with protection against rusting. Coating and Painting – Coating the surface of a metal object with a layer of either Paint or Varnish will break the contact between the surface and atmospheric oxygen making it consequently immune to rusting. Humidity Control – Controlling the humidity of the environment is also a solution. Therefore, the chances of the metal object rusting will reduce. Corrosion in passivated materials
Passivation (use of a light coat of a protective material, such as metal oxide, to create a shell against corrosion) is extremely useful in mitigating corrosion damage, however even a high-quality alloy will corrode if its ability to form a passivating film is hindered. Proper selection of the right grade of material for the specific environment is important for the long-lasting performance of this group of materials. If breakdown occurs in the massive film due to chemical or mechanical factors, the resulting major modes of corrosion may include pitting corrosion , crevice corrosion and stress corrosion cracking. Pitting corrosion: Certain conditions, such as low concentrations of oxygen or high concentrations of species such as chloride which complete as anions , can interfere with a given alloy's ability to re- form a passivating film. In the worst case, almost all of the surface will remain protected, but tiny local fluctuations will degrade the oxide film in a few critical points. Corrosion at these points will be greatly amplified, and can cause corrosion pits of several types, depending upon conditions. In extreme cases, the sharp tips of extremely long and narrow corrosion pits can cause stress concentration to the point that otherwise tough alloys can shatter; a thin film pierced by an invisibly small hole can hide a thumb sized pit from view. These problems are especially dangerous because they are difficult to detect before a part or structure fails. Pitting remains among the most common and damaging forms of corrosion in passivated alloys, but it can be prevented by control of the alloy's environment.
Crevice corrosion is a localized form of corrosion occurring in confined spaces (crevices) to which the access of the working fluid from the environment is limited and a differential aeration cell is set up, leading to the active corrosion inside the crevices. Examples of crevices are gaps and contact areas between parts, under gaskets or seals, inside cracks and seams, spaces filled with deposits and under sludge piles. Example: corrosion occurred in the crevice between the