
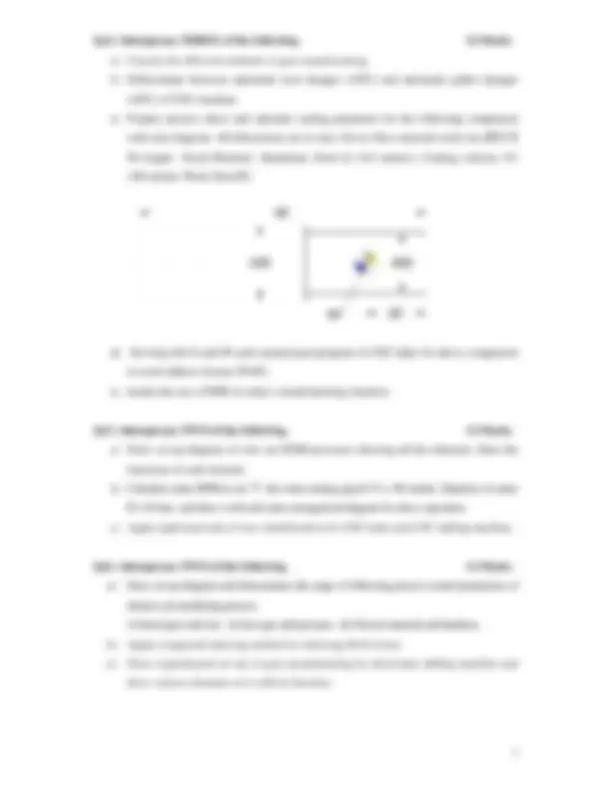
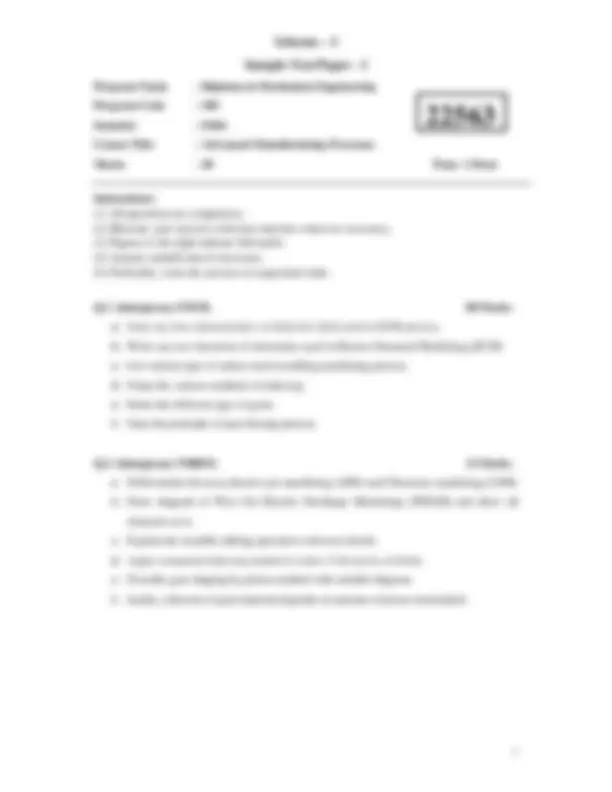
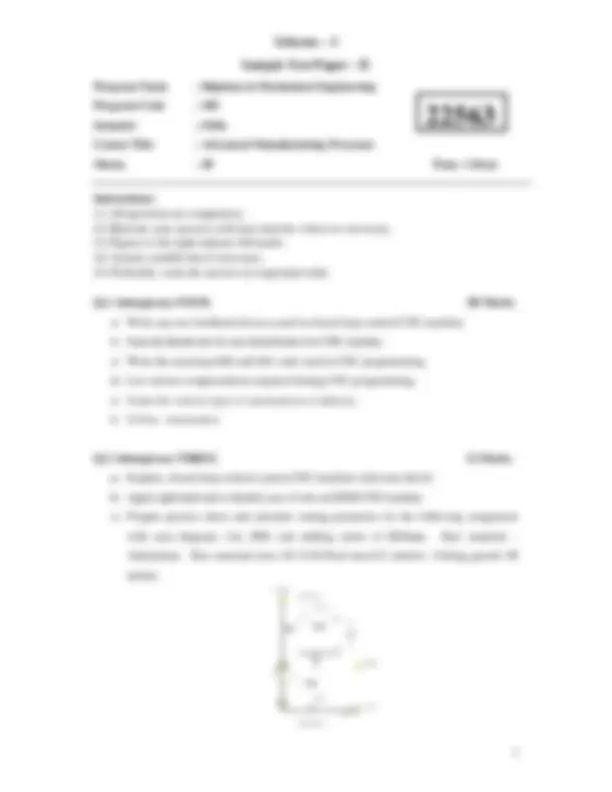
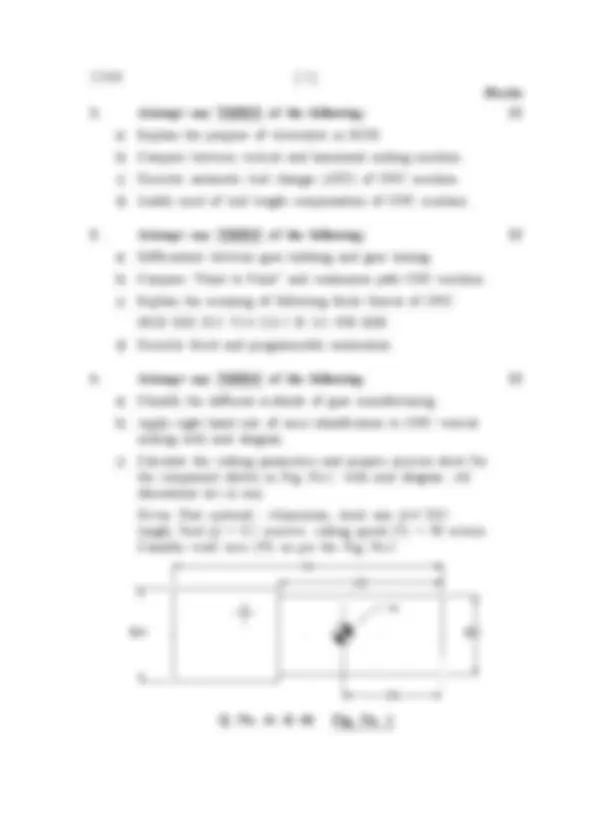
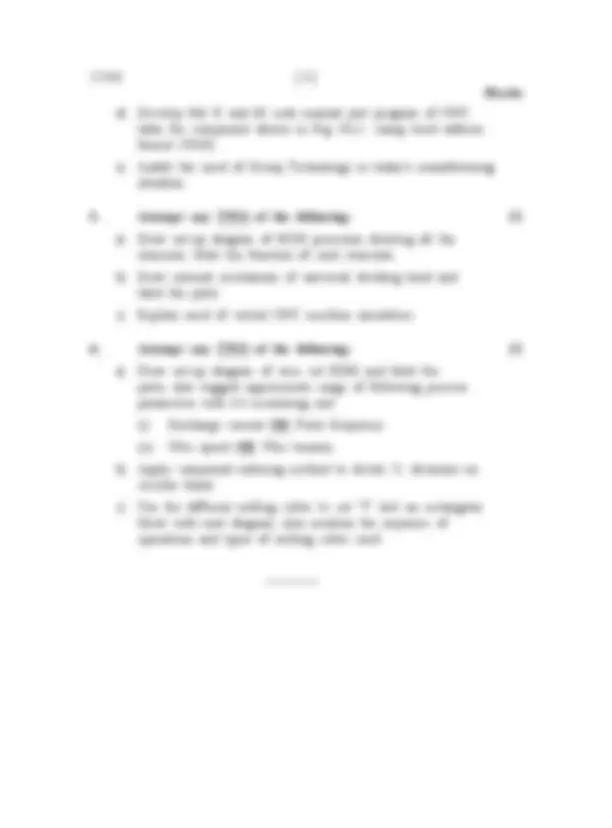
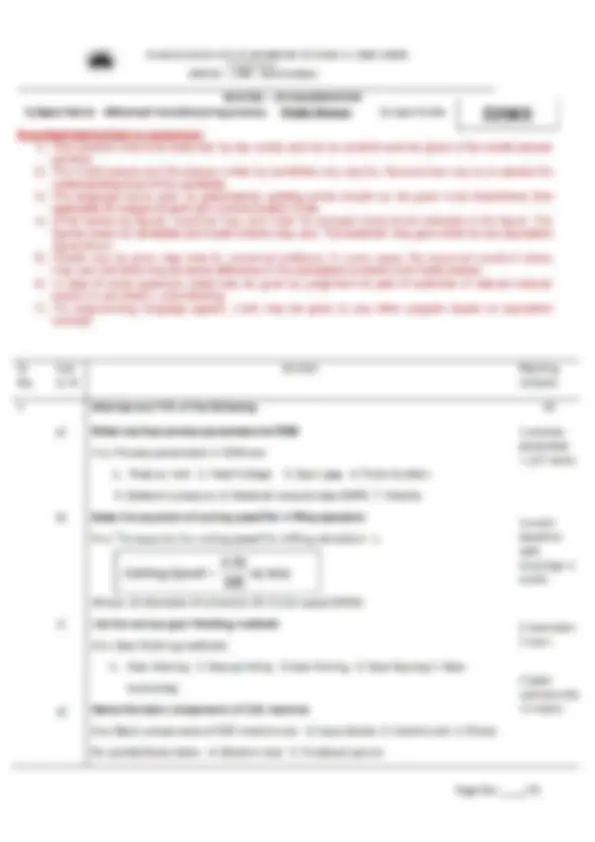
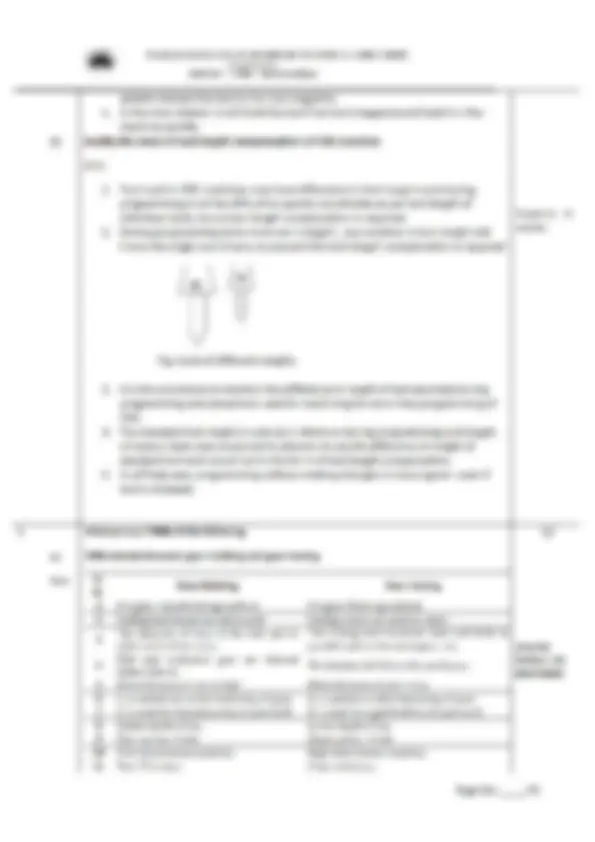
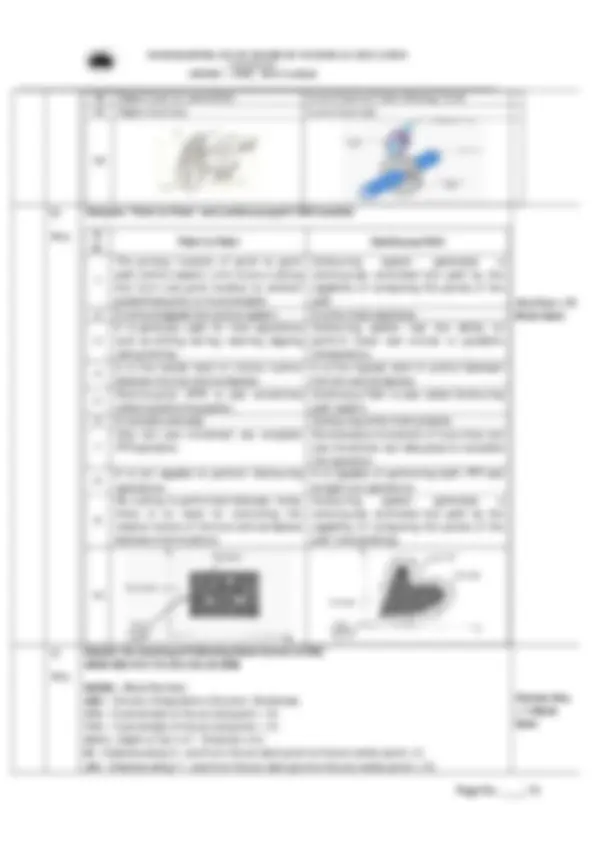
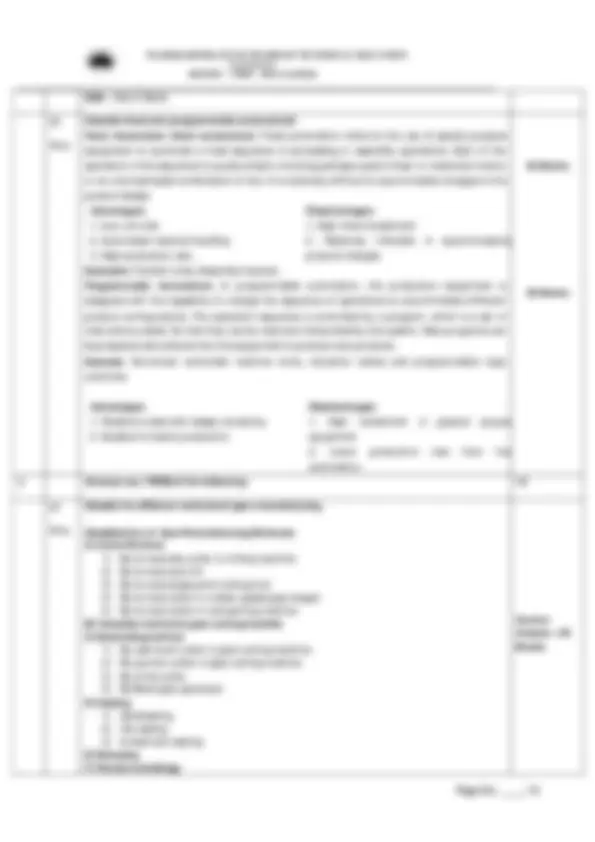
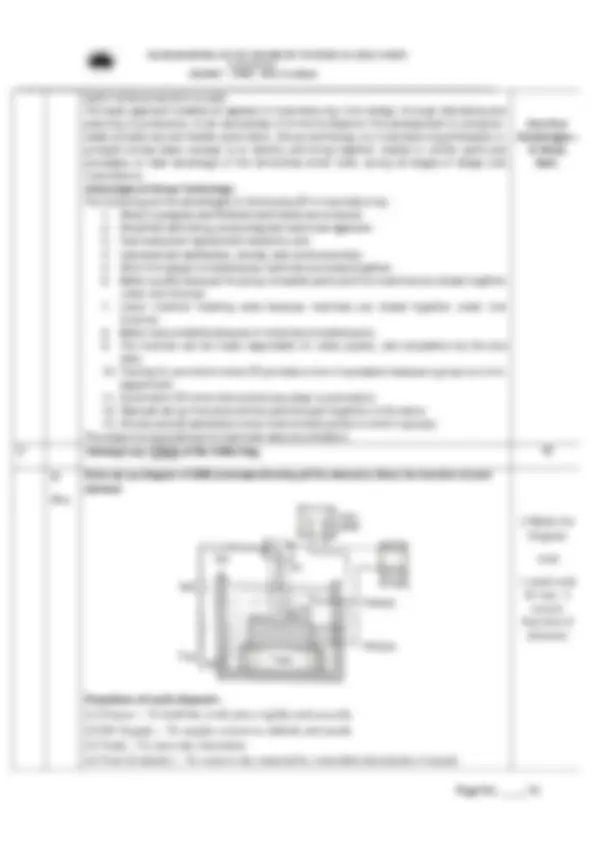
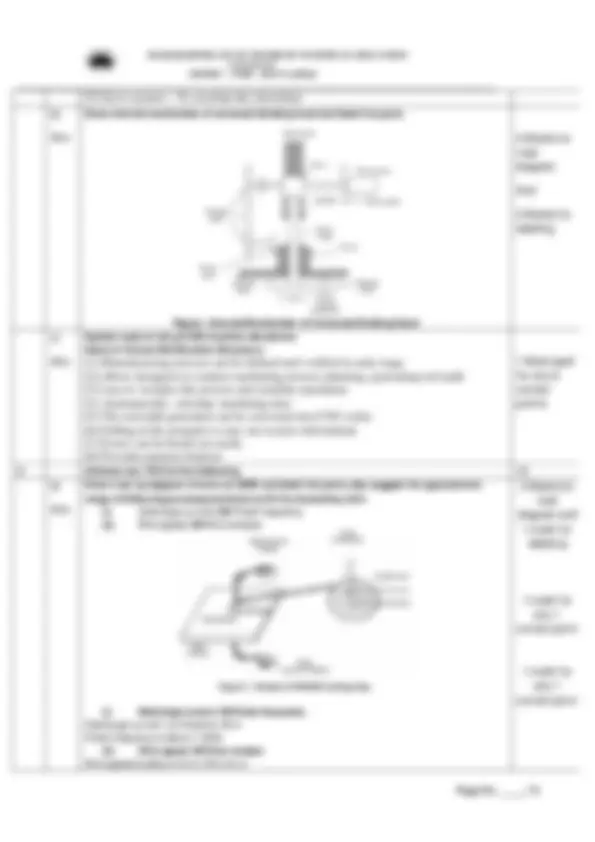
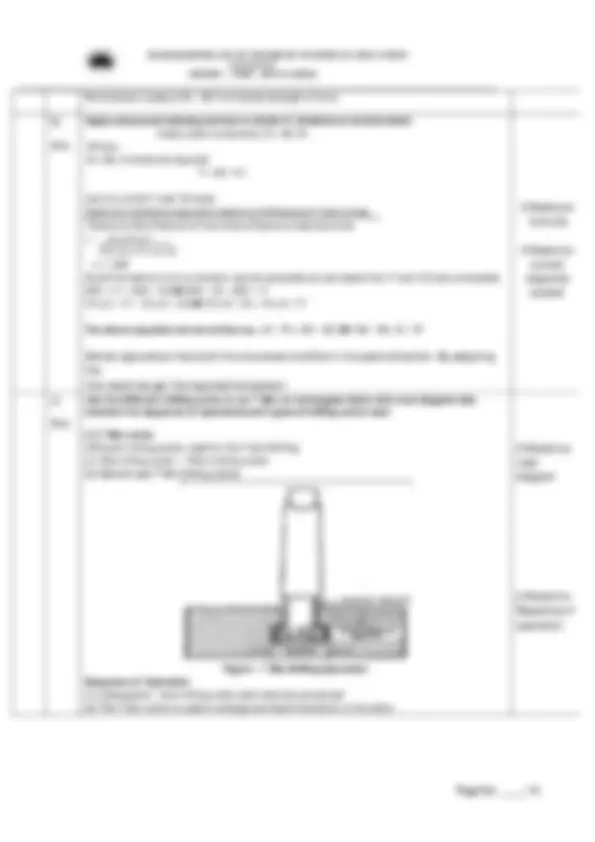
Study with the several resources on Docsity
Earn points by helping other students or get them with a premium plan
Prepare for your exams
Study with the several resources on Docsity
Earn points to download
Earn points by helping other students or get them with a premium plan
Community
Ask the community for help and clear up your study doubts
Discover the best universities in your country according to Docsity users
Free resources
Download our free guides on studying techniques, anxiety management strategies, and thesis advice from Docsity tutors
amp.....................................................
Typology: Lecture notes
1 / 20
This page cannot be seen from the preview
Don't miss anything!
Page 1 of 10
ZEAL POLYTECHNIC, PUNE.
THIRD YEAR (TY) DIPLOMA IN MECHANICAL ENGINEERING SCHEME: I SEMESTER: V NAME OF SUBJECT: ADVANCED MANUFACTURING PROCESS Subject Code: 22563 MSBTE QUESTION PAPERS & MODEL ANSWERS
**1. MSBTE SAMPLE QUESTION PAPER
1
Program Name : Diploma in Mechanical Engineering Program Code : ME Semester : Fifth Course Title : Advanced Manufacturing Processes Marks : 70 Time: 3Hrs. Instructions: (1) All questions are compulsory. (2) Illustrate your answers with neat sketches wherever necessary. (3) Figures to the right indicate full marks. (4) Assume suitable data if necessary. (5) Preferably, write the answers in sequential order. Q.1) Attempt any FIVE of the following. 10 Marks a) Enlist the different type non conventional machining processes. b) Name the various types milling machines. c) List various gear finishing methods. d) State advantages and limitations of CNC machine. e) Define the ‘Work Zero position’ and ‘Machine Zero position’ of CNC machine. f) Write meaning of following M-codes. i) M03 and ii) M g) Give one example of fixed automation and one example of flexible automation. Q.2) Attempt any THREE of the following. 12 Marks a) Explain the functions of the dielectric fluid used in EDM. b) Compare between up milling and down milling process. c) Describe the concept of ‘Tool Offset’ for CNC machine with suitable example. d) Justify need of cutter radius compensation given for CNC milling programming. Q.3) Attempt any THREE of the following. 12 Marks a) Distinguish between gear shaping by pinion cutter and gear shaping by rack cutter. b) Compare lead screw of conventional machine and re-circulating ball screw of CNC machine. c) Differentiate between canned cycle and subroutine function for CNC machine. d) Draw the diagram of simple robot and show different components of it.
3
Program Name : Diploma in Mechanical Engineering Program Code : ME Semester : Fifth Course Title : Advanced Manufacturing Processes Marks : 20 Time: 1 Hour Instructions: (1) All questions are compulsory. (2) Illustrate your answers with neat sketches wherever necessary. (3) Figures to the right indicate full marks. (4) Assume suitable data if necessary. (5) Preferably, write the answers in sequential order. Q.1 Attempt any FOUR. 08 Marks a) State any four characteristics of dielectric fluid used in EDM process. b) Write any two functions of electrolyte used in Electro Chemical Machining (ECM) c) List various type of cutters used in milling machining process. d) Name the various methods of indexing. e) Enlist the different type of gears. f) State the principle of gear honing process. Q.2 Attempt any THREE. 12 Marks a) Differentiate between abrasive jet machining (AJM) and Ultrasonic machining (USM) b) Draw diagram of Wire Cut Electric Discharge Machining (WEDM) and show all elements on it. c) Explain the straddle milling operation with neat sketch. d) Apply compound indexing method to index 51divisions on blank. e) Describe gear shaping by pinion method with suitable diagram. f) Justify, selection of gear material depends on amount of power transmitted.
4
Program Name : Diploma in Mechanical Engineering Program Code : ME Semester : Fifth Course Title : Advanced Manufacturing Processes Marks : 20 Time: 1 Hour Instructions: (1) All questions are compulsory. (2) Illustrate your answers with neat sketches wherever necessary. (3) Figures to the right indicate full marks. (4) Assume suitable data if necessary. (5) Preferably, write the answers in sequential order. Q.1 Attempt any FOUR. 08 Marks a) Write any two feedback devices used in closed loop control CNC machine. b) State the thumb rule for axis identification for CNC machine. c) Write the meaning G00 and G01 code used in CNC programming. d) List various compensations required during CNC programming. e) Name the various types of automations in industry. f) Define- Automation Q.2 Attempt any THREE. 12 Marks a) Explain, closed loop control system CNC machine with neat sketch. b) Apply right hand rule to identify axes of wire cut EDM CNC machine. c) Prepare process sheet and calculate cutting parameter for the following component with neat diagram. Use HSS end milling cutter of Ø20mm. Raw material – Aluminium Raw material size= 6 0 X 60 Feed rate=0.2 mm/rev. Cutting speed= 90 m/min.
22563
MAHARASHTRA STATE BOARD OF TECHNICAL EDUCATION (Autonomous) (ISO/IEC - 27001 - 2013 Certified) __________________________________________________________________________________________________
MAHARASHTRA STATE BOARD OF TECHNICAL EDUCATION (Autonomous) (ISO/IEC - 27001 - 2013 Certified) __________________________________________________________________________________________________
12 Higher load on cutter(Hob) Lower load on Cutter (Honing Tool) 13 Higher feed rate. Lower feed rate. 14
Compare “Point to Point” and continuous path CNC machine S. N. Point to Point Continuous Path 1 The primary function of point to point path control system, is to move a cutting tool form one point location to another predefined point on the worktable Contouring system generates a continuously controlled tool path by the capability of computing the points of the path 2 It is the cheapest tool control system It is the most expensive. 3 It is generally used for hole operations such as drilling, boring, reaming, tapping and punching. Contouring system had the ability to perform linear and circular or parabolic interpolation. 4 It is the lowest level of motion control between the tool and workpiece. It is the highest level of control between the tool and workpiece. 5 Point-to-point (PTP) is also sometimes called a positioning system. Continuous Path is also called Contouring path system. 6 It is simple and easy. Contouring is the most complex 7 Only two axis movement can complete PTP operation. Simultaneous movement of more than one axis movement can take place to complete the operation. 8 It is not capable to perform Contouring operations. It is capable of performing both PTP and straight-cut operations. 9 No cutting is performed between holes, there is no need for controlling the relative motion of the tool and workpiece between hole locations Contouring system generates a continuously controlled tool path by the capability of computing the points of the path (interpolating). 10 Any Four = 01 Mark Each.
Explain the meaning of following block format of CNC. N020 G03 X12 Y14 Z-0.5 I0 J12 EOB N0020 – Block Number. G03 – Circular interpolation (Counter- Clockwise). X12 – X coordinate of the arc end point = 12. Y14 – Y coordinate of the arc end point = 14. Z-0.5 – Depth of Cut in Z - Direction= 0.5. I0 – Distance along X – axis from the arc start point to the arc center point = 0. J12 – Distance along Y – axis from the arc start point to the arc center point = 12. Correct Ans. = ½ Mark Each
MAHARASHTRA STATE BOARD OF TECHNICAL EDUCATION (Autonomous) (ISO/IEC - 27001 - 2013 Certified) __________________________________________________________________________________________________
G) Plastic molding H) Extruding
Apply right hand rule for axes identification of CNC vertical milling with neat diagram Right Hand Rule for Axes Identification of CNC Vertical Milling : The main axis of movement and the direction of movement along this axis is identified as follows: Z- Axis: The Z- axis motion is always the axis of the main spindle of the machine. It does not matter whether the spindle carries the work piece or the cutting tool. On vertical machines the Z-axis is vertical. Positive Z movement is in the direction is towards the tip of middle finger. X-Axis: The X-axis is always horizontal and parallel to the work holding surface. If the Z-axis is vertical in vertical milling machine, positive X-axis movement is identified as being to the tip of thumb. Y-Axis: The Y-axis is always at right angle to both the X-axis and Z-axis. Positive Y-axis movement is identified as being to the tip of Fore finger. A- Axis: Direction of curled finger about X – axis is rotary motion along X-axis is consider as positive. B- Axis: Direction of curled finger about Y – axis is rotary motion along Y-axis is consider as positive. C- Axis: Direction of curled finger about Z– axis is rotary motion along Z-axis is consider as positive. Sketch 01 Mark & Explanation = 03 Marks
Calculate the cutting parameters and prepare process sheet for the component shown in Fig. No. 1 with neat diagram. All the dimensions are in mm. Given: Raw material - Aluminium, Stock Size – Dia.14 X 42 length, Feed ( f ) = 0.2 mm/rev., Cutting Speed (V) = 90 m/min., Consider work zero (W) as per Fig. No. 1. Figure No. 1 Given Data: V = 90 m/min., f = 0.2 mm/rev., D = 14 mm, Depth of cut, dc = 1 mm, Length of Cut, l = 25 mm Cutting Parameters: Spindle Speed: V = πDN/ N = 2043 rpm. Feed: f = 0.2 mm/rev. Depth of Cut: dc = 1 mm 01 Mark for Calculation and 03 Marks for Process Sheet
MAHARASHTRA STATE BOARD OF TECHNICAL EDUCATION (Autonomous) (ISO/IEC - 27001 - 2013 Certified) __________________________________________________________________________________________________
Operation No. Description Machine Tool Tools / Fixture Spindle Speed in rpm. Feed in mm/rev . Depth of Cut in mm
Develop full G and M code manual part program of CNC lathe for the component shown in Fig. No. 1 using word address format (WAF). Figure No. 1 Point X Z P0 0.0 2. P1 0.0 0. P2 12.0 0. P3 12.0 - 25. P4 14.0 - 25. P5 14.0 - 41. P6 20.0 - 41. O1234; N001 G28 U0.0 W0.0; N002 G90 G21 G95; N003 M03 S2043 M08; N004 G00 X0.0 Z2.0; N005 G01 X0.0 Z0.0 F0.2; N006 G01 X12.0 Z0.0; N007 G01 X12.0 Z - 25.0; N008 G01 X14.0 Z - 25.0; N009 G01 X14.0 Z - 41.0; N010 G01 X20.0 Z - 41.0; N011 G28 U0.0 W0.0; N012 M05; N013 M09; N014 M30; Correct Answer = 04 Marks
Justify the need of Group Technology in today’s manufacturing situation Group technology is an approach to organizing manufacture which can be applied in any industry (machining, welding, foundry, press work, forging, plastic molding, etc.) where small-
MAHARASHTRA STATE BOARD OF TECHNICAL EDUCATION (Autonomous) (ISO/IEC - 27001 - 2013 Certified) __________________________________________________________________________________________________
Draw internal mechanism of universal dividing head and label the parts Figure:- Internal Mechanism of Universal Dividing Head
Explain need of virtual CNC machine simulators Need of Virtual CNC Machine Simulator:-
Draw a set up diagram of wire cut EDM and label the parts, also suggest the approximate range of following process parameters with its measuring units (i) Discharge current OR Pulse frequency (ii) Wire speed OR Wire tensio n (i) Discharge current OR Pulse frequency Discharge current is limited to 30 A Pulse frequency is about 1 MHz (ii) Wire speed OR Wire tension Wire speed is about 2.5 to 150 mm/s
MAHARASHTRA STATE BOARD OF TECHNICAL EDUCATION (Autonomous) (ISO/IEC - 27001 - 2013 Certified) __________________________________________________________________________________________________
Wire tension is about 50 – 60 % of tensile strength of wire
Apply compound indexing method to divide 51 divisions on circular blank Index crank movement (T) = 40 /N Where , N = No of divisions required T = 40 / 51 Let’s try circle17 and 18 holes Factors of divisions required x factors of difference of hole circles Factors of 40 x Factors of first circle x Factors of second circle = 3 x 17 x 1 10 x 4 x 17 x 3 x 6 = 1 / 240 As all the factors from numerator can be cancelled we can select the 17 and 18 hole circle plate 240 / 17 – 240 / 18 OR 240 / 18 – 240 / 17 14 x 2 / 17 – 13 x 6 / 18 OR 1 3 x 6 / 18 – 14 x 2 / 17 The above equation can be written as = 2 / 17 + 12 / 18 OR - 12 / 18 – 2 / 17
Use the different milling cutter to cut T Slot on rectangular block with neat diagram also mention the sequence of operations and types of milling cutter used [1] T Slot cutter Different milling cutter used for the T slot Milling [1] End milling cutter / Plain milling cutter [2] Special type T Slot Milling Cutter Figure :- T Slot Milling Operation Sequence of Operation [1] ]Using plain / end milling cutter plain slots are produced [2] The T slot cutter is used to enlarge and face the bottom of the slots