
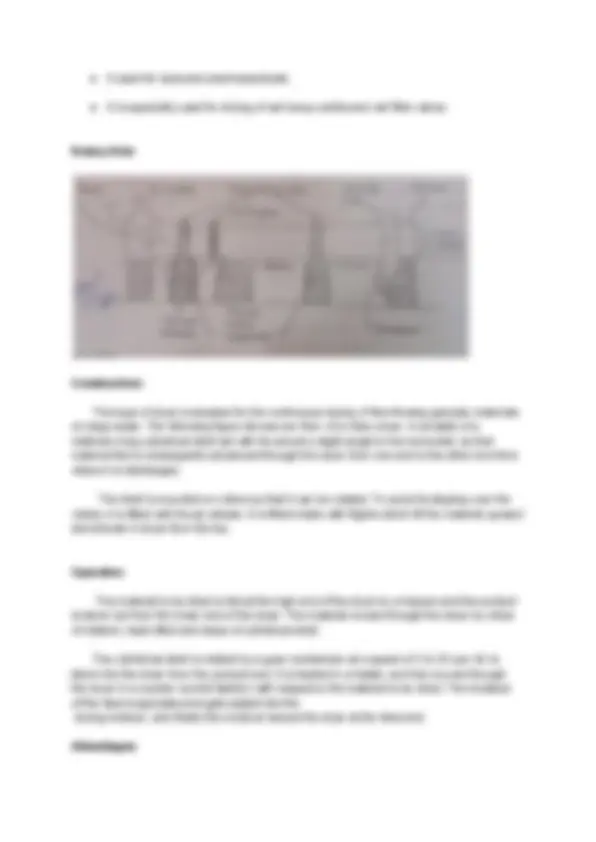
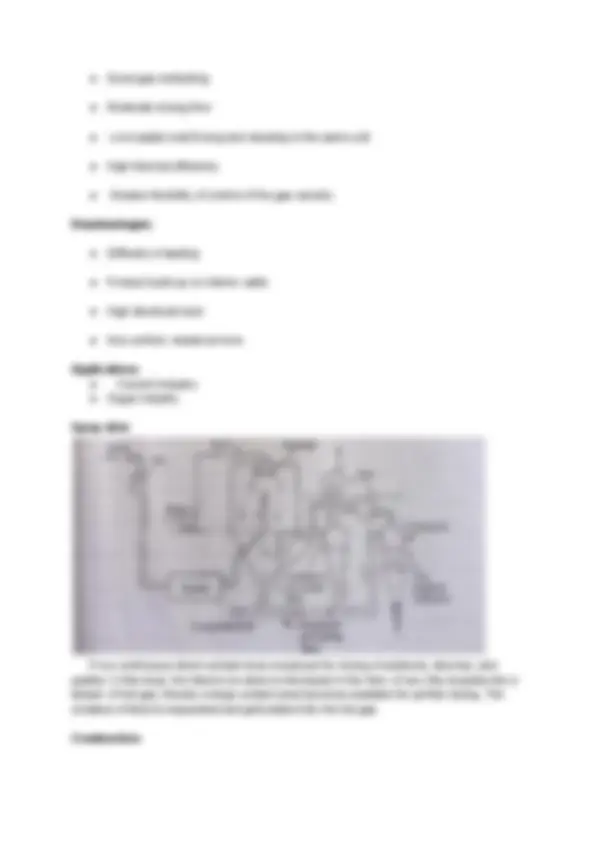
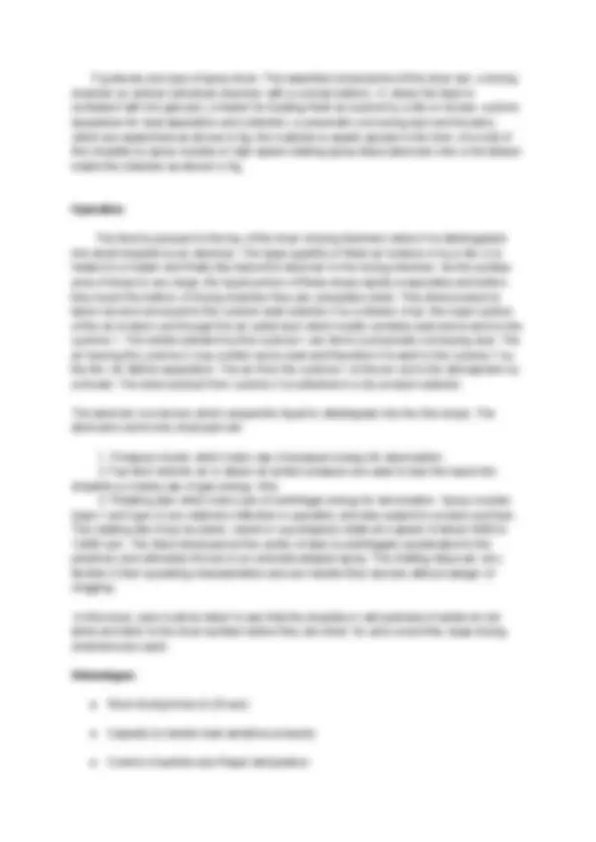
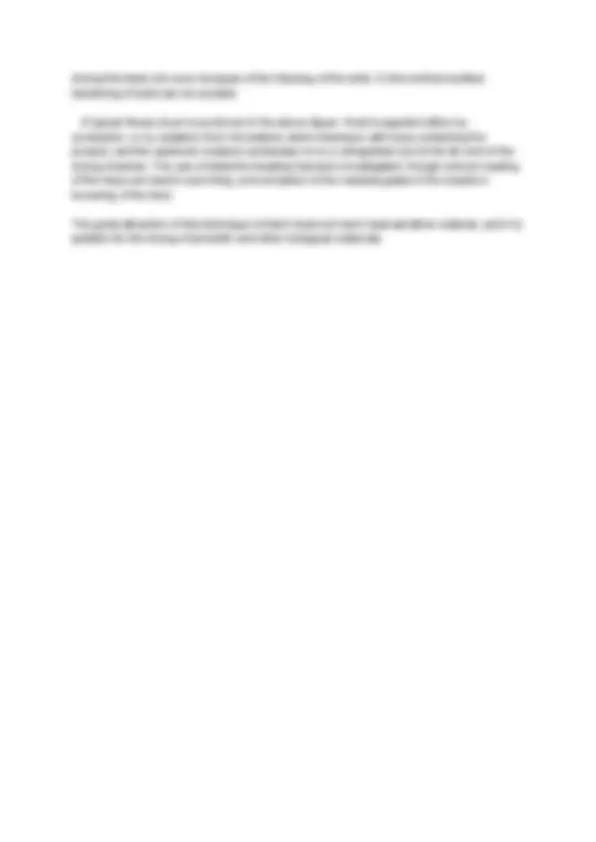
Study with the several resources on Docsity
Earn points by helping other students or get them with a premium plan
Prepare for your exams
Study with the several resources on Docsity
Earn points to download
Earn points by helping other students or get them with a premium plan
Community
Ask the community for help and clear up your study doubts
Discover the best universities in your country according to Docsity users
Free resources
Download our free guides on studying techniques, anxiety management strategies, and thesis advice from Docsity tutors
The construction and operation of batch and continuous driers, including tray driers, spray driers, fluidized bed driers, and freeze driers. It describes the advantages and disadvantages of each type of drier and their applications. The document also explains the components of each drier and how they work. It is a useful resource for students studying chemical engineering or related fields.
Typology: Schemes and Mind Maps
1 / 8
This page cannot be seen from the preview
Don't miss anything!
Tray Drier Construction โ It is the simplest of the batch dryer and also known as cabinet or compartment dryer. The tray dryer shown in the following figure is a batch operated direct dryer. โ It consists of an enclosed insulated cabinet or large compartment into which the material to be dried is placed on a number of removable trays. โ The trays may either be fabricated from sheets or from screens. โ The trays may be stacked on racks or loaded on trucks. โ It is provided with the inlet outlet connections for air. โ A heating coil either electrical or steam heating is incorporated in it. โ In these dryers, steam, gas or electrically heated air is used as a drying medium. โ The air is circulated in the dryer over the trays by means of fan fitted at the top or at the side.
Operation โ The material to be dried is sprayed over the trays and put into the cabinet and then it is closed. โ The steam is continuously passed through the coil and fan is started. โ Air is heated by heating coils, its relative humidity decreases (i.e. its capacity to evaporate the moisture is increased) and hot air then passes over the trays. โ The moisture is evaporated from the wet solid feed, gets added in air and finally air leaves the dryer though the outlet. โ The process is continued until the solids are dried, the cabinet is then opened, dried material is removed from trays and afresh batch is charged. โ To avoid heat loss about 80 - 95% of air is recirculated by adjusting a damper at the outlet, and the remaining portion is exhausted out, and the same amount of air is taken in through the inlet. โ Trays are usually made up of stainless steel, steel, enameled iron etc. and are fabricated from sheets of 3 mm to 6 mm thick. Advantages โ It is cheap and easy to construct โ Low space requirement. โ Ease of cleaning. โ *Requires very low maintenance. โ No loss of product during drying. Disadvantages โ It is expensive to operate due to high labour requirement for loading and unloading the dryer. โ Long drying time (4 to 48 hrs per batch) Small quantities are handled. Applications
โ Good gas contacting โ Moderate drying time โ Low capital cost Drying and cleaning in the same unit โ High thermal efficiency โ Greater flexibility of control of the gas velocity. Disadvantages: โ Difficulty of sealing โ Product build-up on interior walls โ High structural load โ Non-uniform residence time Applications โ Cement industry โ Sugar industry Spray drier It is a continuous direct contact dryer employed for drying of solutions, shurries, and pastes. In this dryer, the feed to be dried is introduced in the form of very fine droplets into a stream of hot gas, thereby a large contact area becomes available for perfect drying. The moisture of feed is evaporated and gets added into the hot gas Construction
Fig shows one type of spray dryer. The essential components of this dryer are: a drying chamber (a vertical cylindrical chamber with a conical bottom). O where the feed is contacted with hot gas (air), a heater for heating fresh air sucked by a fan or blower, cyclone separators for dust separation and collection, a pneumatic conveying duct and blowers, which are assembled as shown in fig. the material is usually spread in the form of a mist of fine droplets by spray nozzles or high speed rotating spray discs (atomizer) into a hot stream inside the chamber as shown in fig. Operation The feed is pumped to the top of the dryer (drying chamber) where it is disintegrated into small droplets by an atomizer. The large quantity of fresh air is taken in by a fan, it is heated in a heater and finally fed below the atomizer in the drying chamber. As the surface area of drops is very large, the liquid portion of these drops rapidly evaporates and before they touch the bottom of drying chamber they are completely dried. This dried product is taken out and conveyed to the cyclone dust collector-2 by a stream of air, the major portion of the air is taken out through the air outlet duct which mostly contains dust and is sent to the cyclone-1. The solids collected by this cyclone-1 are fed to a pneumatic conveying duct. The air leaving the cyclone-2 may contain some dust and therefore it is sent to the cyclone-1 by the fan, for farther separation. The air from the cyclone-1 is thrown out to the atmosphere by a blower. The dried product from cyclone-2 is collected in a dry product collector. The atomizer is a device which causes the liquid to disintegrate into the fine drops. The atomizers commonly employed are
โ In this dryer hot gav air is passed through a wet material at a velocity sufficiently high to fluidize the wet material but not too high enough to cause pneumatic conveying โ Fluidized bed system in addition to a fluidizing chamber also needs an air blower, a hot air generator, a feed conveyer, a cyclone separator and a product conveyor. โ In this dryer, hot air is used to keep a wet feed in the fluidized state. In the dryer shown in fig, a material is dried and cooled in the same bed. โ Wet feed admitted to the top of the bed through a hopper by a rotary valve and hot air is distributed at the bottom of the bed through a diffuser plate. โ The dry product is taken out from the side or near the bottom. โ Heat and mass transfer co-efficient are high because of turbulence created at bed โ The material to be dried and hot air are in cross flow with respect to each other. The residence time can be controlled from sec to hours. โ The most air from the dryer containing lines is admitted to a cyclone separator for the recovery of fines โ It is used for drying very fine size free flowing materials, and it is well suited for heat sensitive materials โ These dryers may also be operated in batch wise. Freeze Drier In this process, the material is first frozen and then dried by sublimation in a very high vacuum 10-40 N/m, at a temperature of 240-260 K. During the sublimation of ice, a dry surface layer is left, though this is not free to move because it has been frozen and a honeycomb structure is formed. With normal vacuum drying of biological solutions containing dissolved salts, a high local salt concentration is formed at the skin, although with freeze
drying this does not occur because of the freezing of the solid. In this method surface hardening of solid can be avoided. A typical freeze dryer is as shown in the above figure. Heat is supplied either by conduction, or by radiation from hot platens which interleave with trays containing the product, and the sublimed moisture condenses on to a refrigerated coil at the far end of the drying chamber. The use of dielectric-heating has been investigated, though uneven loading of the trays can lead to scorching, and ionization of the residual gases in the results in browning of the food. The great attraction of this technique is that it does not harm heat-sensitive material, and it is suitable for the drying of penicillin and other biological materials.