
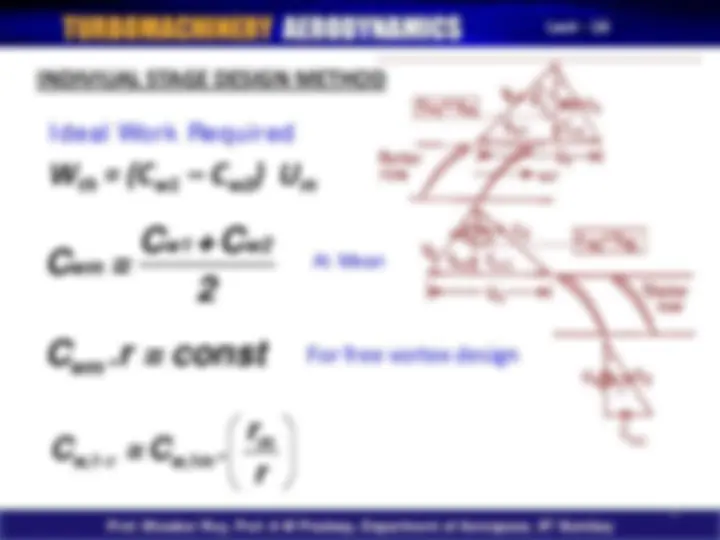
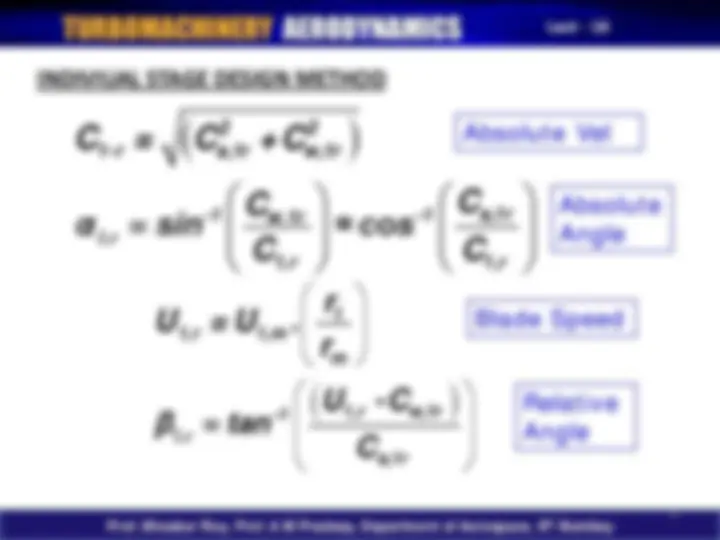
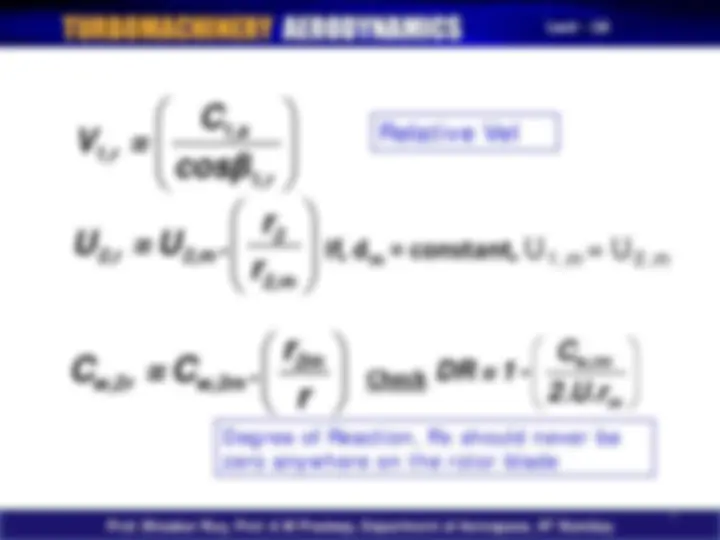
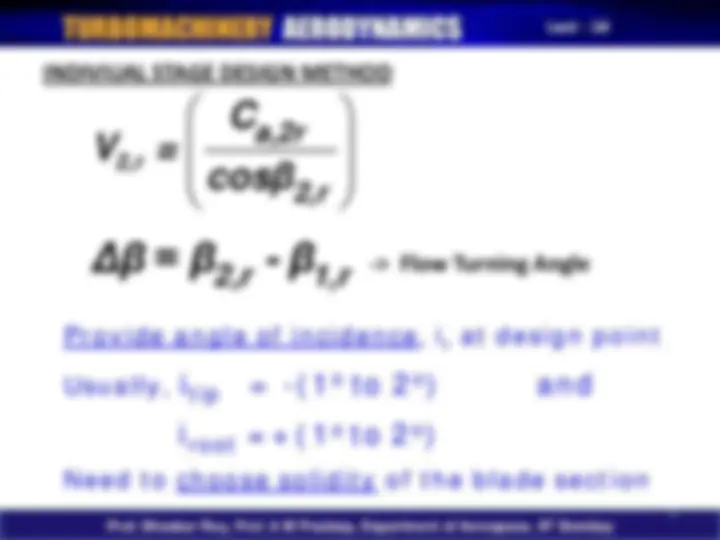
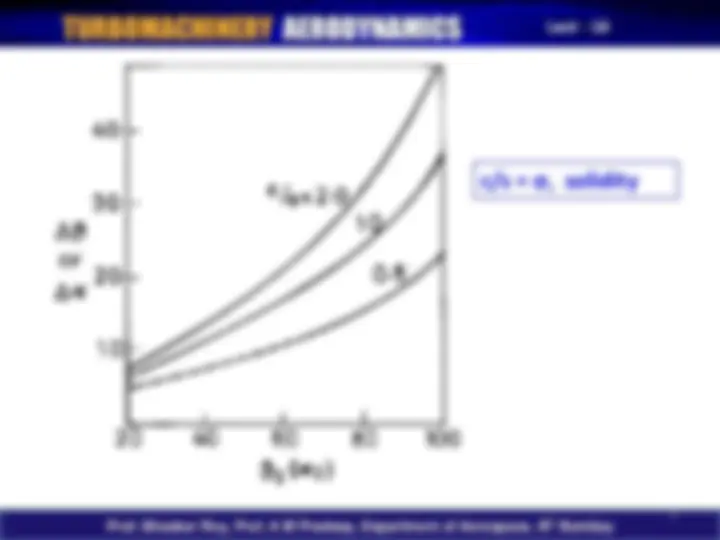
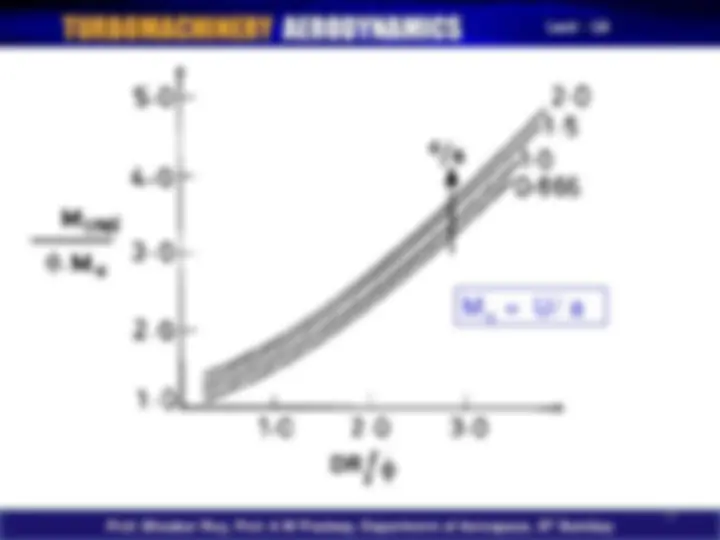
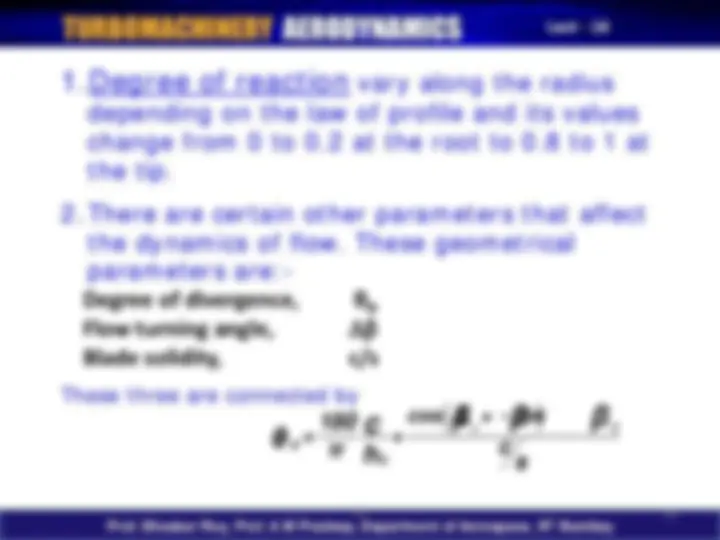
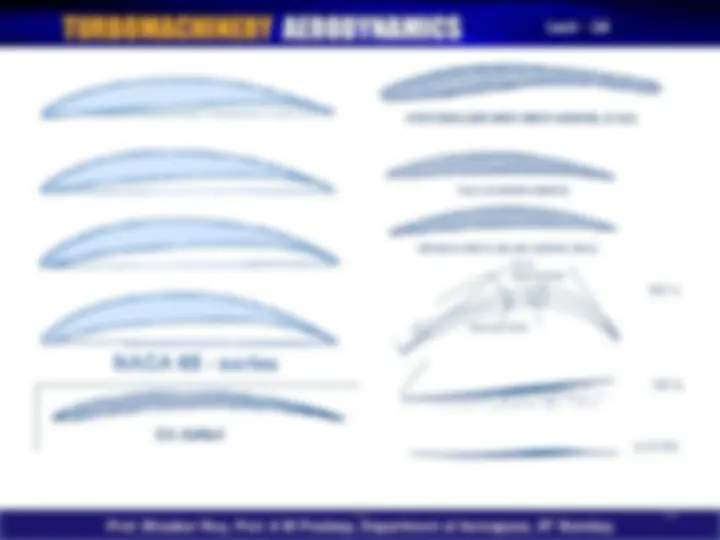
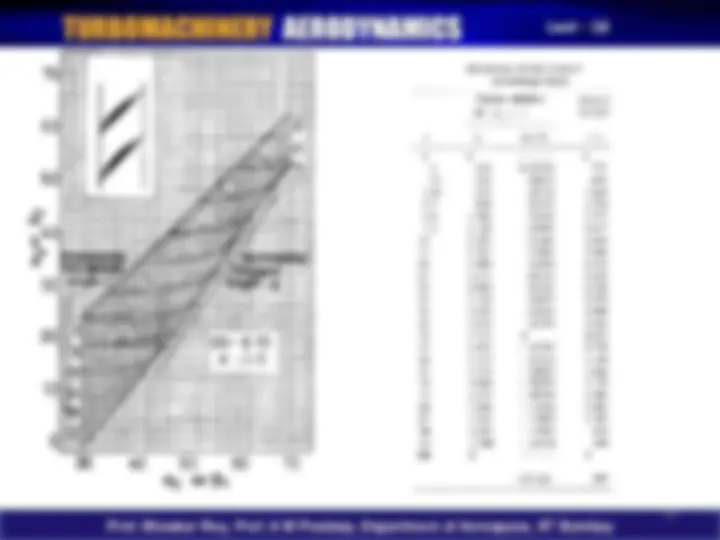
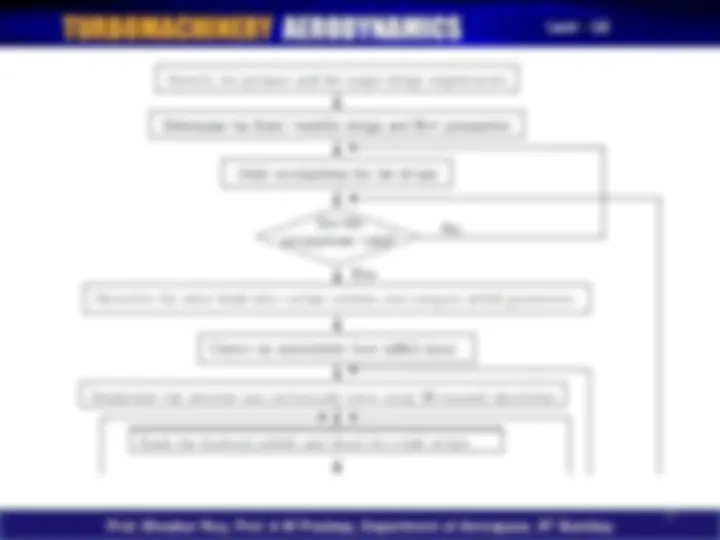
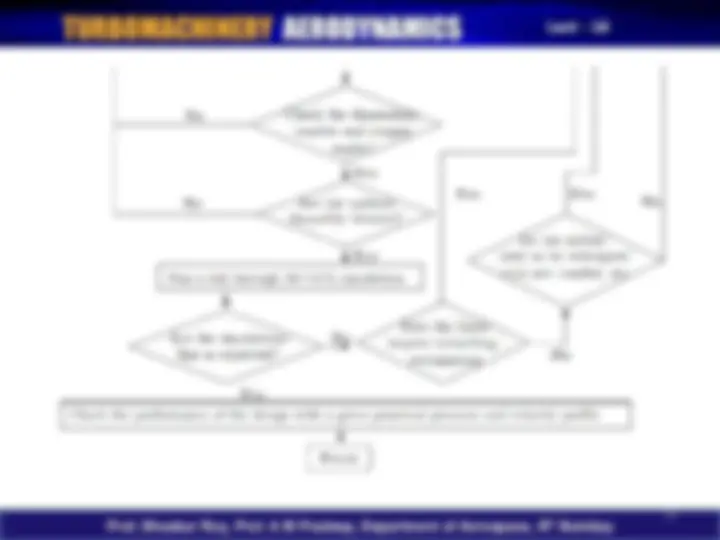
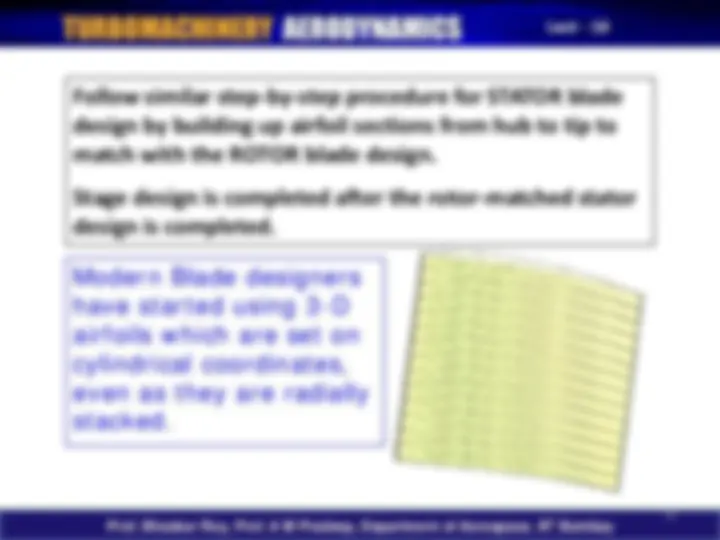
Study with the several resources on Docsity
Earn points by helping other students or get them with a premium plan
Prepare for your exams
Study with the several resources on Docsity
Earn points to download
Earn points by helping other students or get them with a premium plan
Community
Ask the community for help and clear up your study doubts
Discover the best universities in your country according to Docsity users
Free resources
Download our free guides on studying techniques, anxiety management strategies, and thesis advice from Docsity tutors
Some concept of Turbomachinery Aerodynamics are Axial Flow Compressors, Axial Turbine Design Considerations, Blade Performance, Engine Performance Significantly, Flows Through Axial Compresso. Main points of this lecture are: Blade Design Procedure, Design Method, Indiviual Stage, Ideal Work, Transonic Fan, Fan Design, Rarely Used, Possibility, Carter’S Deviation, Design Point
Typology: Slides
1 / 20
This page cannot be seen from the preview
Don't miss anything!
1
Aerodynamic Design of Axial Compressor
---------------- Blade design Procedure
2 2
-1 (^) w.1r -1^ a,1r
1,r 1,r
1 1,r 1,m m
-1^ 1,r^ w,1r
a,1r
INDIVIUAL STAGE DESIGN METHOD
Absolute Vel
Absolute Angle
Blade Speed
Relative Angle
1,a 1,r 1,r
C V = cos β
2 2,r 2,m 2,m
r U = U. r
2m w,2r w,2m
r C = C. r
w,rm m
C DR = 1 - 2.U.r
Check
Relative Vel
Degree of Reaction, Rx should never be zero anywhere on the rotor blade
or assume a value for
AVDR = C (^) a1. ρ 1 /C (^) a2. ρ 2
-1 w,2r 2,r a,2r
(^) ( )
-1 2,r^ w,2r 2,r a,2r
U - C β = tan C
Δβ = β 2,r (^) - β 1,r
≈ 1 0.
V 2 <V 1 →
V 2 =V 1 →
V 2 >V 1 →
Generally accepted
Rarely Used
transonic fan design – possibility
INDIVIUAL STAGE DESIGN METHOD
2,r
C V = cos β
Δβ = β 2,r (^) - β 1,r -> Flow Turning Angle
Provide angle of incidence, ir at design point
Need to choose solidity of the blade section
M (^) u = U/a
INDIVIUAL STAGE DESIGN METHOD
r• 2,r^ ′ 2,r r
s δ = β - β = m .θ. c
(Carter’s deviation – valid at design point)
At any radius
Deviation,
18
depending on the law of profile and its values change from 0 to 0.2 at the root to 0.8 to 1 at the tip.
( 1 ) D
1 c
cos Δ + - cos = 180 × c π (^) h s
c^ β^ β^ β θ
These three are connected by
19
Transonic Compressor Basic Characteristics
3-D Blade Shapes
Follow similar step-by-step procedure for STATOR blade design by building up airfoil sections from hub to tip to match with the ROTOR blade design.
Stage design is completed after the rotor-matched stator design is completed.
Modern Blade designers have started using 3-D airfoils which are set on cylindrical coordinates, even as they are radially stacked.