
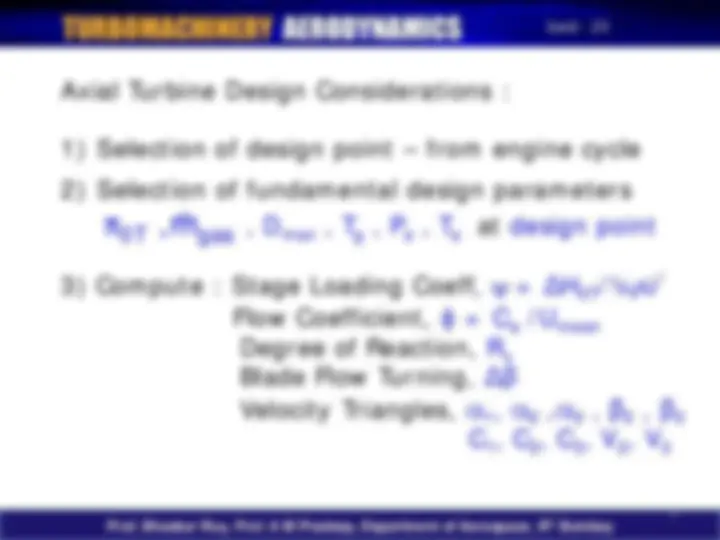
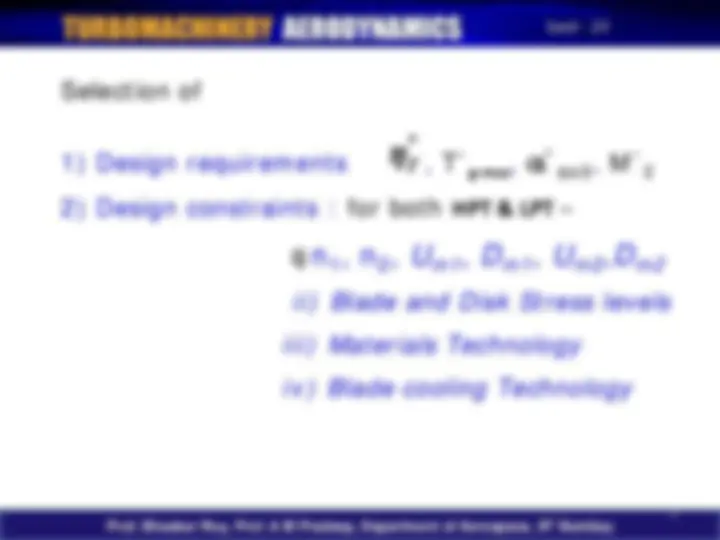
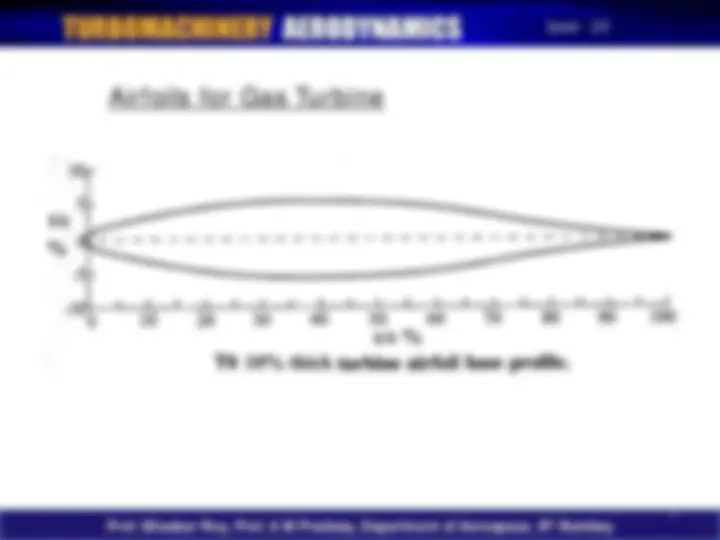
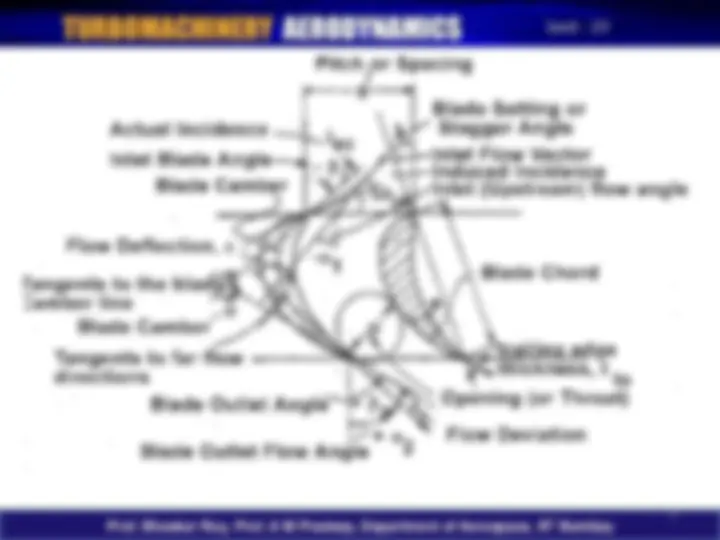
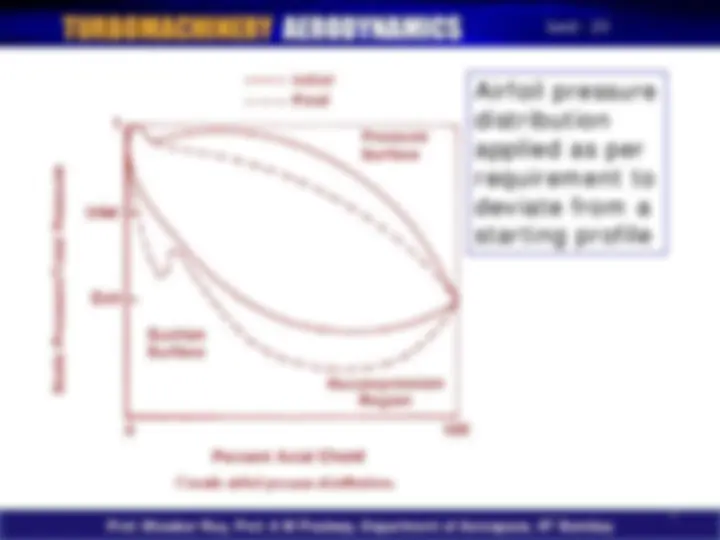
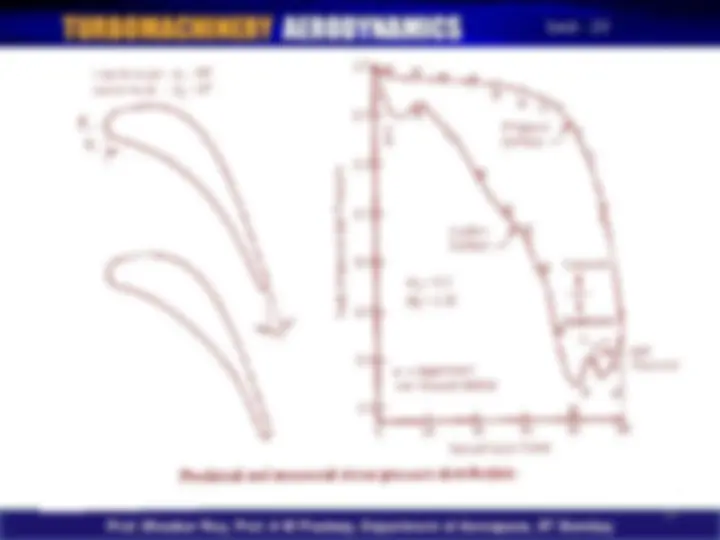
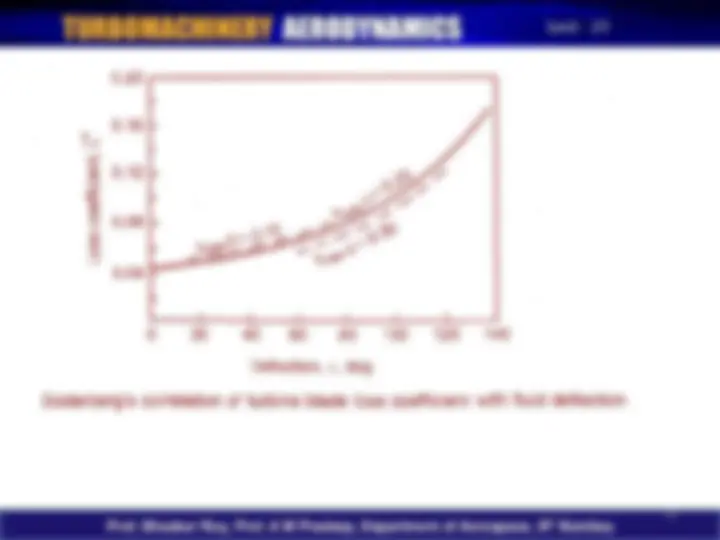
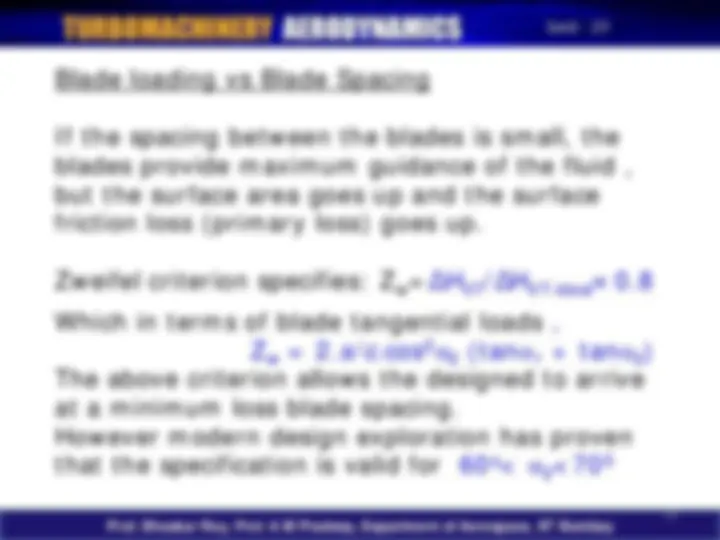
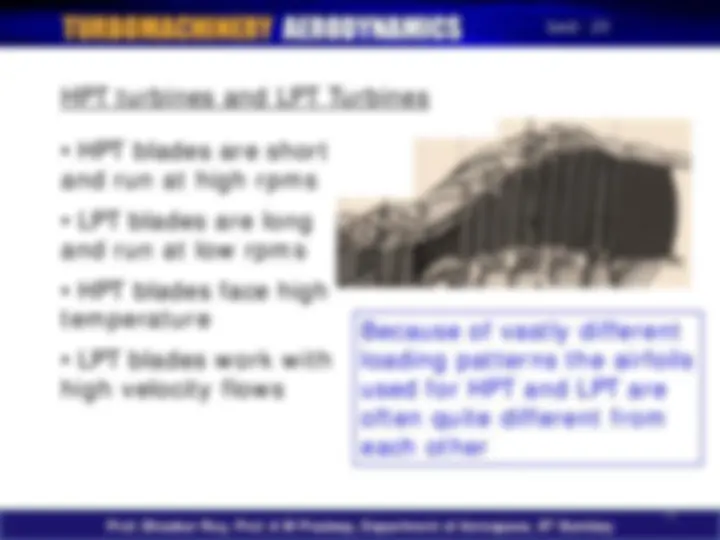
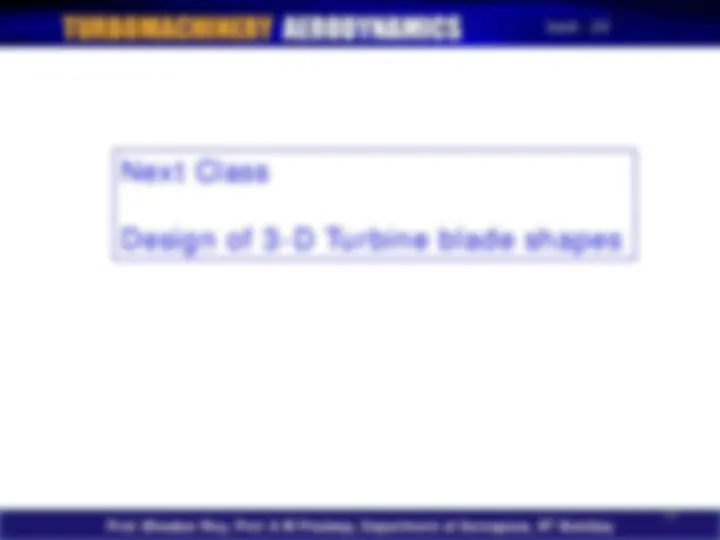
Study with the several resources on Docsity
Earn points by helping other students or get them with a premium plan
Prepare for your exams
Study with the several resources on Docsity
Earn points to download
Earn points by helping other students or get them with a premium plan
Community
Ask the community for help and clear up your study doubts
Discover the best universities in your country according to Docsity users
Free resources
Download our free guides on studying techniques, anxiety management strategies, and thesis advice from Docsity tutors
Some concept of Turbomachinery Aerodynamics are Axial Flow Compressors, Axial Turbine Design Considerations, Blade Performance, Engine Performance Significantly, Flows Through Axial Compresso. Main points of this lecture are: Axial Turbine Design Considerations, Design Considerations, Axial Turbine, Turbine Design, Design Requirements, Design Constraints, Parameters, Blade Airfoil, Airfoil Pressure
Typology: Slides
1 / 18
This page cannot be seen from the preview
Don't miss anything!
1
Selection of
ii) Blade and Disk Stress levels iii) Materials Technology iv) Blade cooling Technology
__*
Airfoils for Gas Turbine
Airfoil Geometry Selection
Blade loading vs Blade Spacing
If the spacing between the blades is small, the blades provide maximum guidance of the fluid , but the surface area goes up and the surface friction loss (primary loss) goes up.
Zweifel criterion specifies: Zw =ΔH0T/ΔH0T-ideal≈ 0.
Which in terms of blade tangential loads , Zw = 2. s/c .cos^2 α 2 (tanα 1 + tanα 2 ) The above criterion allows the designed to arrive at a minimum loss blade spacing. However modern design exploration has proven that the specification is valid for 60 o^ < α 2 <70 0
Supersonic Turbine airfoils