
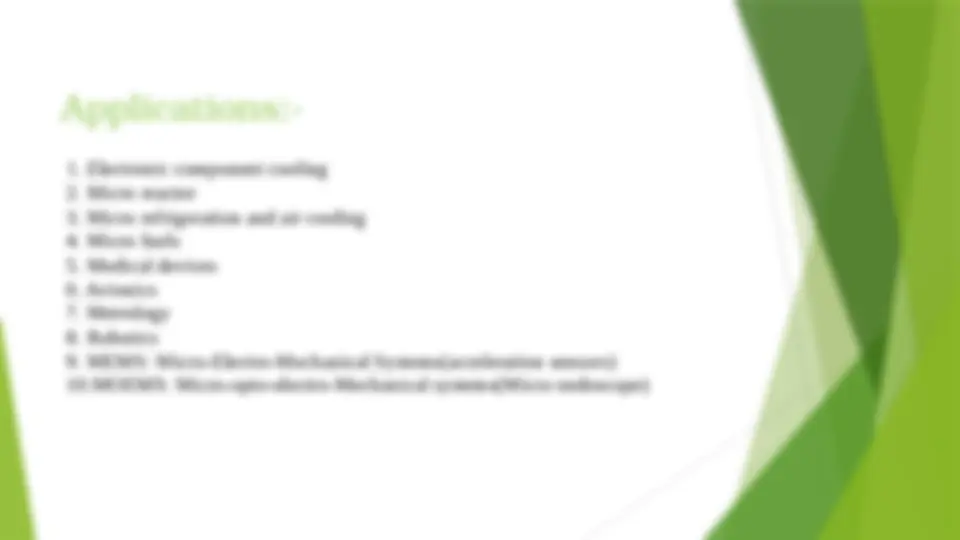
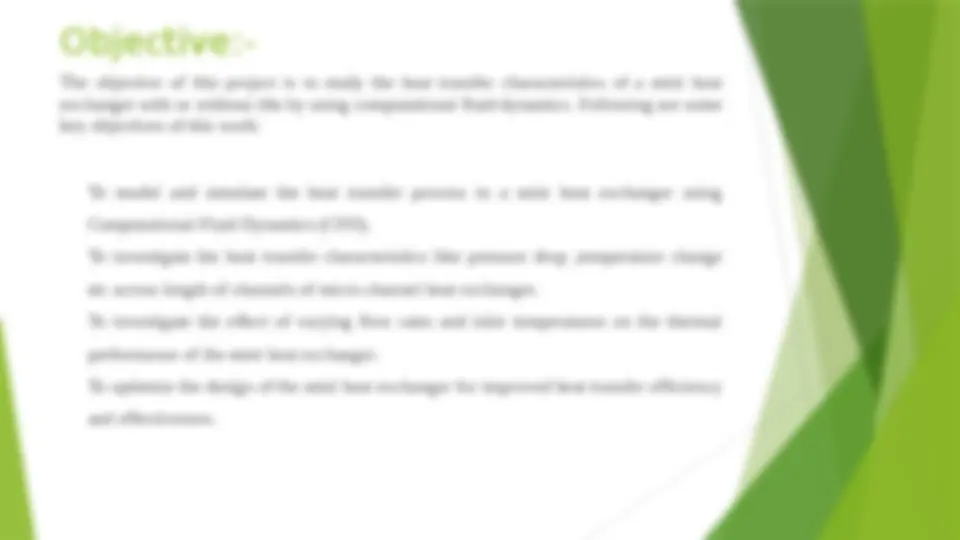
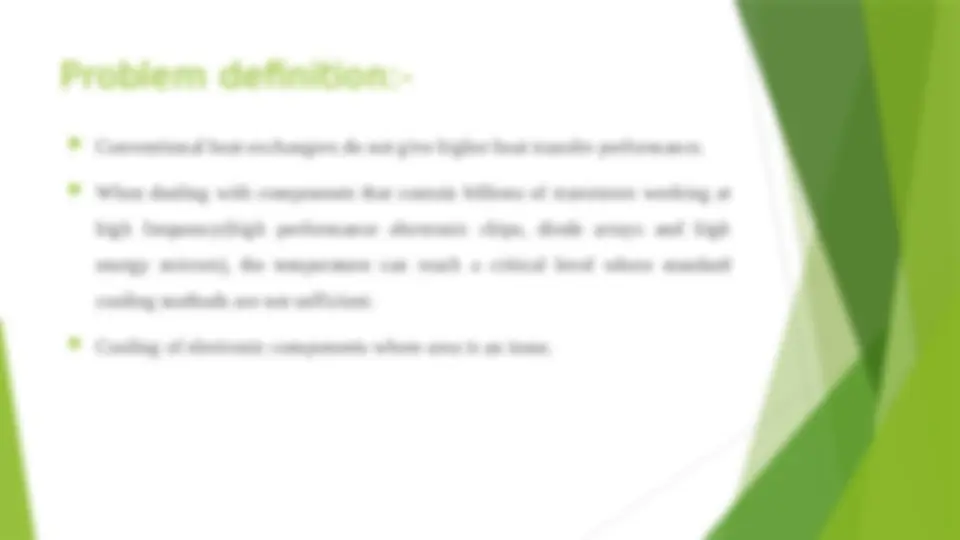

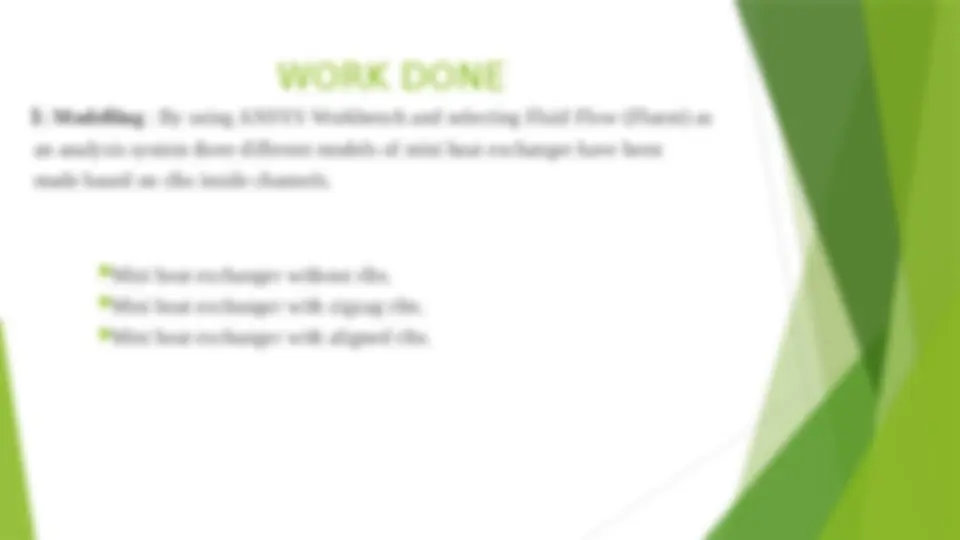
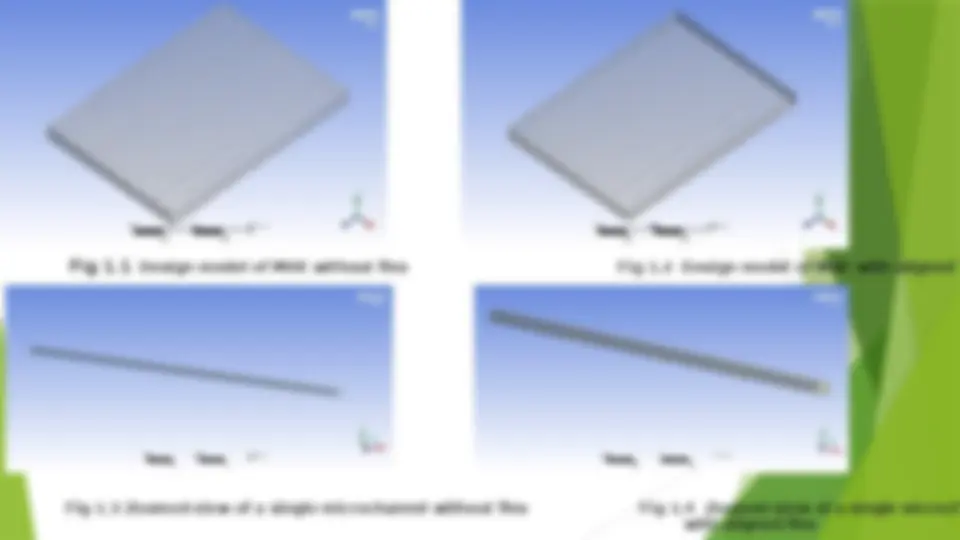
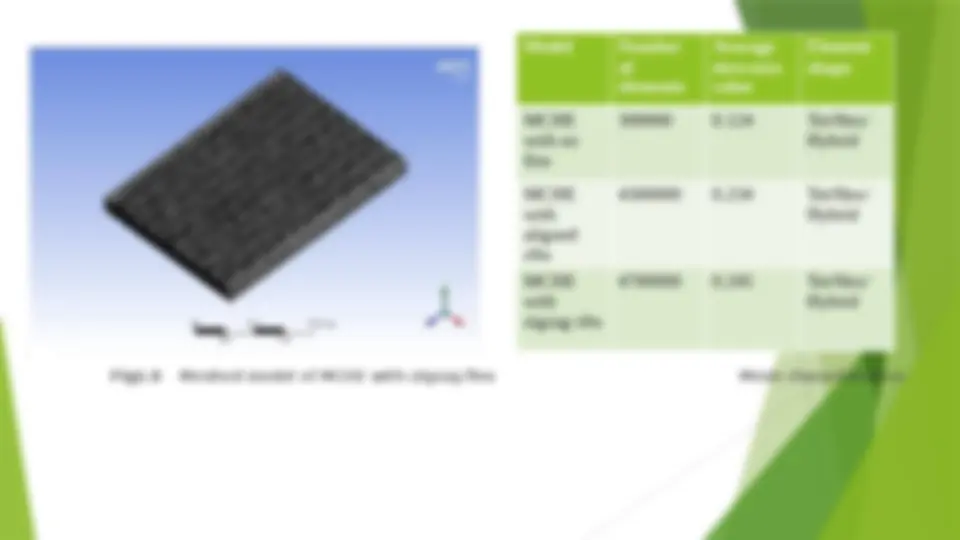
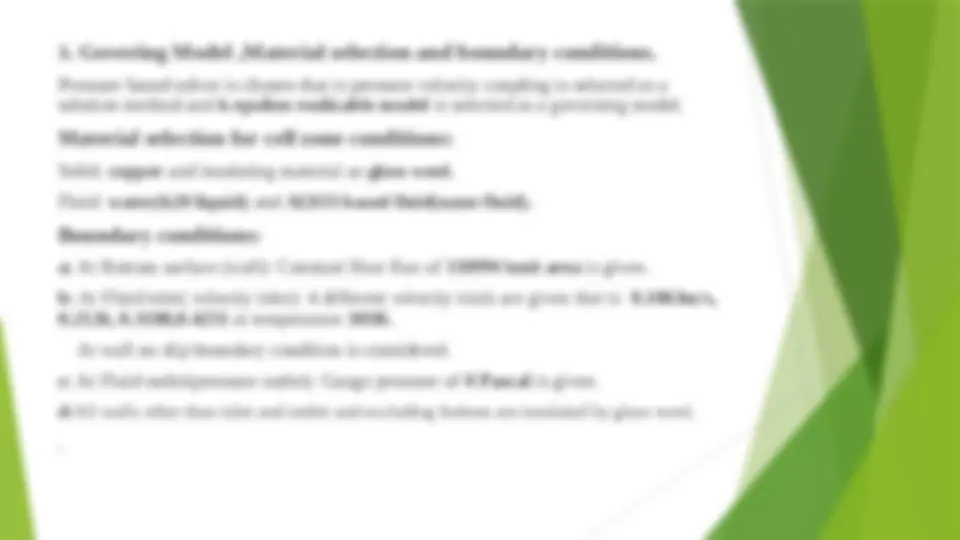
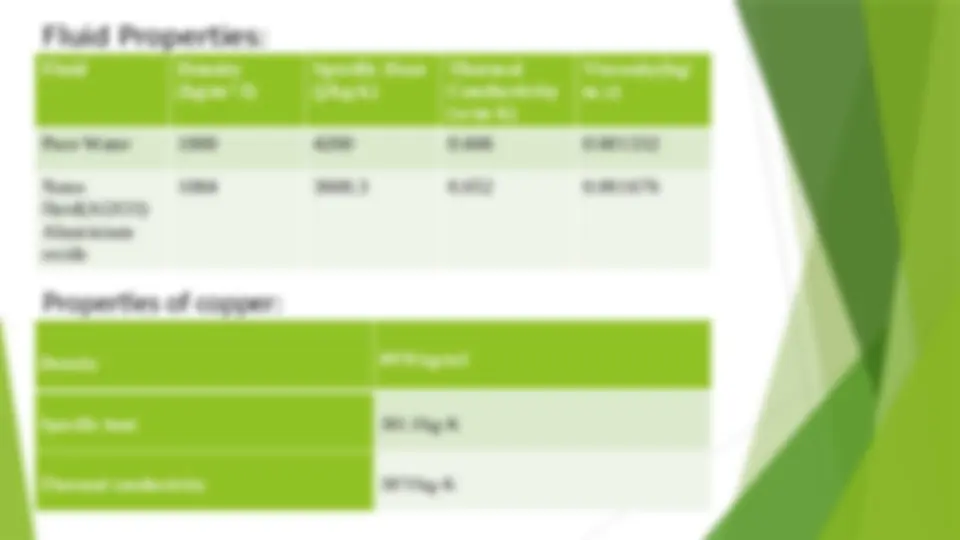
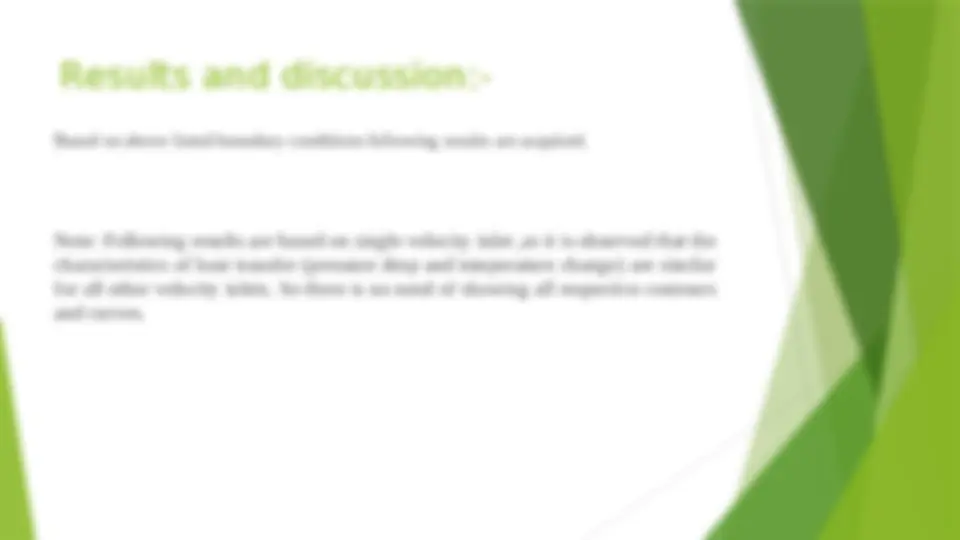
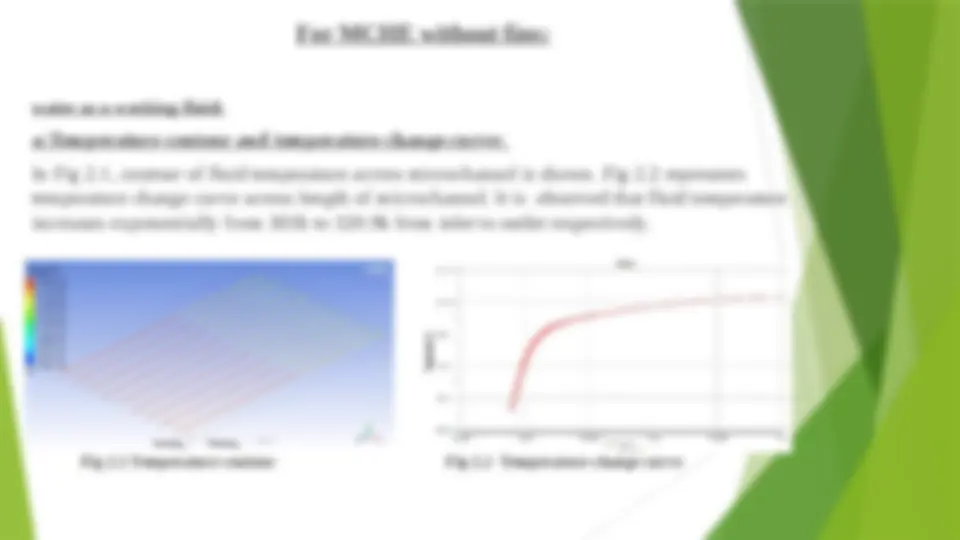
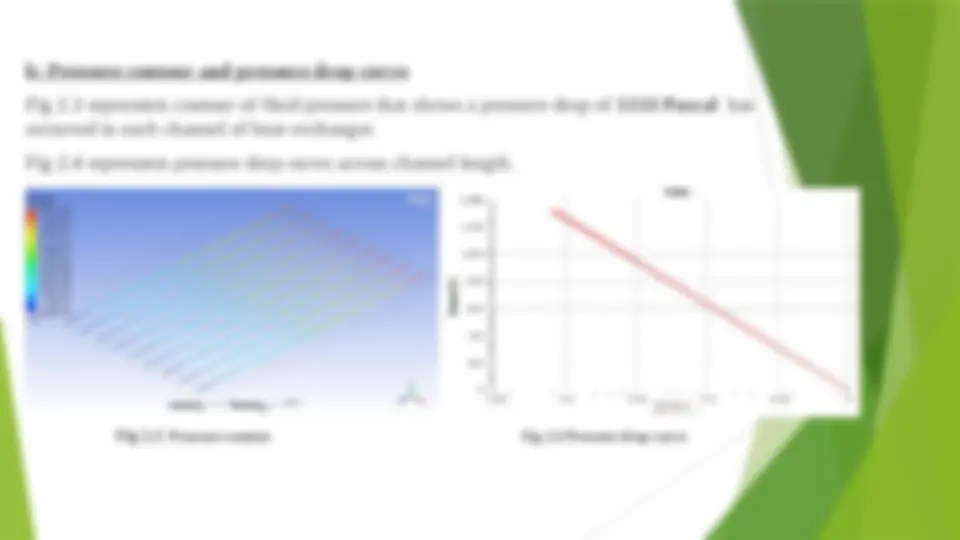
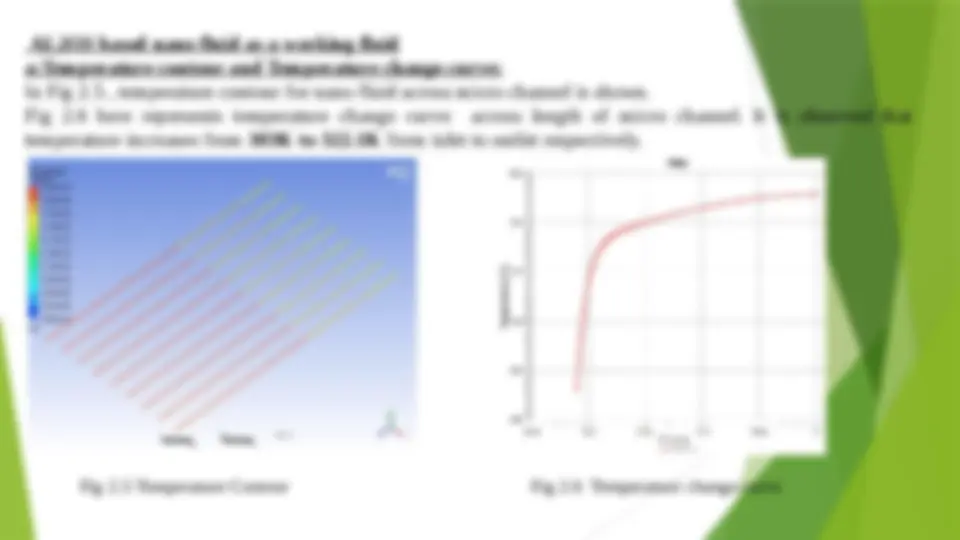
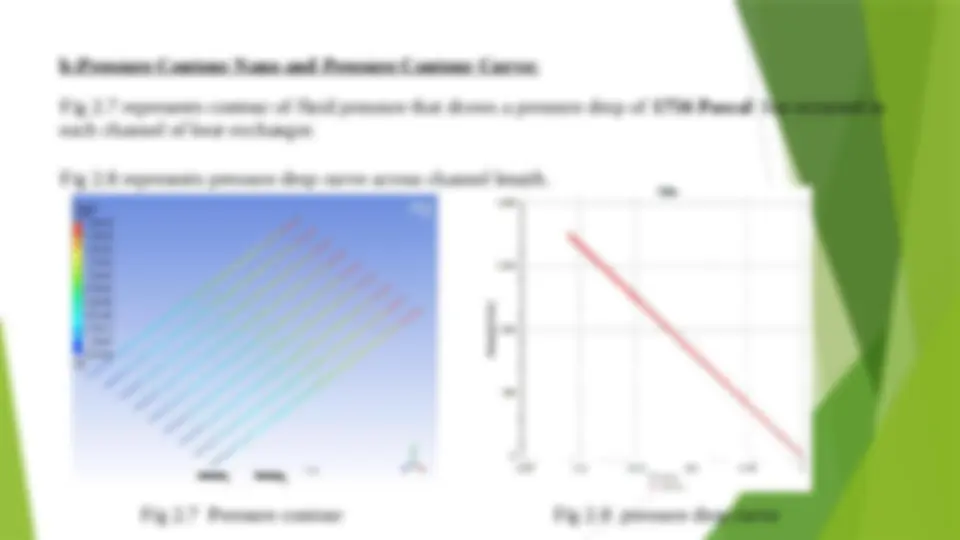
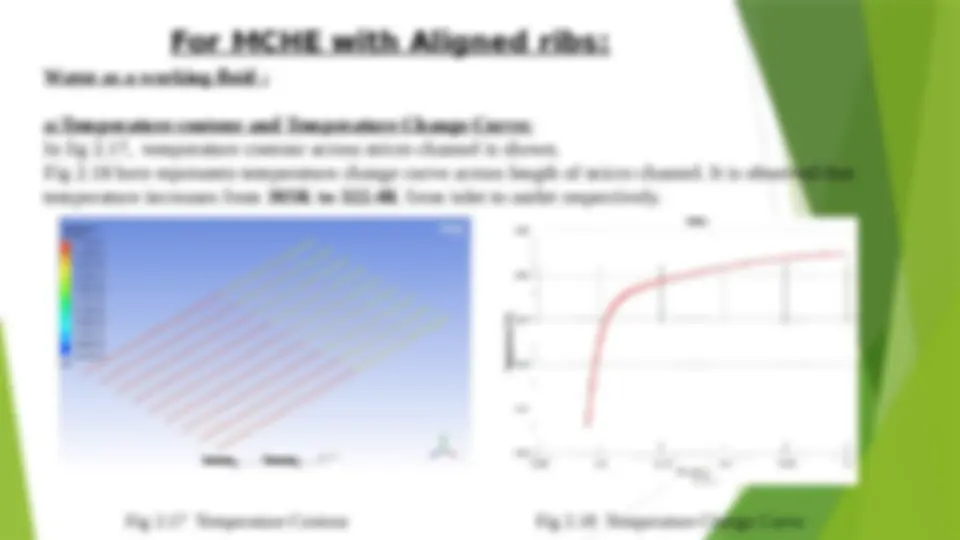
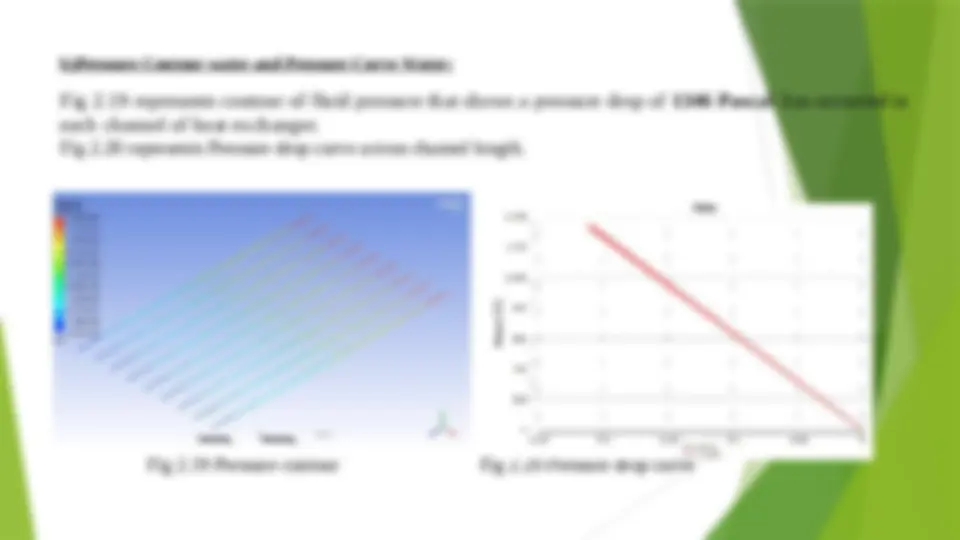
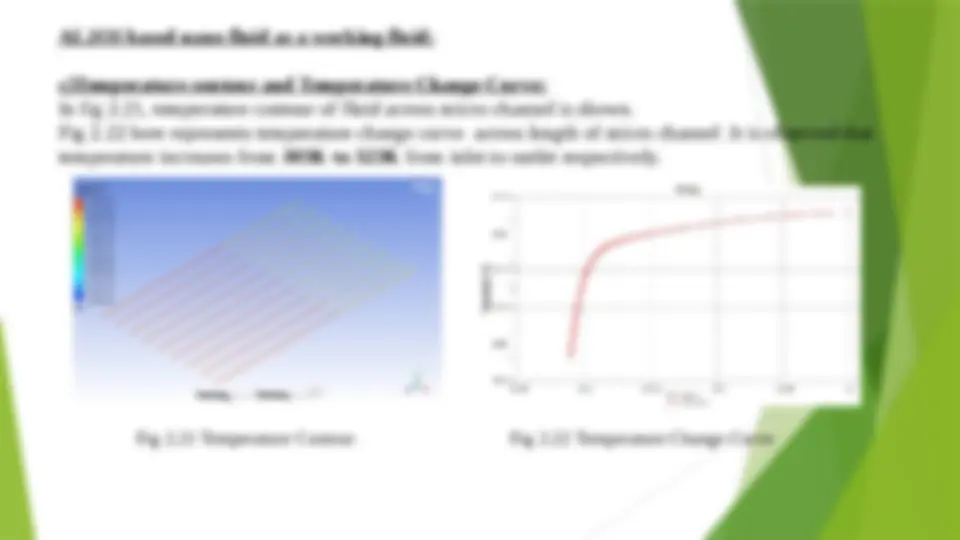
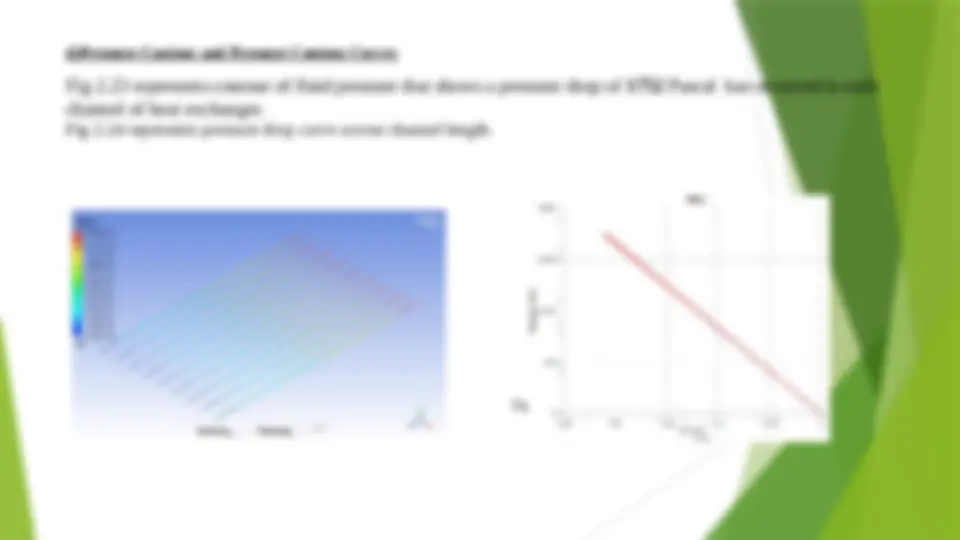

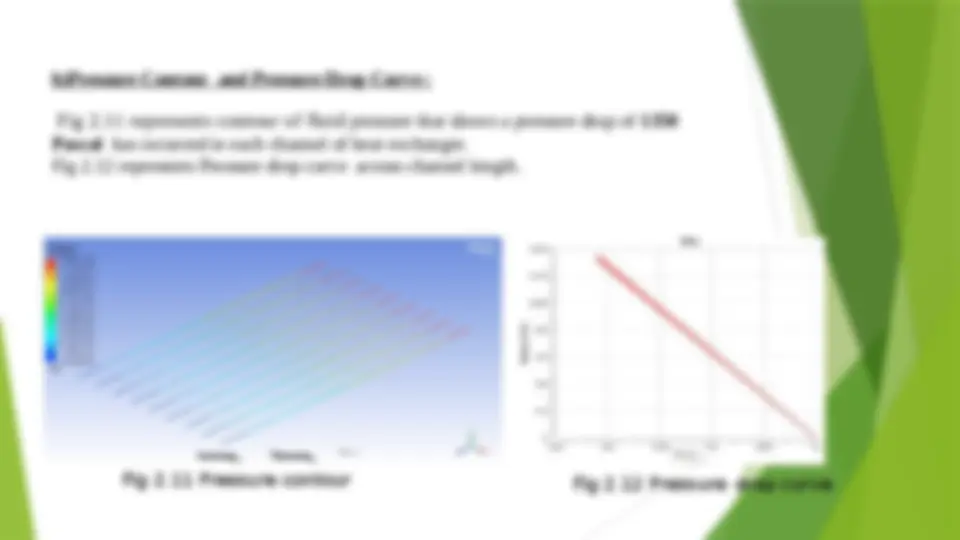

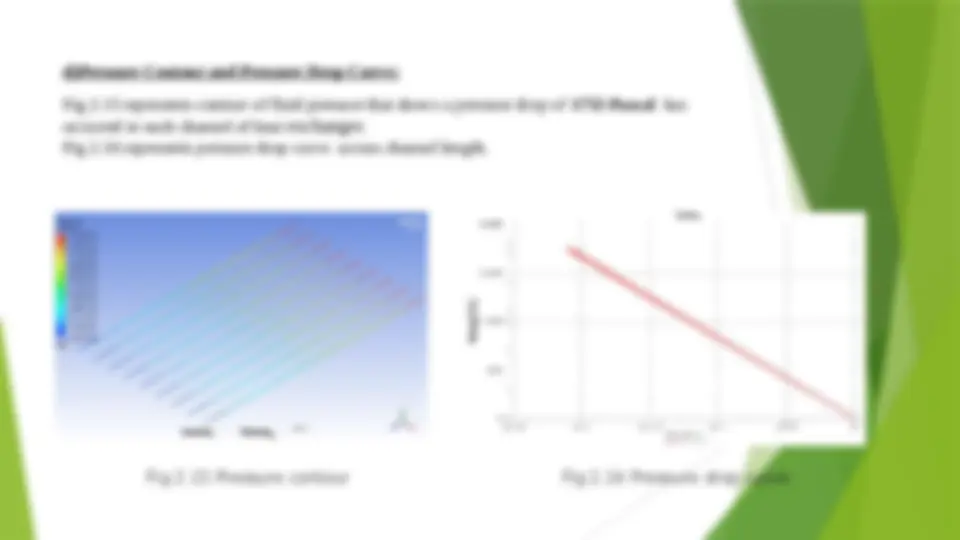
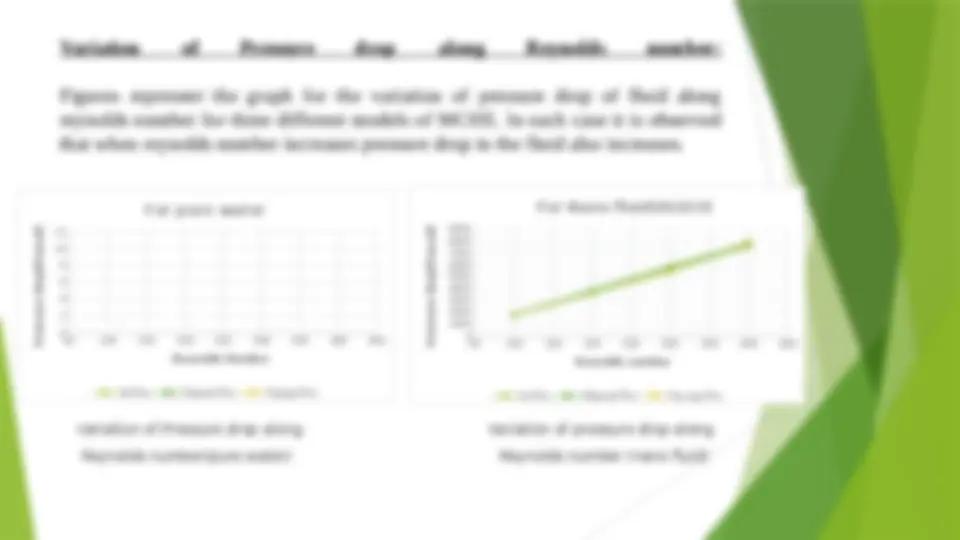
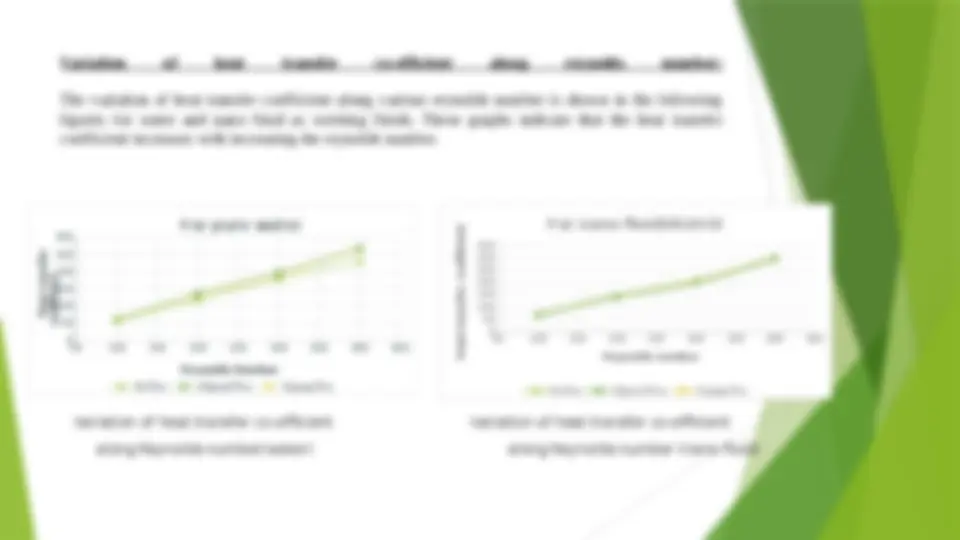
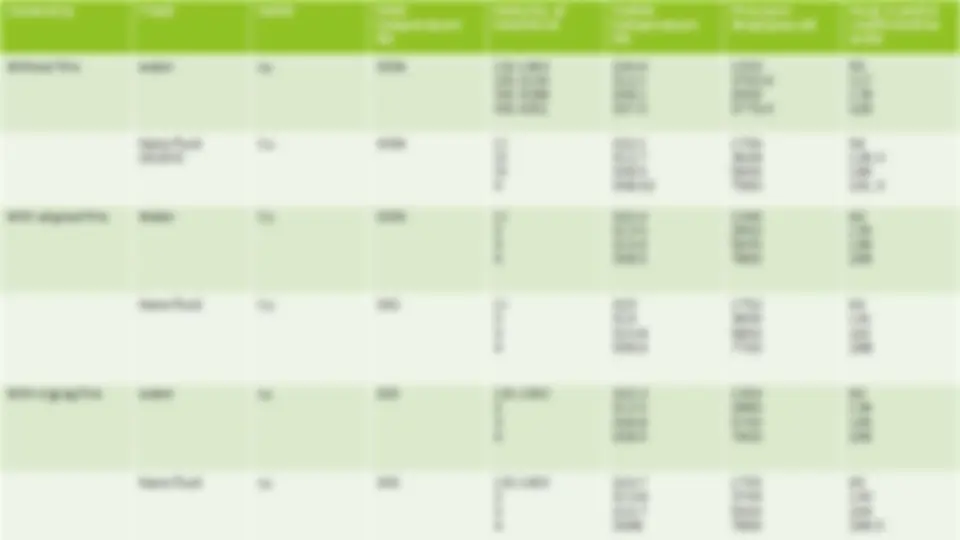
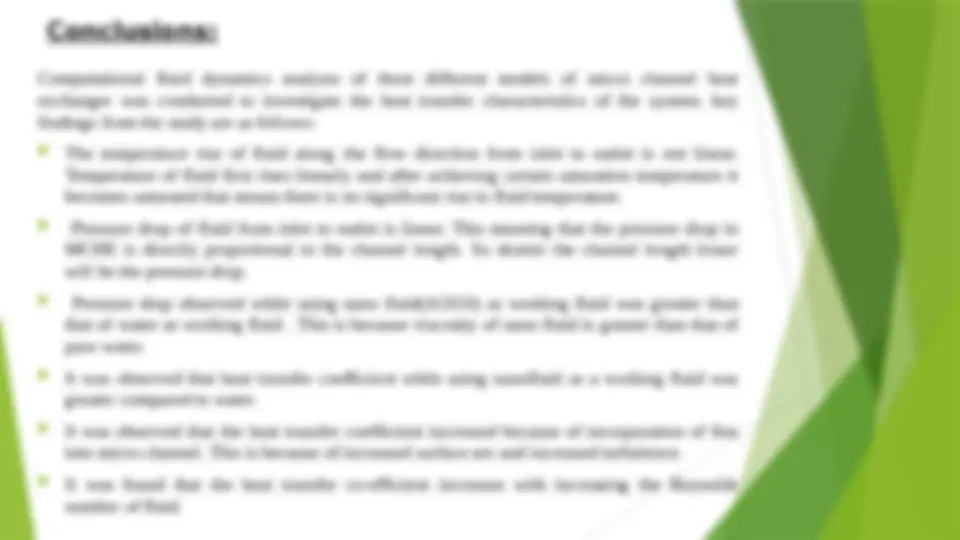
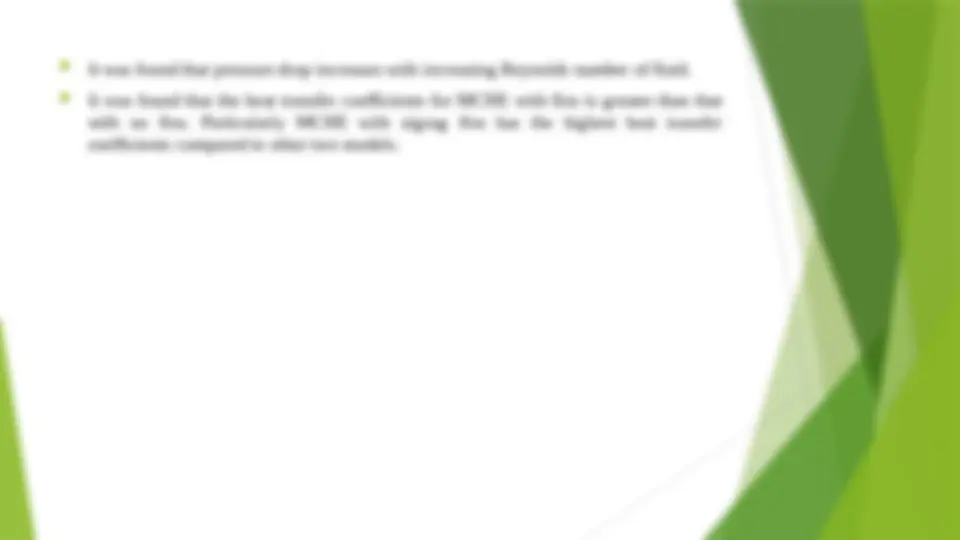
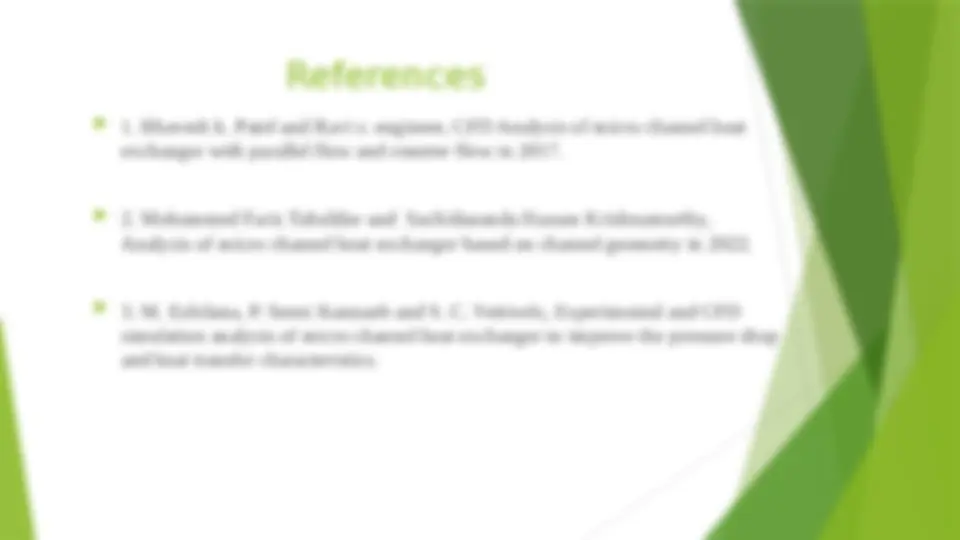
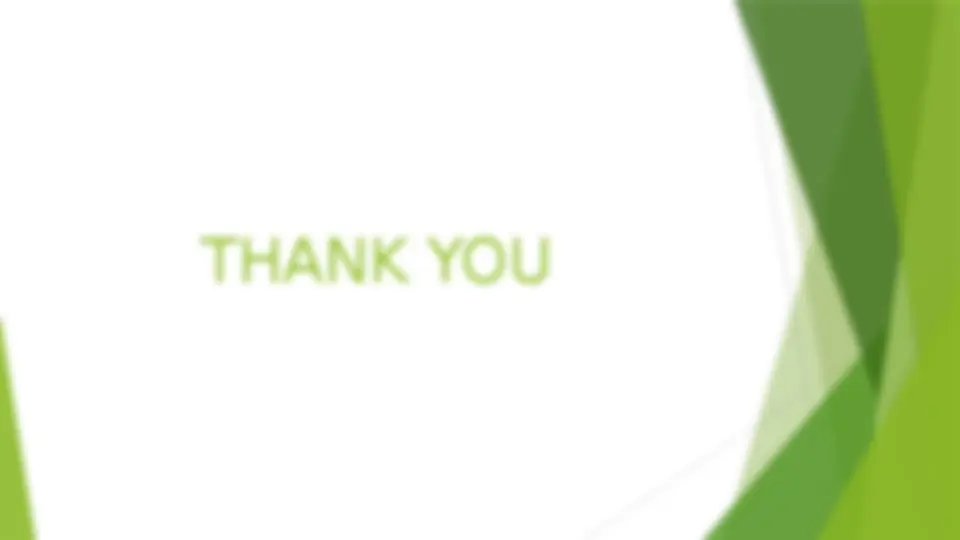
Study with the several resources on Docsity
Earn points by helping other students or get them with a premium plan
Prepare for your exams
Study with the several resources on Docsity
Earn points to download
Earn points by helping other students or get them with a premium plan
Community
Ask the community for help and clear up your study doubts
Discover the best universities in your country according to Docsity users
Free resources
Download our free guides on studying techniques, anxiety management strategies, and thesis advice from Docsity tutors
This presentation explores the heat transfer characteristics of mini heat exchangers with and without ribs through computational fluid dynamics (cfd) analysis. The study reveals deviations in heat transfer and fluid flow characteristics in microscale devices compared to conventionally-sized devices. Microchannel heat exchangers, which consist of narrow, parallel channels, offer high heat transfer rates and efficient thermal management. The investigation of heat transfer characteristics, optimization of mini heat exchanger design, and the results obtained from cfd simulations for three different models of mini heat exchangers.
Typology: Lecture notes
1 / 37
This page cannot be seen from the preview
Don't miss anything!
By Syed Abid Hussain Waqas Ibni Tariq Sanketh M. Patil Aamir Rasool Kumar Guide Name :Dr. P B Nagaraj
(^) A heat exchanger is a device that is used to transfer thermal energy between two or more fluids, between a solid surface and a fluid, or between solid particulates and a fluid, at different temperatures and in thermal contact. (^) The trend towards miniaturization and the advances in microfabrication have led to the application of microchannels for thermal management in many areas. (^) Microchannels have received considerable attention particularly in the areas of experimental , analytical and numerical studies. These studies revealed deviations in the heat transfer and fluid flow characteristics in microscale devices from those of conventionally-sized devices. (^) Microchannel heat exchanger is the type of compact heat exchanger that consists of a series of narrow, parallel channels through which fluids flow. These channels are typically less than 1 mm in size and are separated by thin walls or fins that serve as the heat transfer surface. The design of microchannel heat exchangers allows for a large surface area relative to the overall size of the device, which enables high heat transfer rates and efficient thermal management. (^) The performance of a microchannel heat exchanger depends very much on the aspect ratio of the channels. (^) In spite of the widespread use of micro heat exchangers in the process and automotive industries, there is limited published literature and attempts at designing them for optimal performance.
The objective of this project is to study the heat transfer characteristics of a mini heat exchanger with or without ribs by using computational fluid dynamics. Following are some key objectives of this work: (^) To model and simulate the heat transfer process in a mini heat exchanger using Computational Fluid Dynamics (CFD). (^) To investigate the heat transfer characteristics like pressure drop ,temperature change etc across length of channels of micro channel heat exchanger. (^) To investigate the effect of varying flow rates and inlet temperatures on the thermal performance of the mini heat exchanger. (^) To optimize the design of the mini heat exchanger for improved heat transfer efficiency and effectiveness.
3. Experimental and CFD simulation analysis of micro channel heat exchanger to improve the pressure drop and heat transfer characteristics by M. Ezhilana, P. Seeni Kannanb and S. C. Vettivelc.
Pre-Processing
Fig 1.1 Design model of MHE without fins Fig 1.2 Design model of MHE with aligned fi Fig 1.3 Zoomed view of a single microchannel without fins Fig 1.4 Zoomed view of a single microch with aligned fins
Fig1.5 Design model of MHE with zig zag fins Fig1.6 Zoomed view of a single microchannel with zigzag fins
Fig1.9 Meshed model of MCHE with zigzag fins Mesh characteristics Model Number of elements Average skewness value Element shape MCHE with no fins 300000 0.124 Tet/Hex/ Hybrid MCHE with aligned ribs 4300000 0.234 Tet/Hex/ Hybrid MCHE with zigzag ribs 4700000 0.245 Tet/Hex/ Hybrid
3. Govering Model ,Material selection and boundary conditions.
Material selection for cell zone conditions:
Boundary conditions:
d: All walls other than inlet and outlet and excluding bottom are insulated by glass wool.
4: Solving For solving the problem, under pressure velocity coupling following things are considered: Under Scheme: SIMPLE is selected. Under Spatial discretization: Following are selected; Gradient: Least square cell based. Pressure : 2nd^ order. Momentum: 2nd^ order upwind. Turbulent kinetic energy: 2 nd order upwind. Turbulent dissipation rate: 2nd^ order upwind. Energy : 2 nd order upwind. Initialization of calculation is given as velocity inlet.
Residual graph of MCHE without fins Residual graph with aligned fins Residual graph with zigzag fins
For MCHE without fins: water as a working fluid:
Fig 2.1 Temperature contour Fig 2.2 Temperature change curve
Fig 2.3 Pressure contour Fig 2.4 Pressure drop curve