
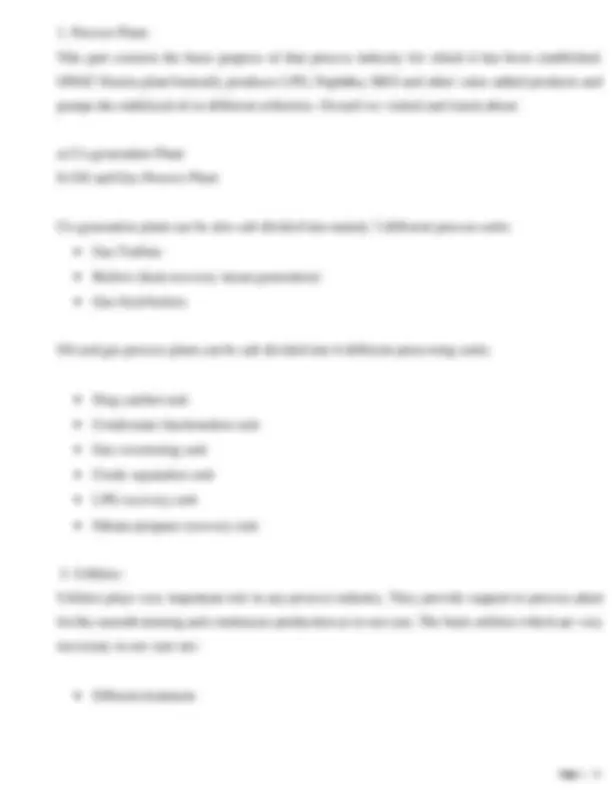
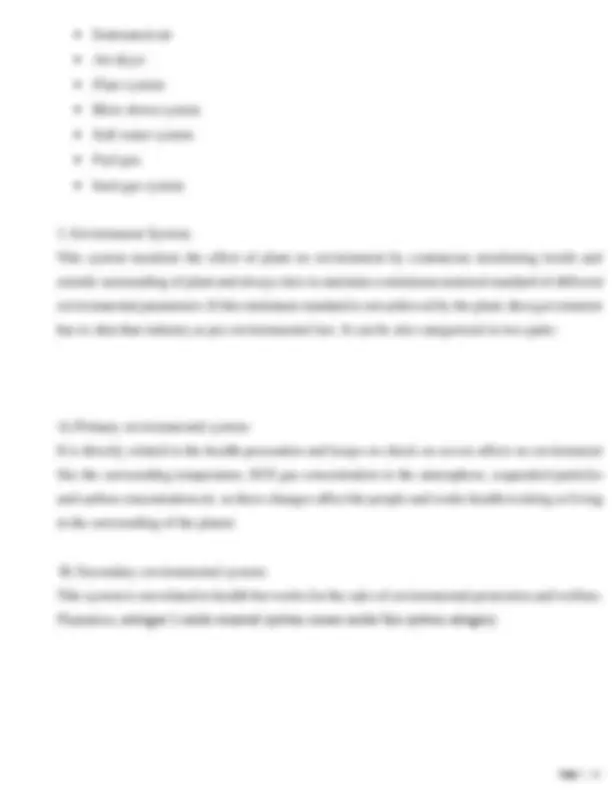
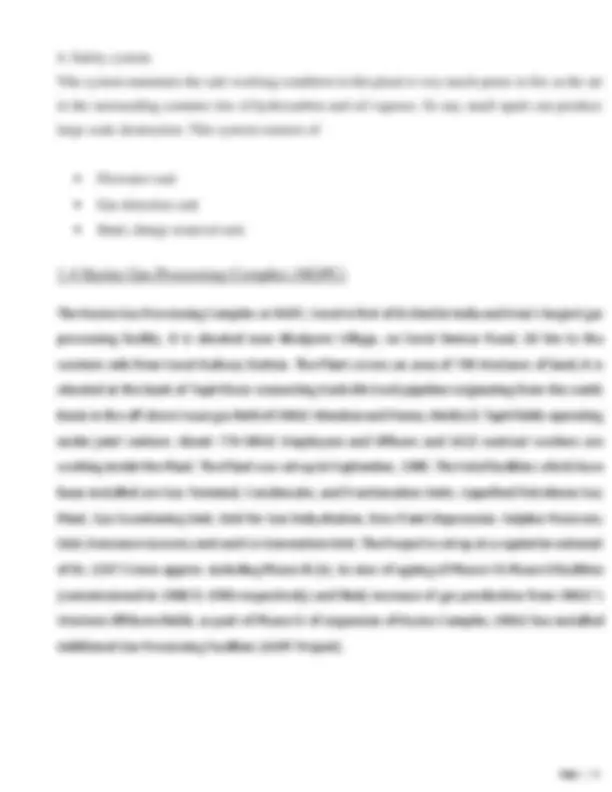
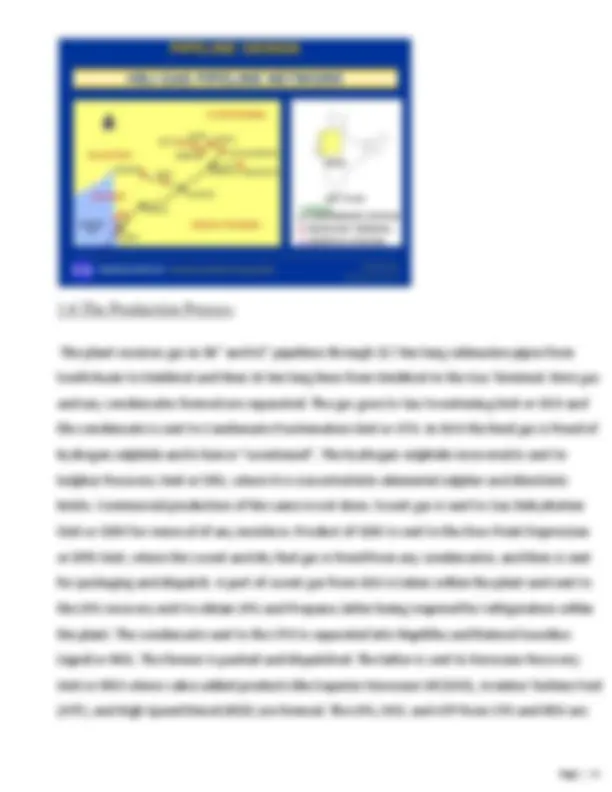
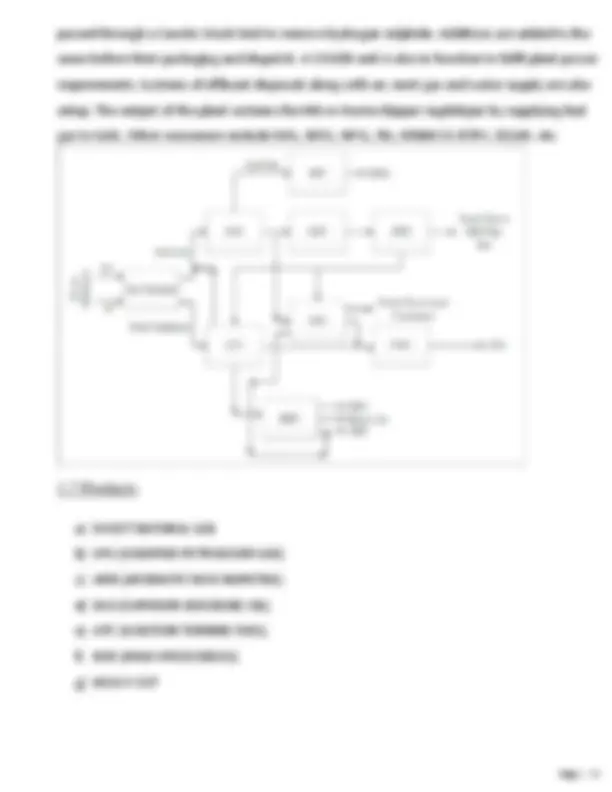
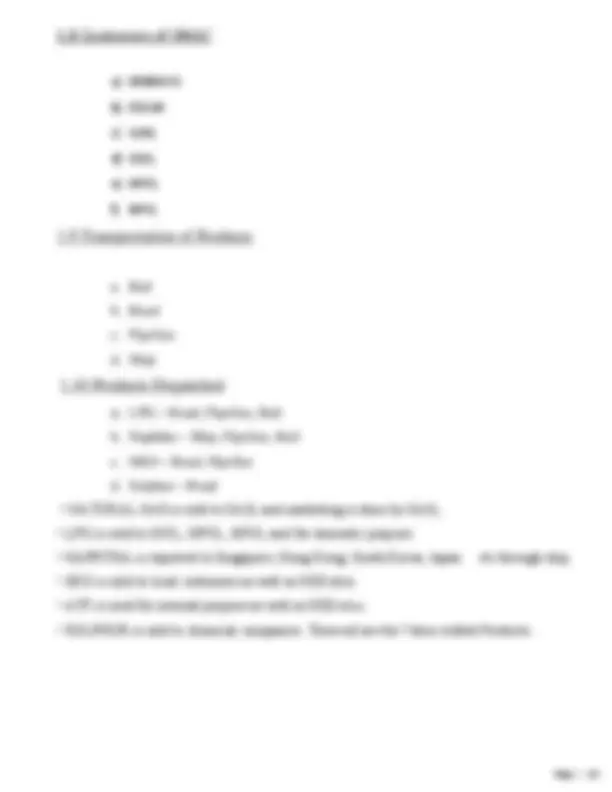
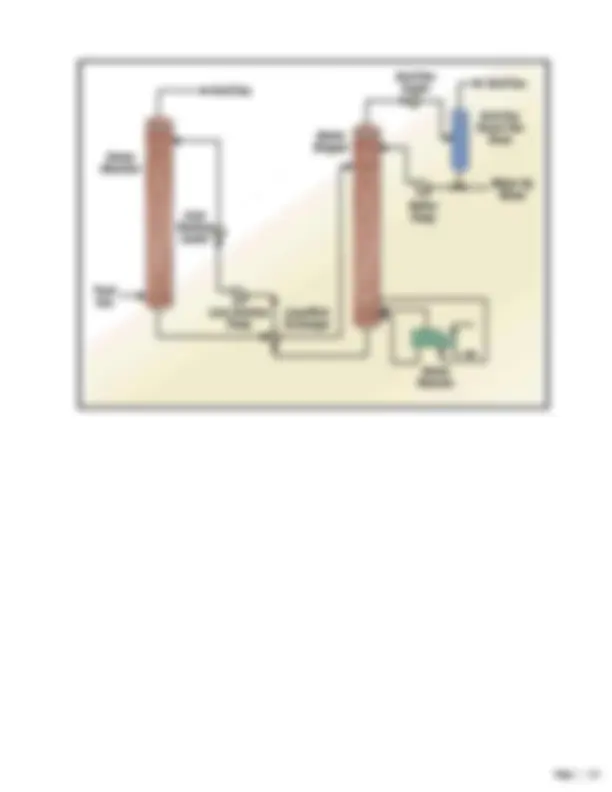
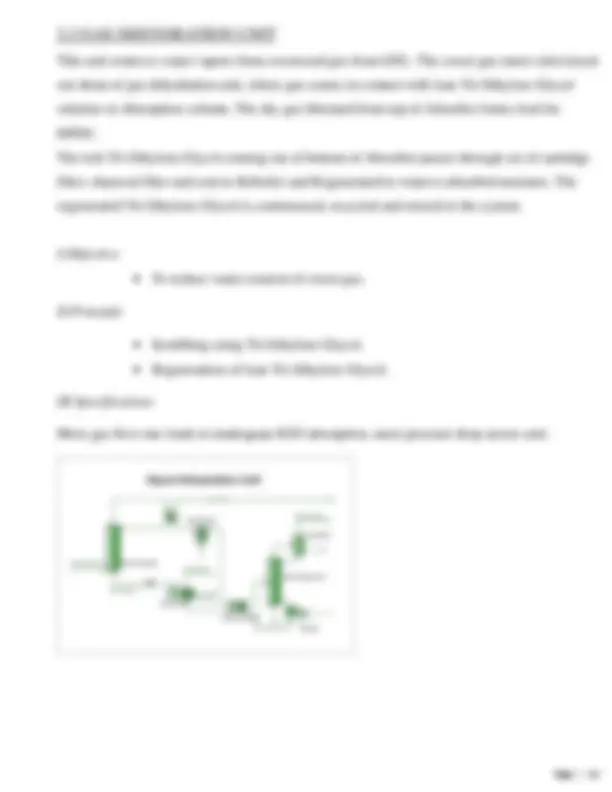
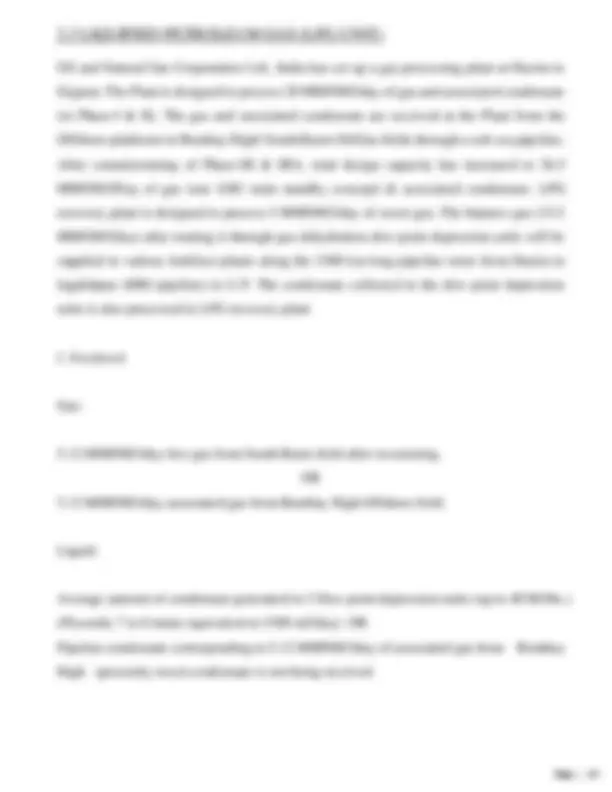
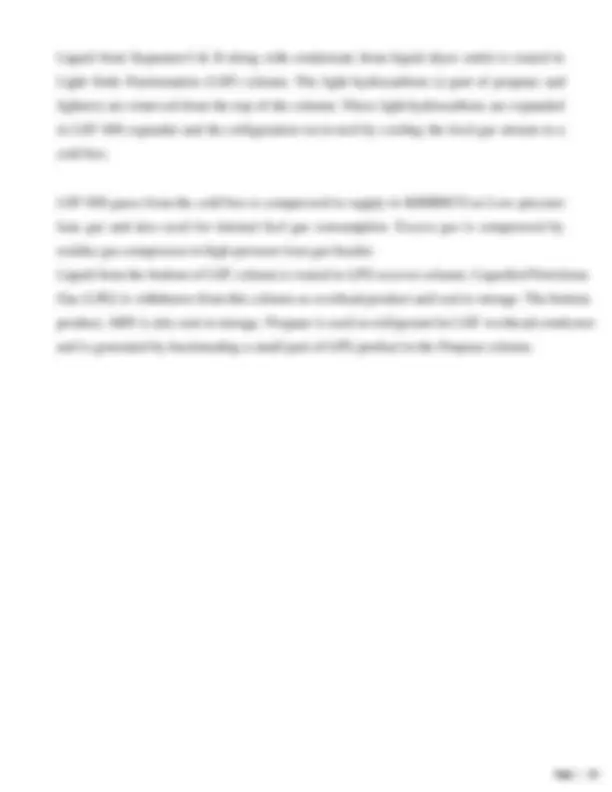
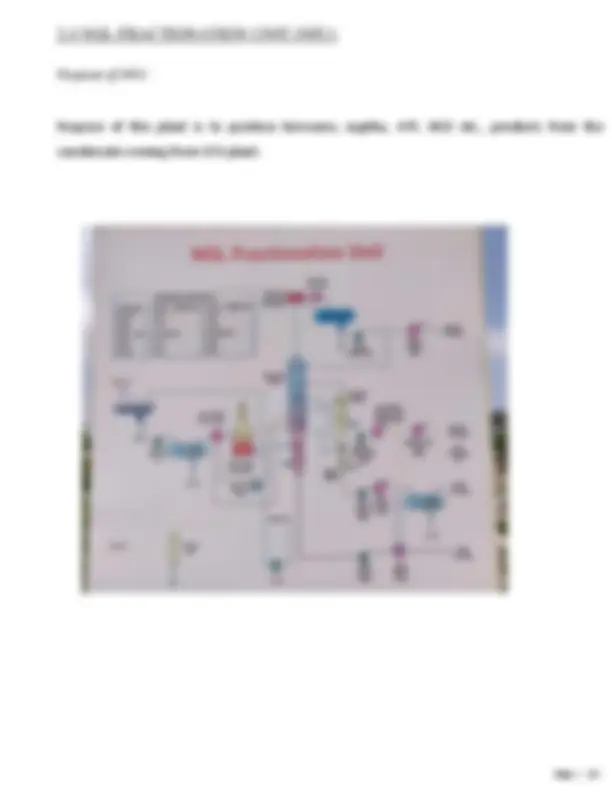
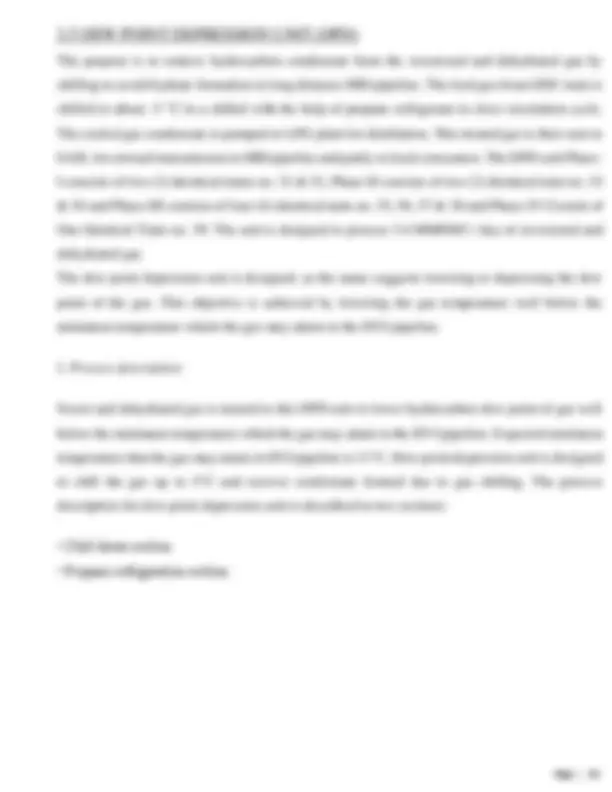
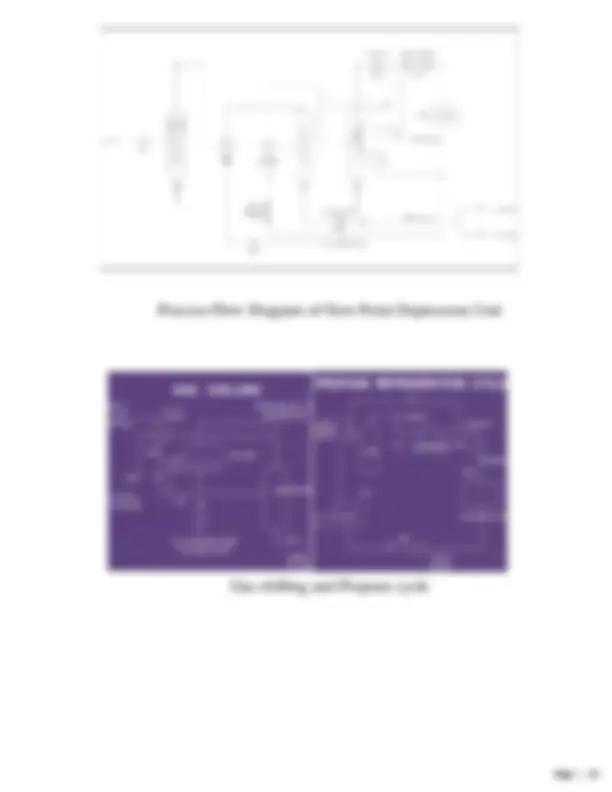
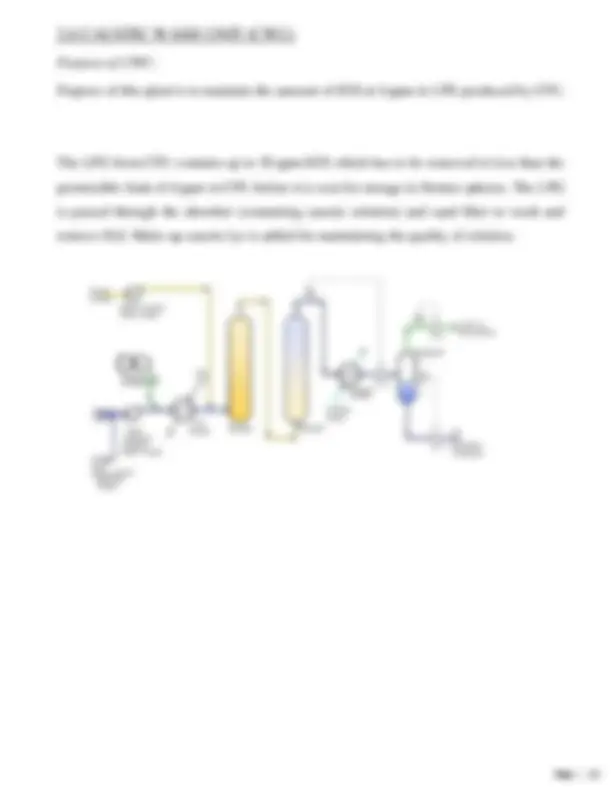
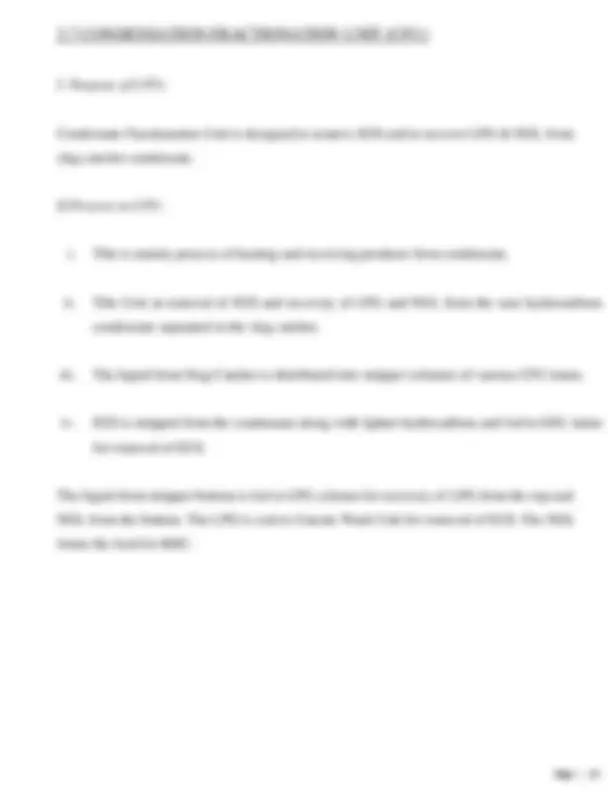
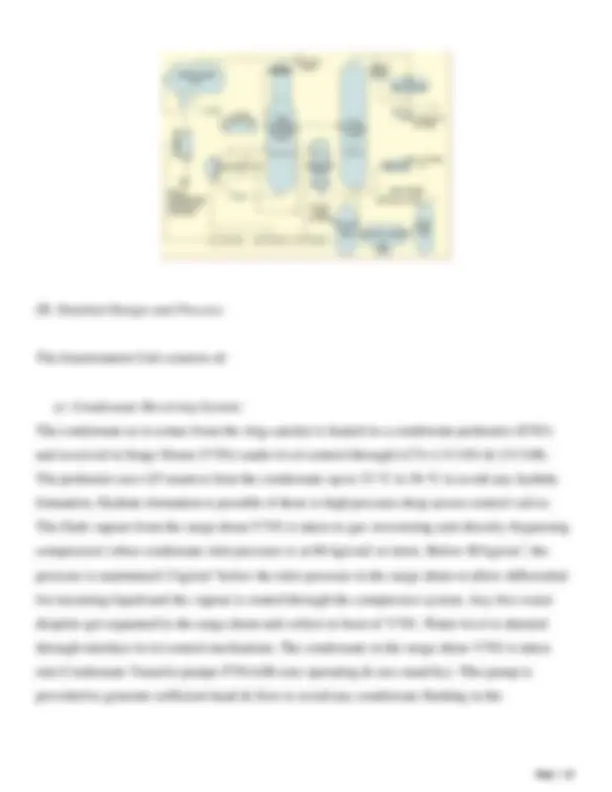
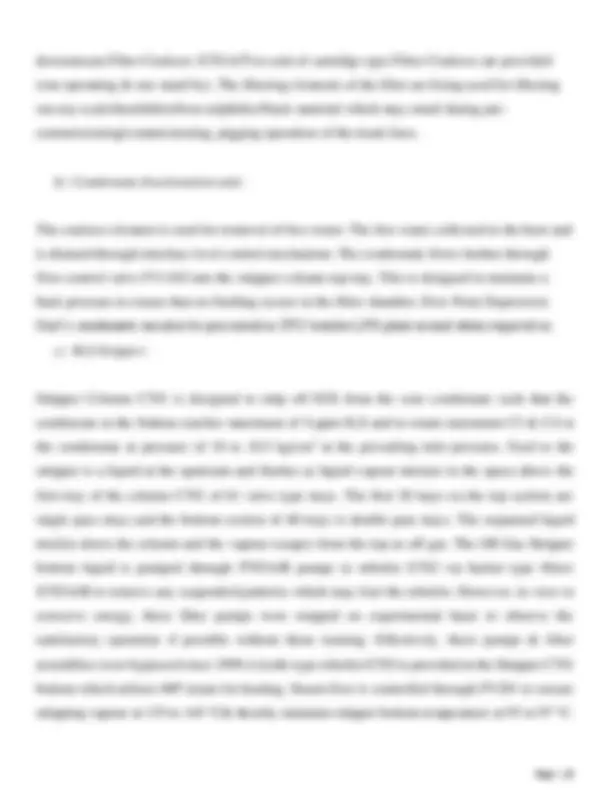
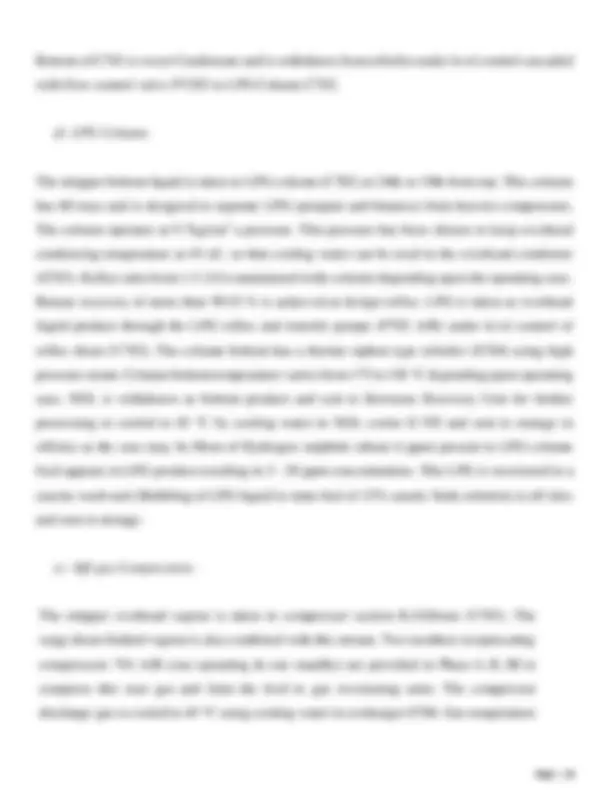
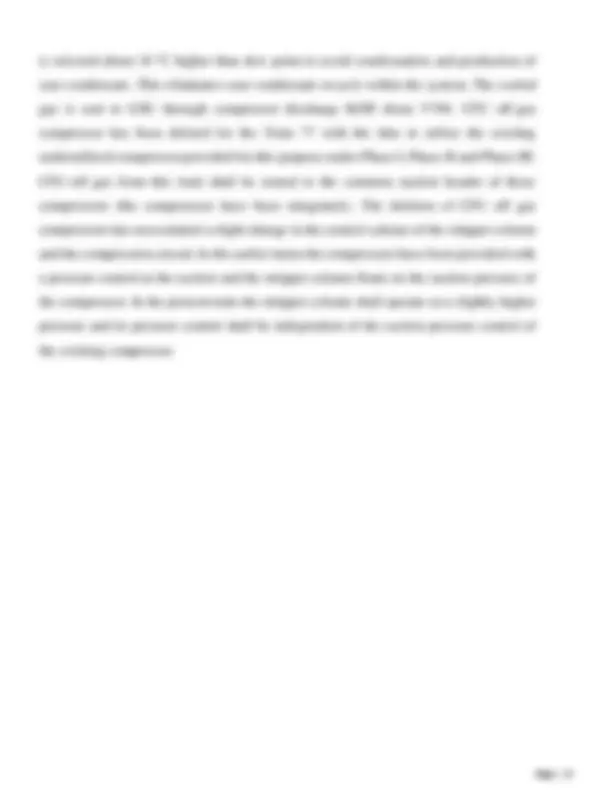
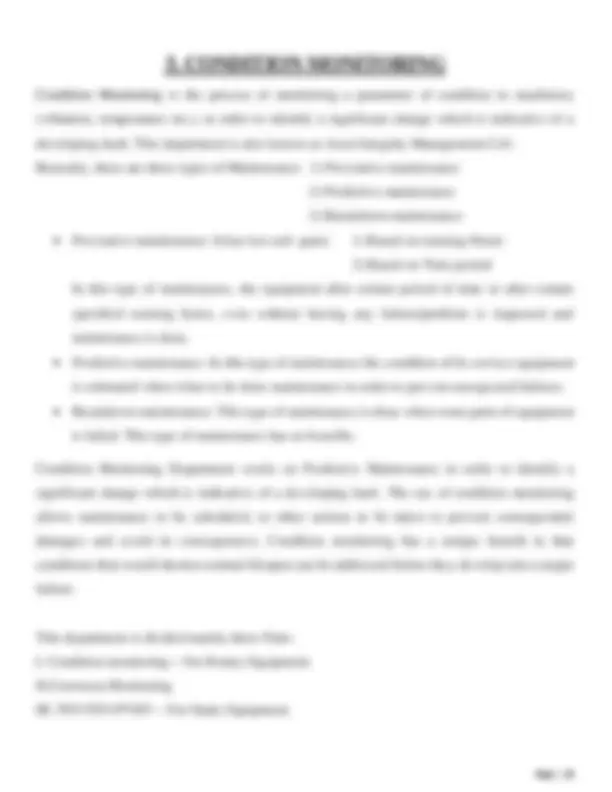
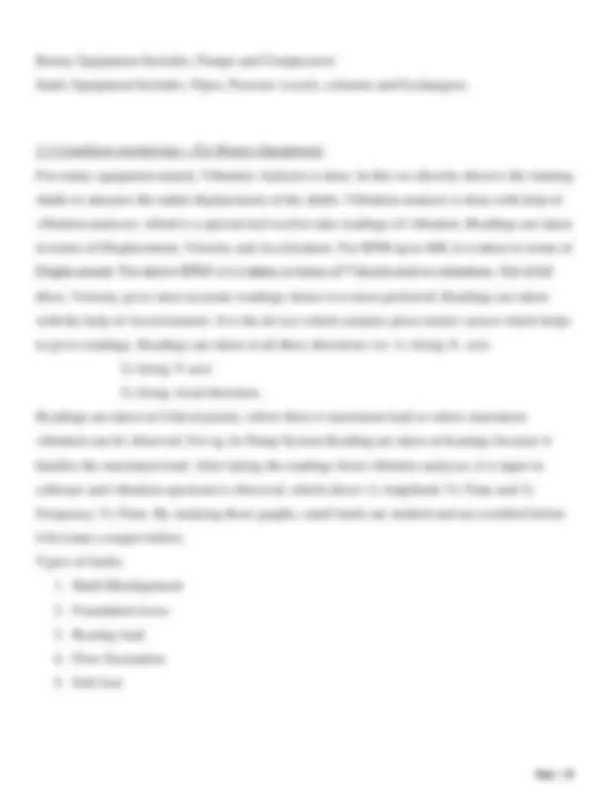
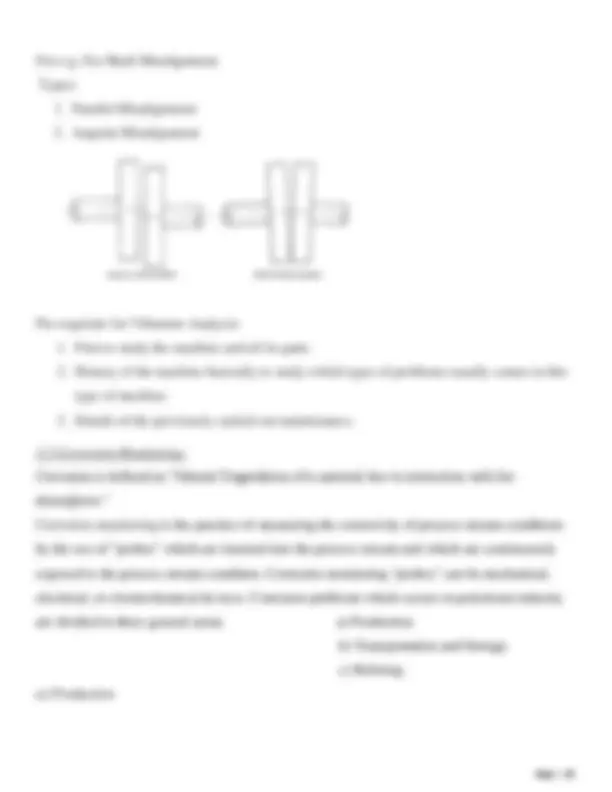
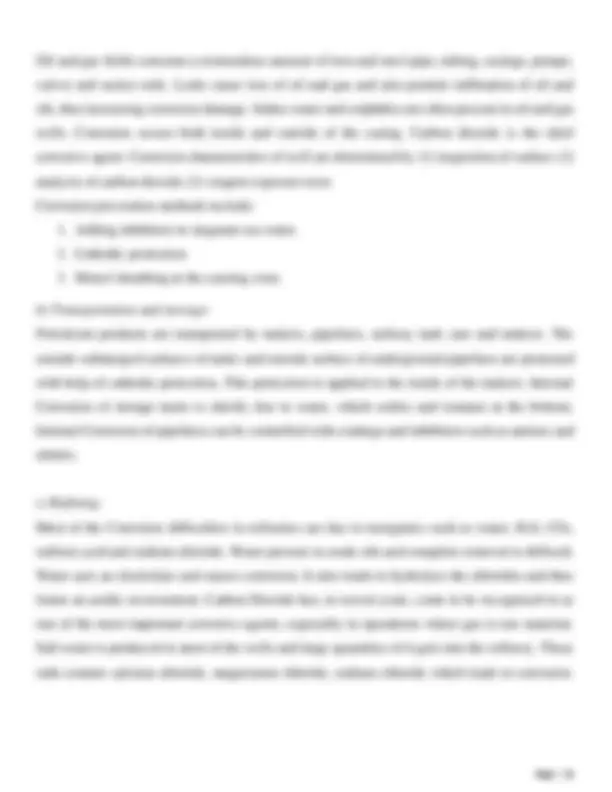
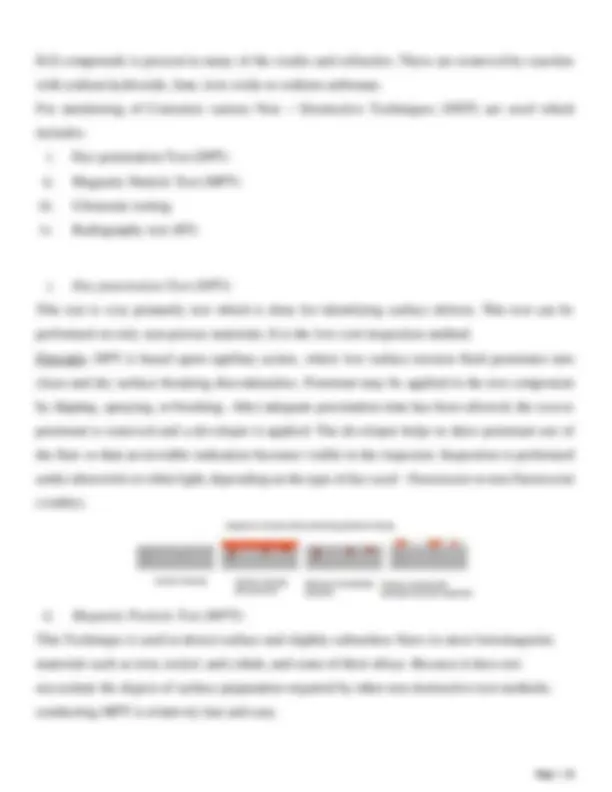
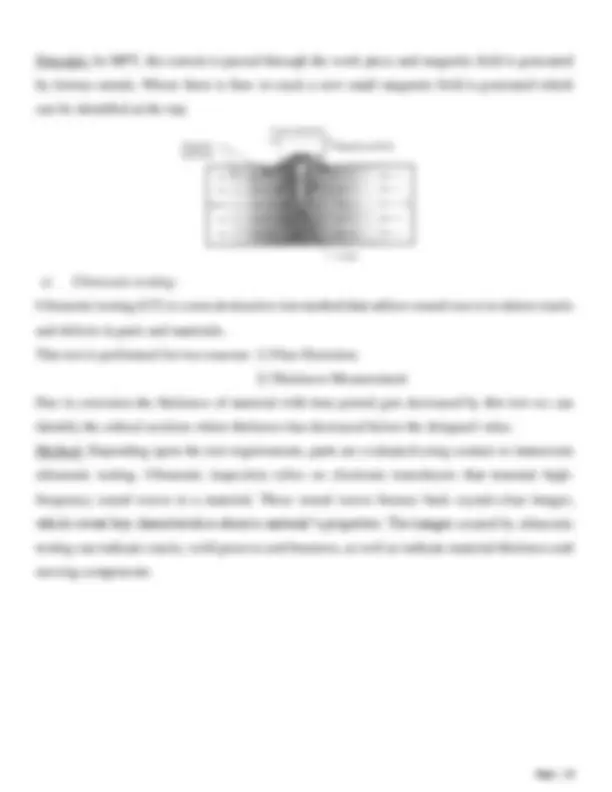
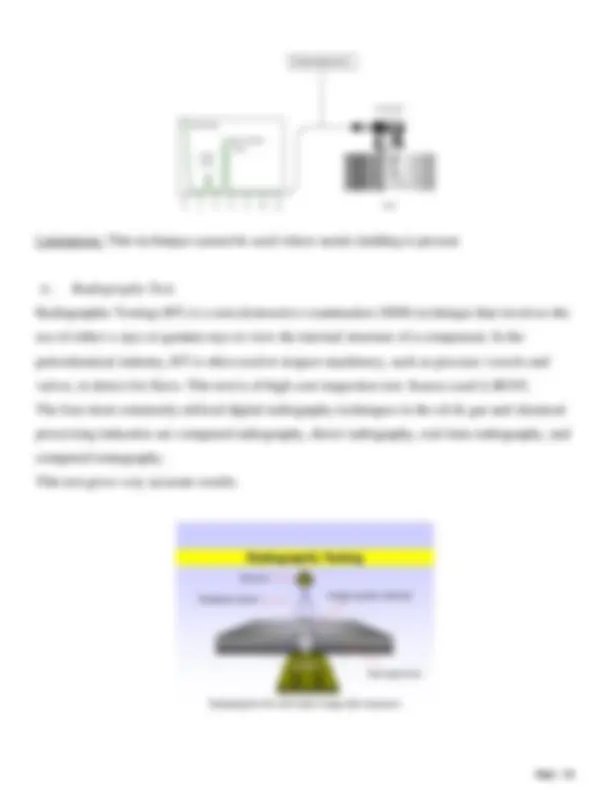
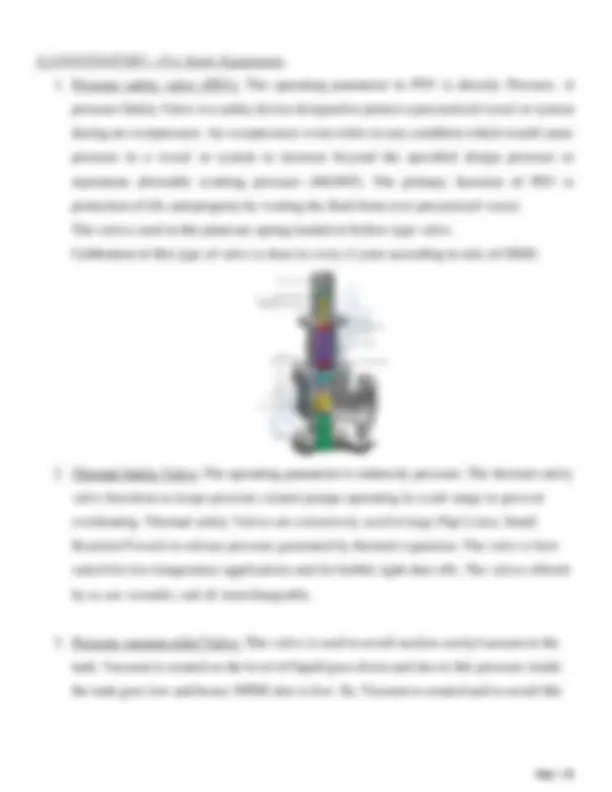
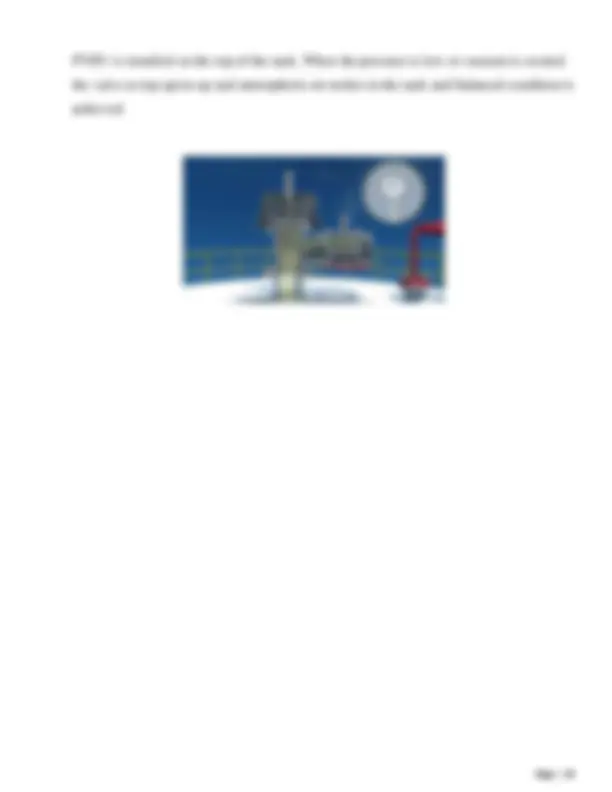
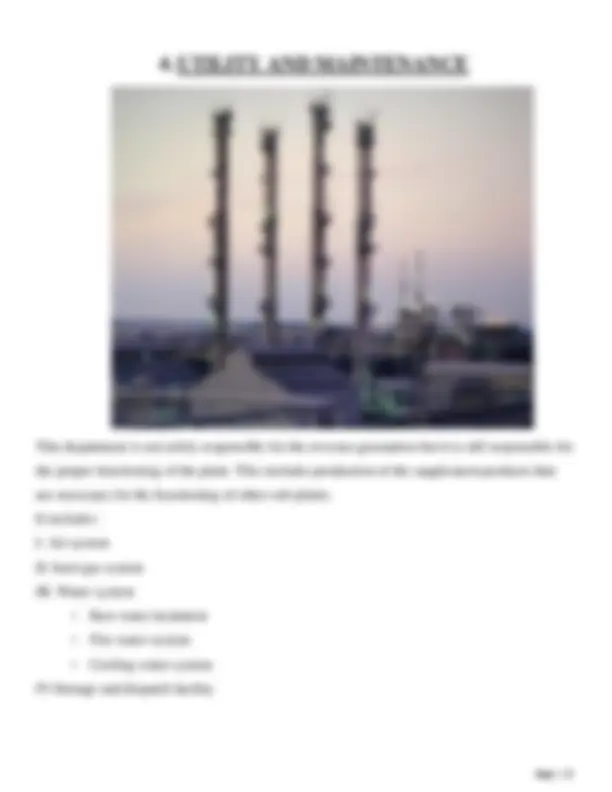
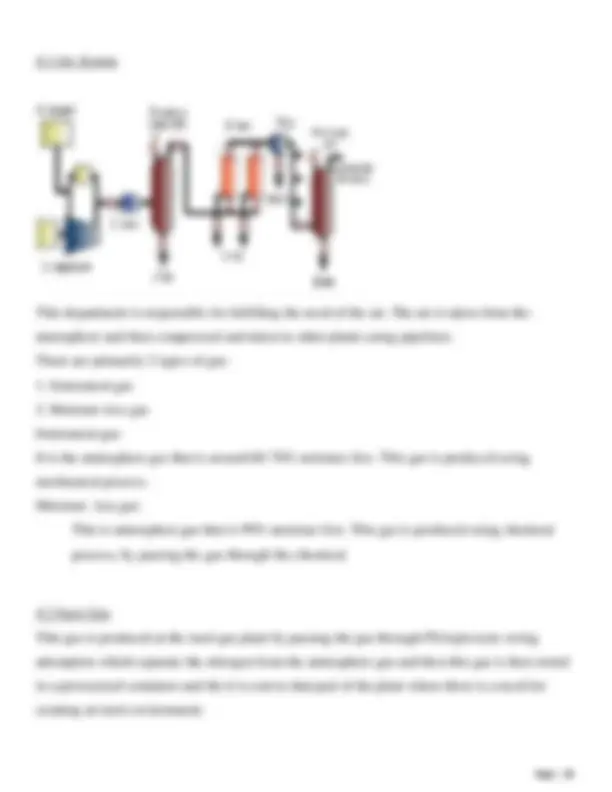
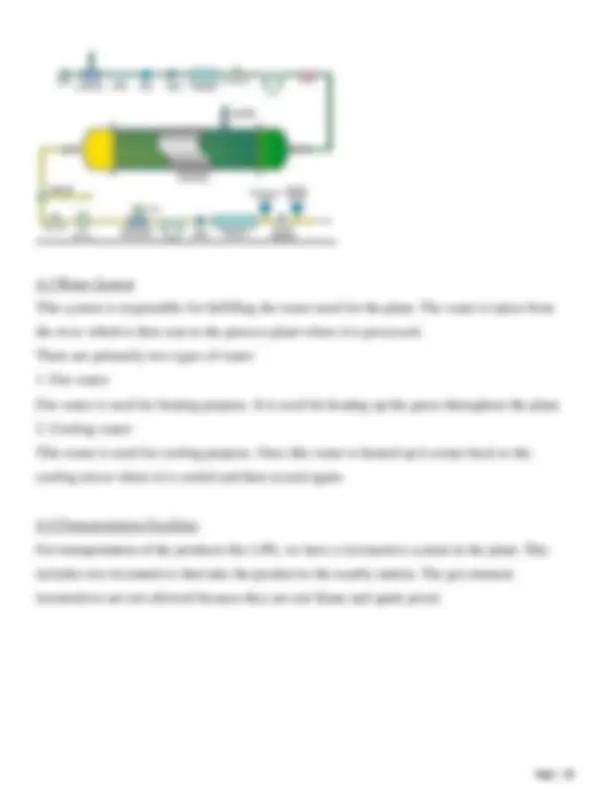

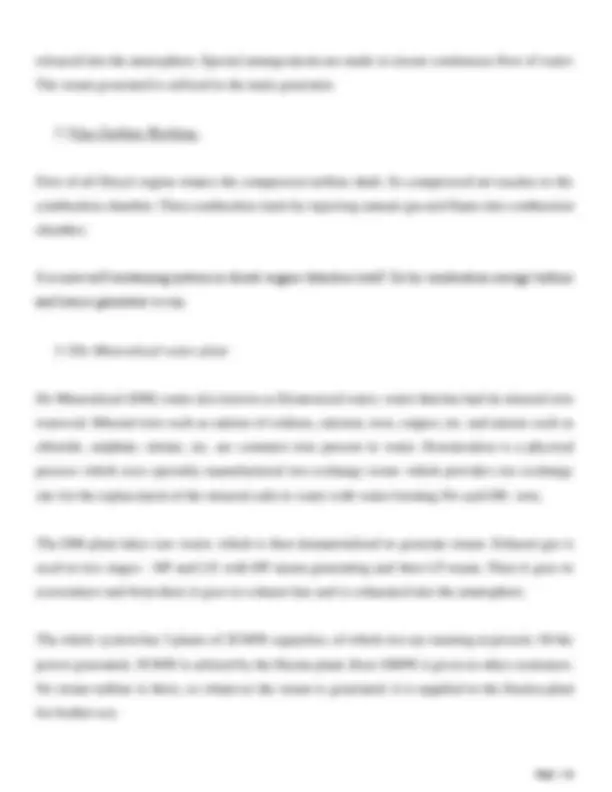
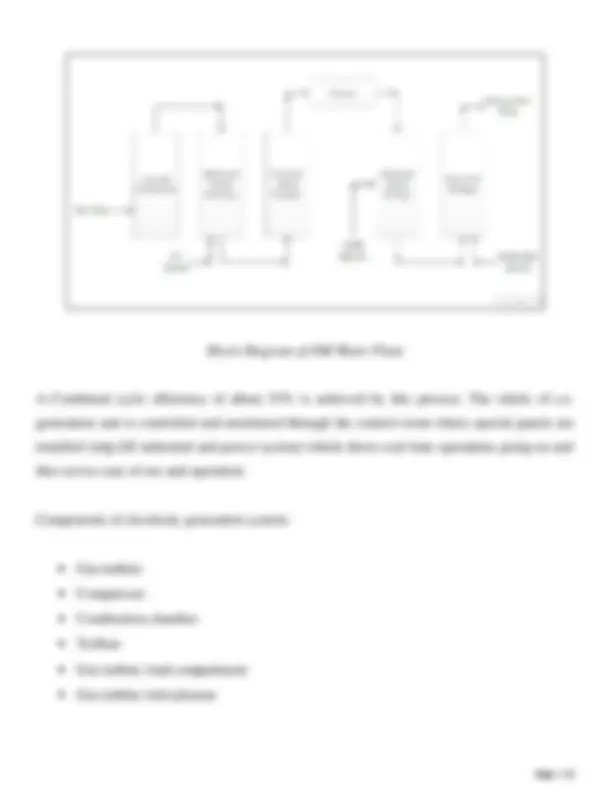
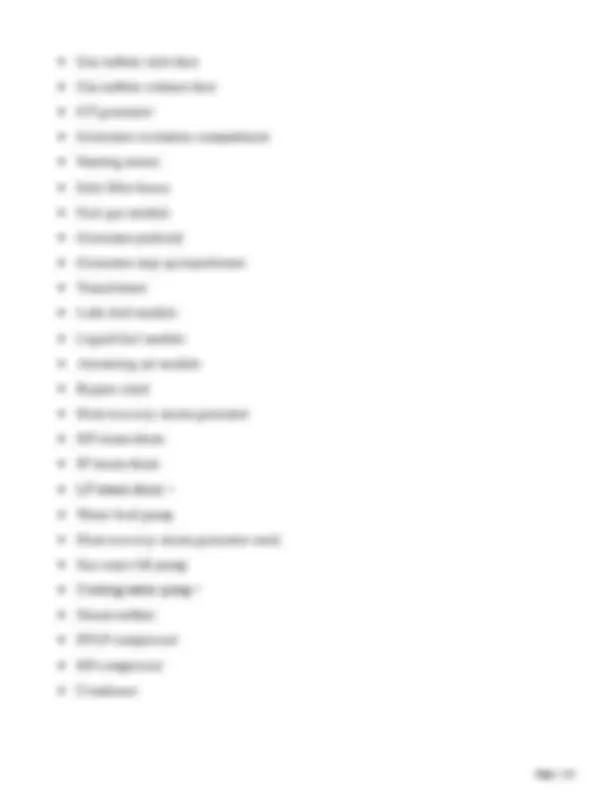
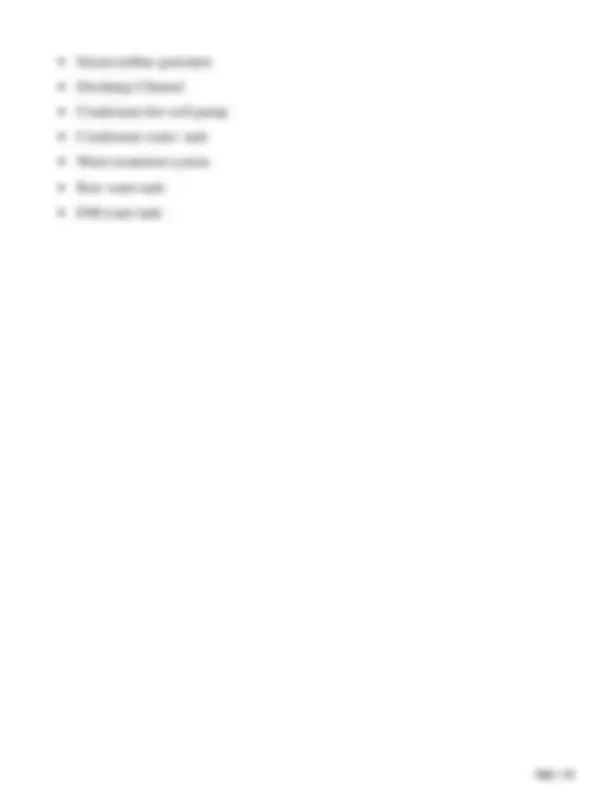
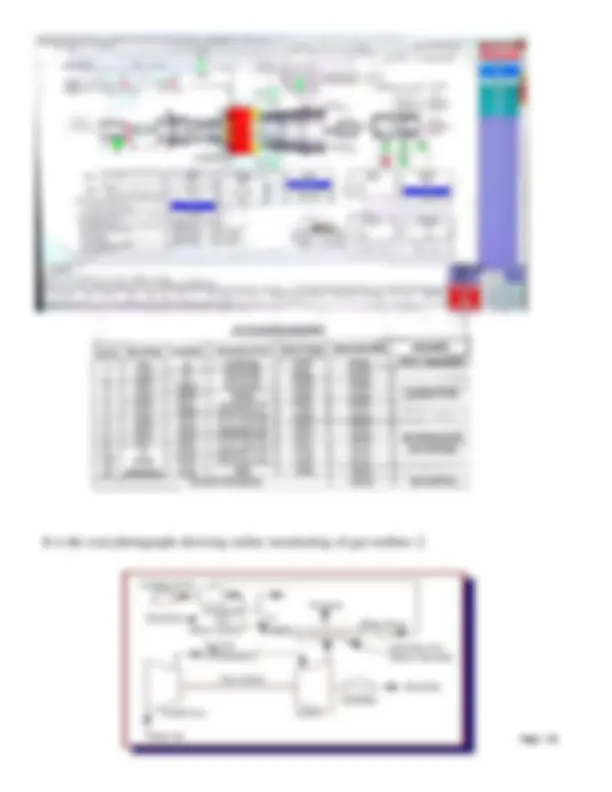
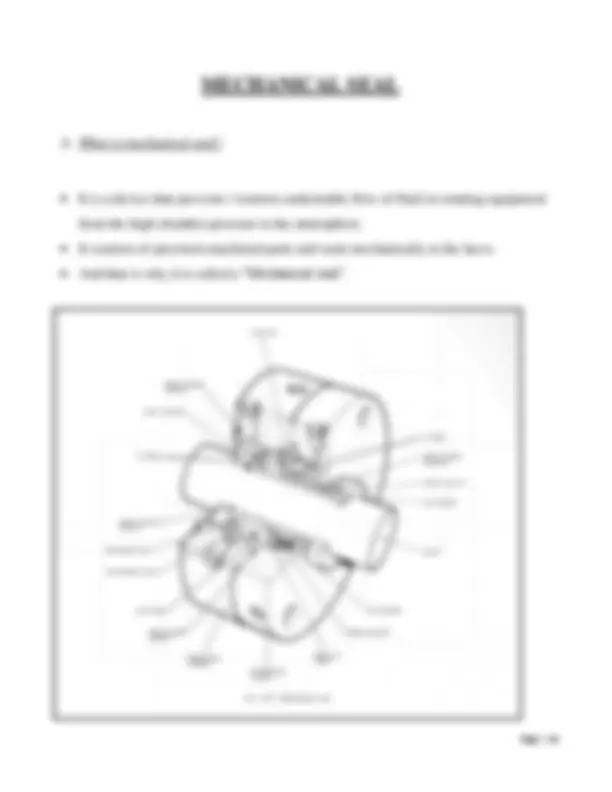
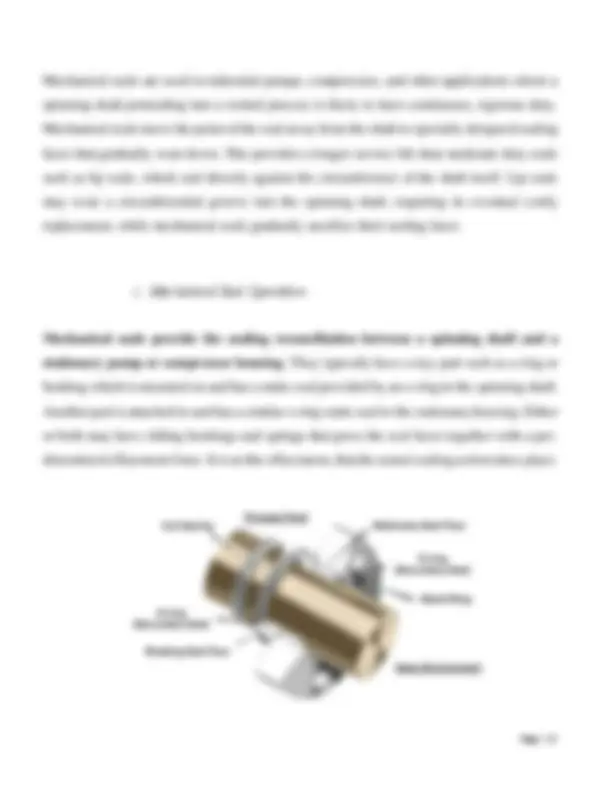
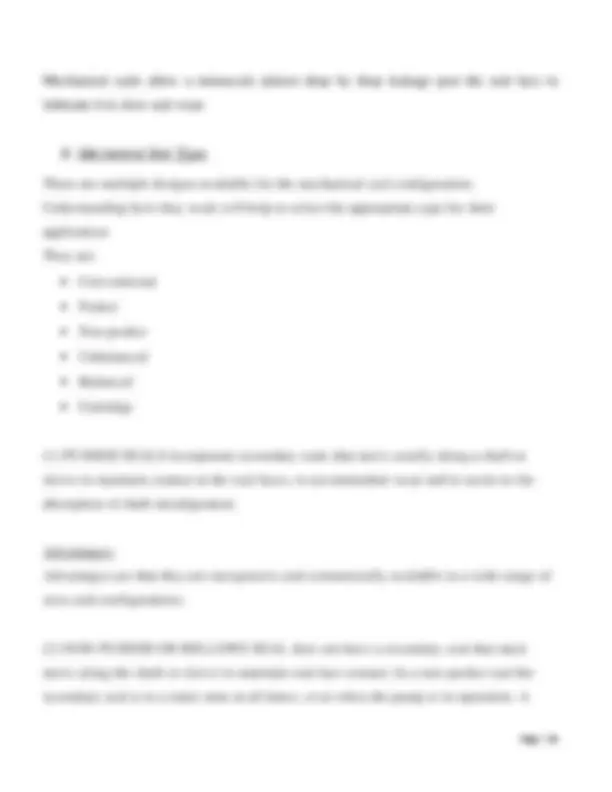
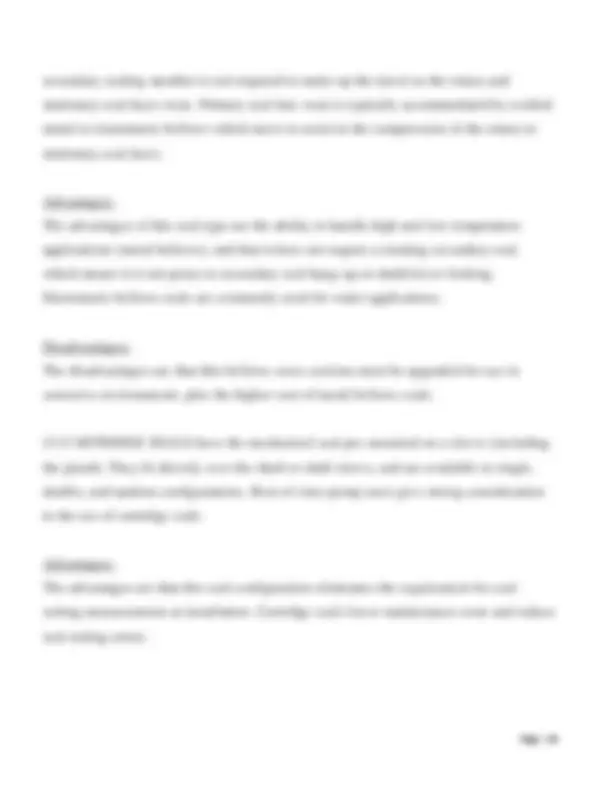
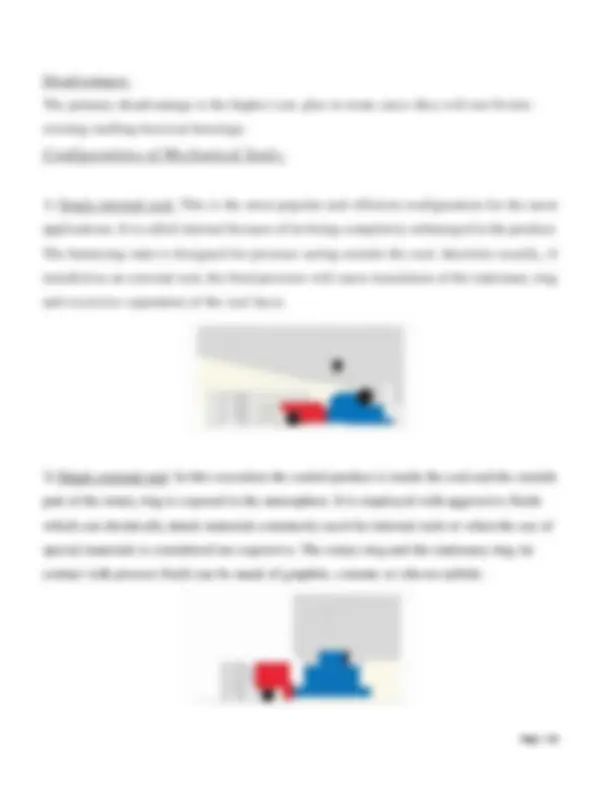
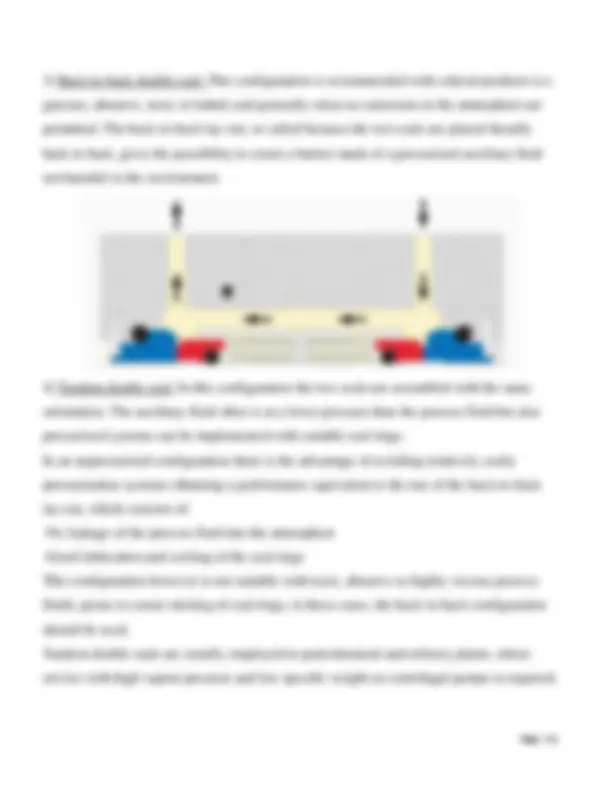
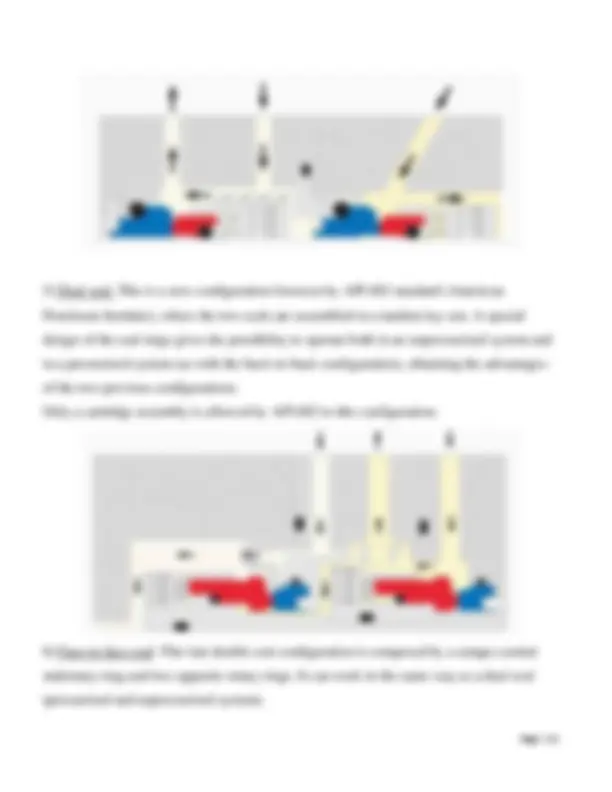
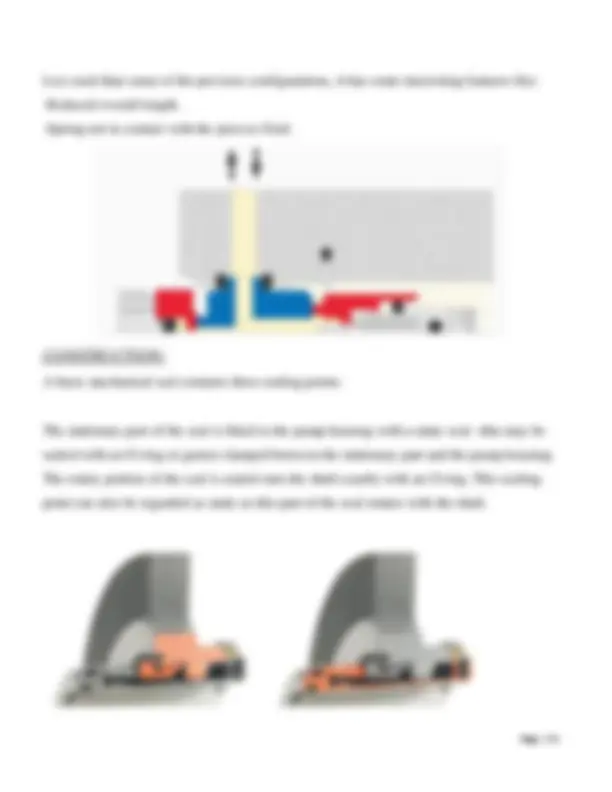
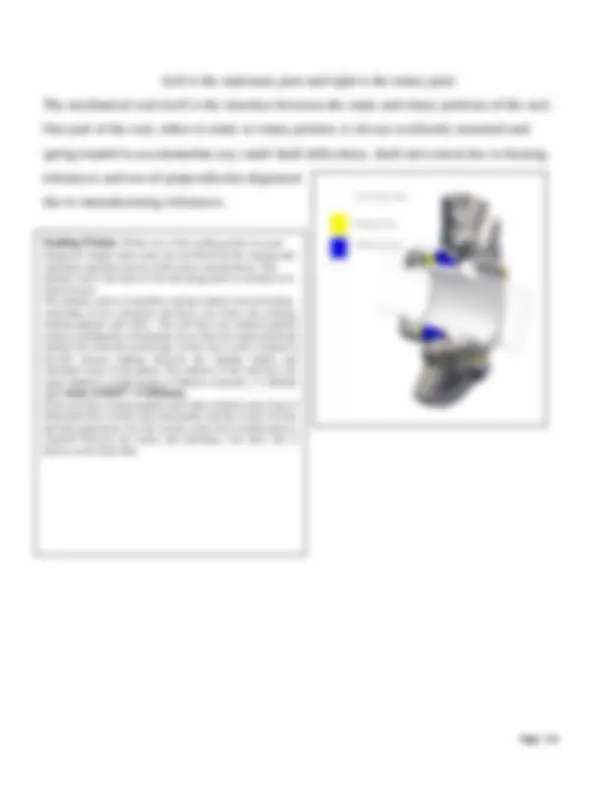
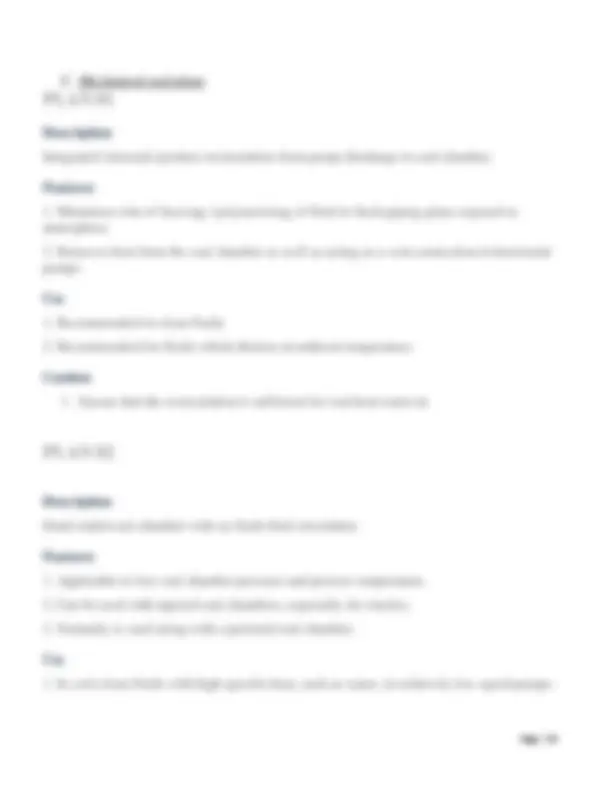
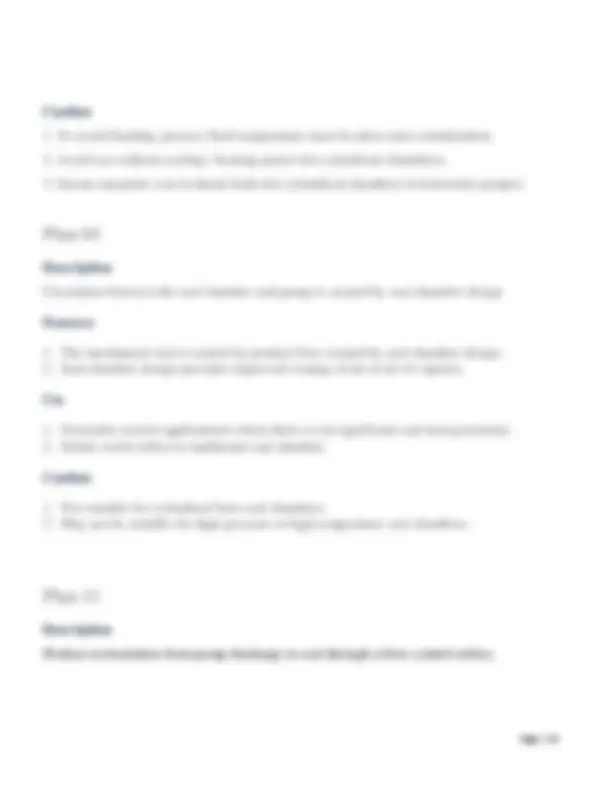
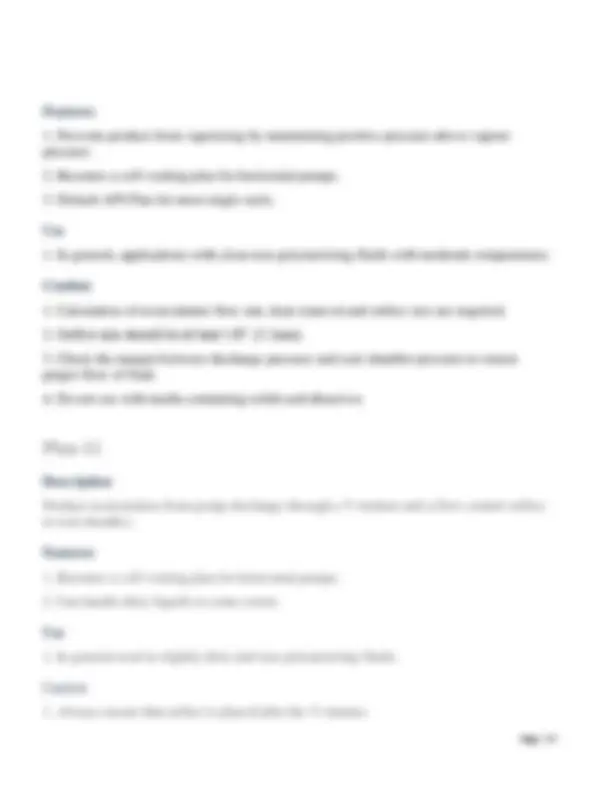
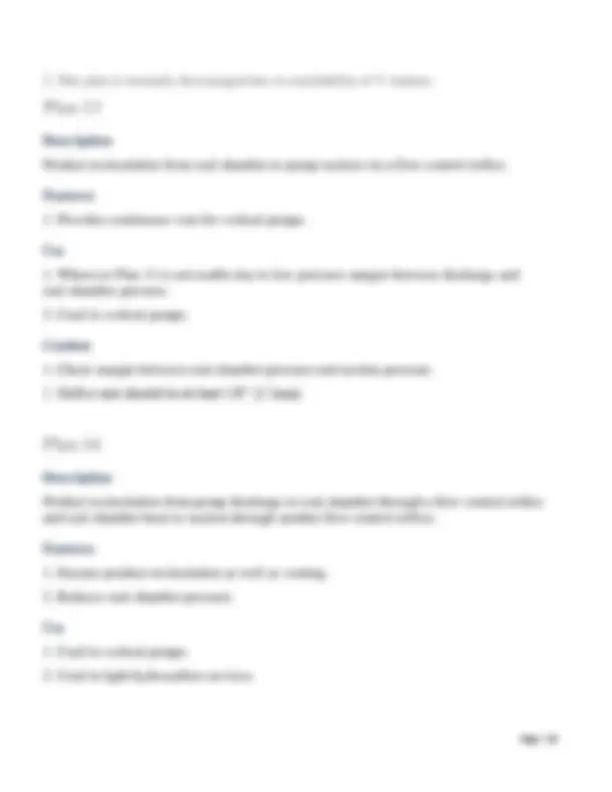
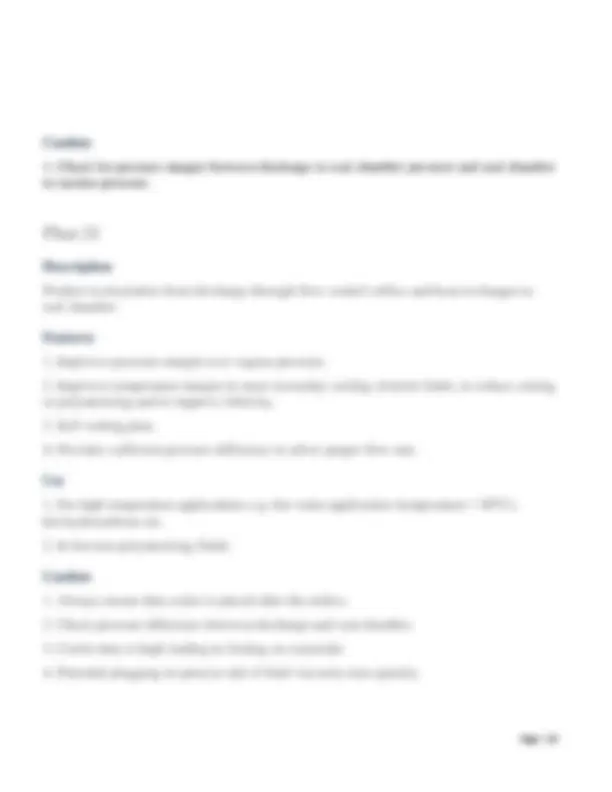
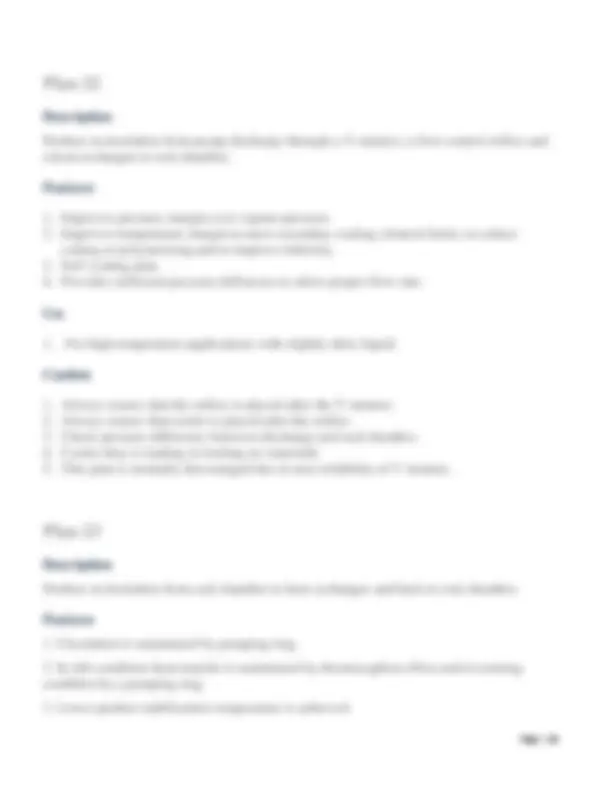
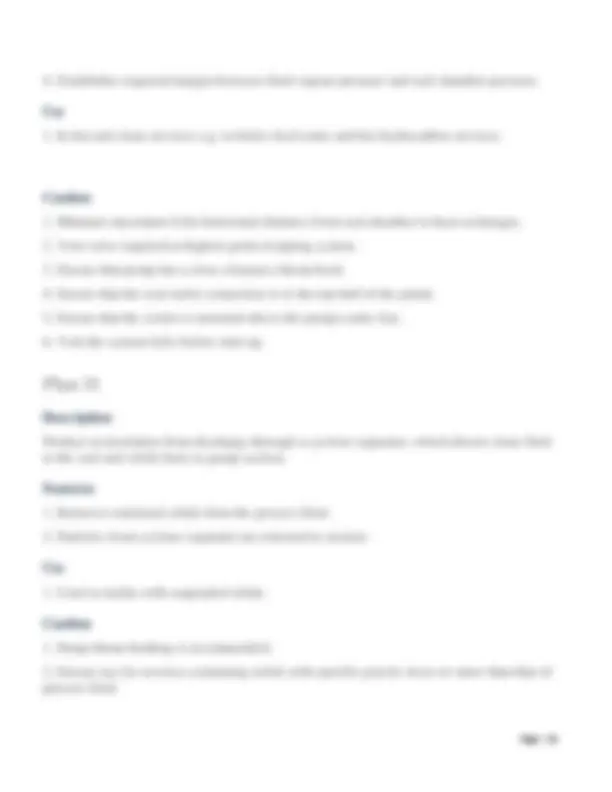
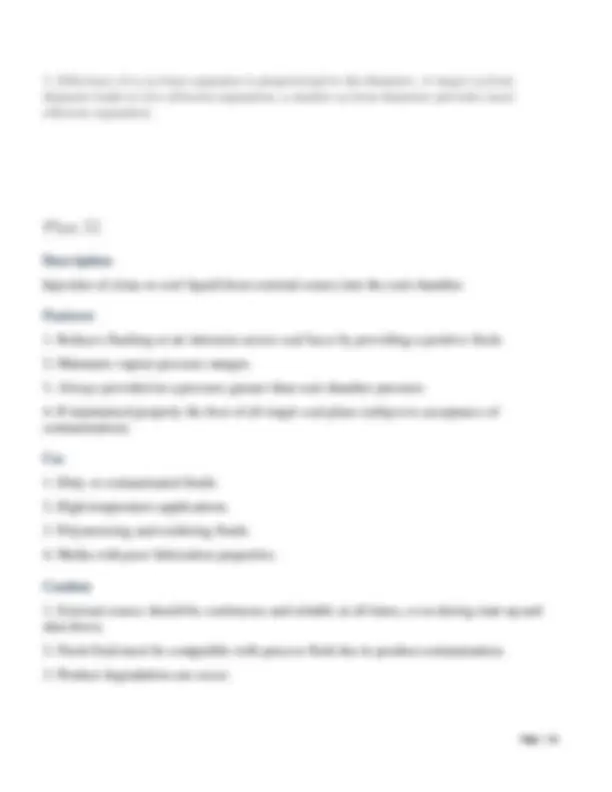
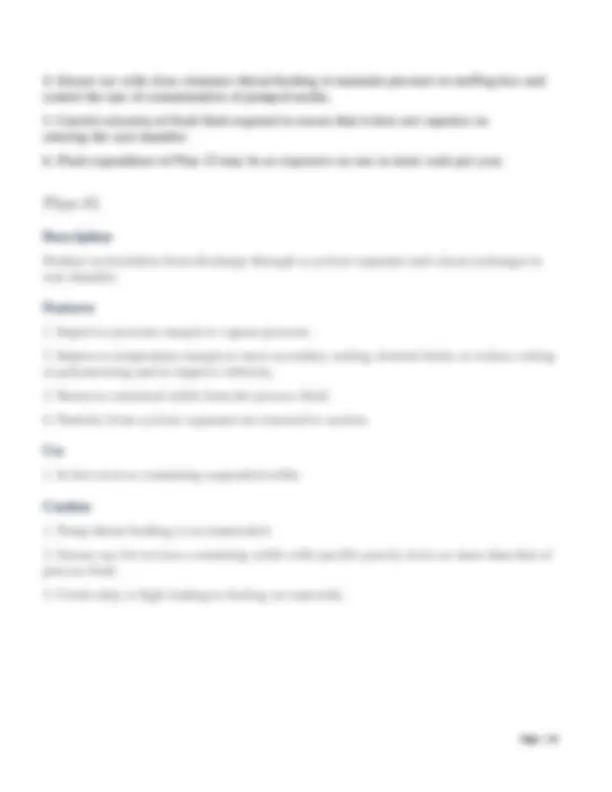
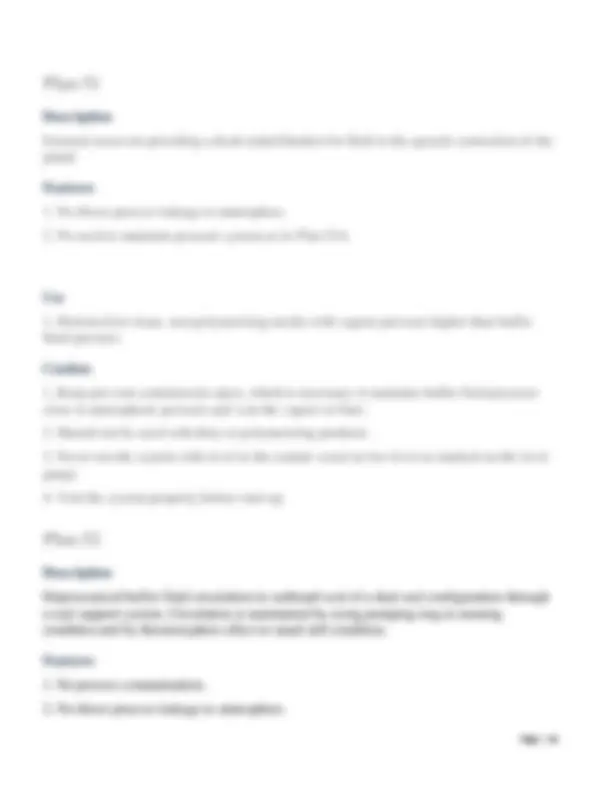
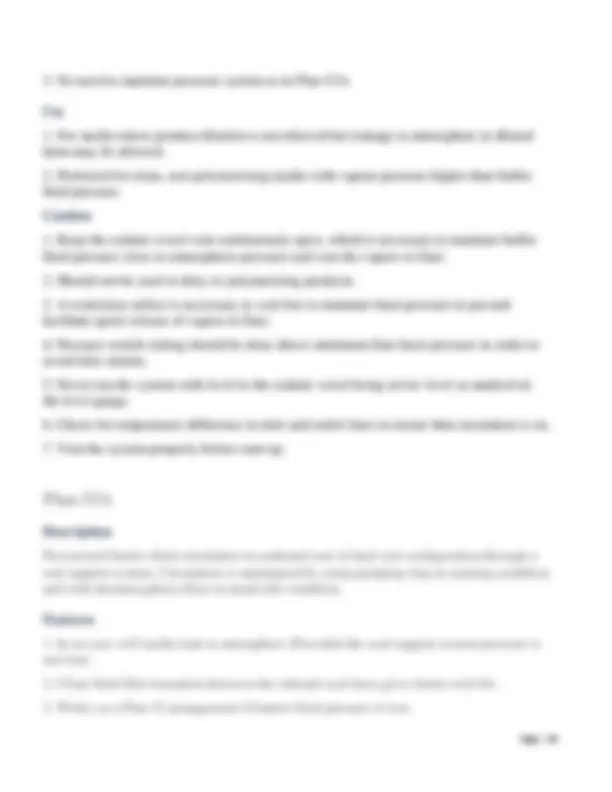
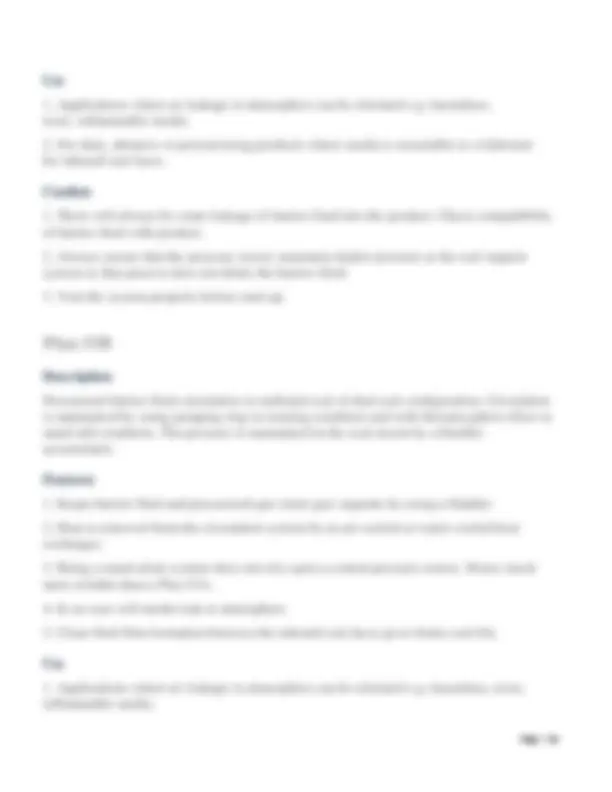
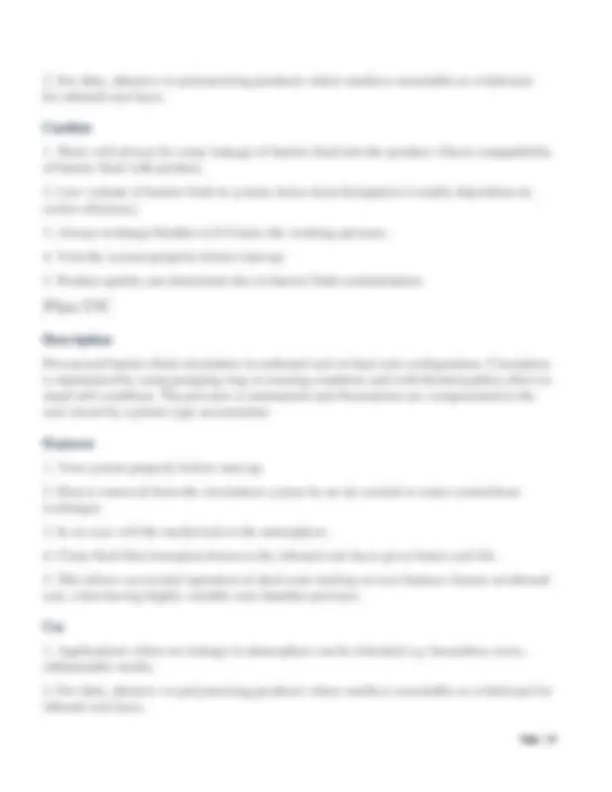
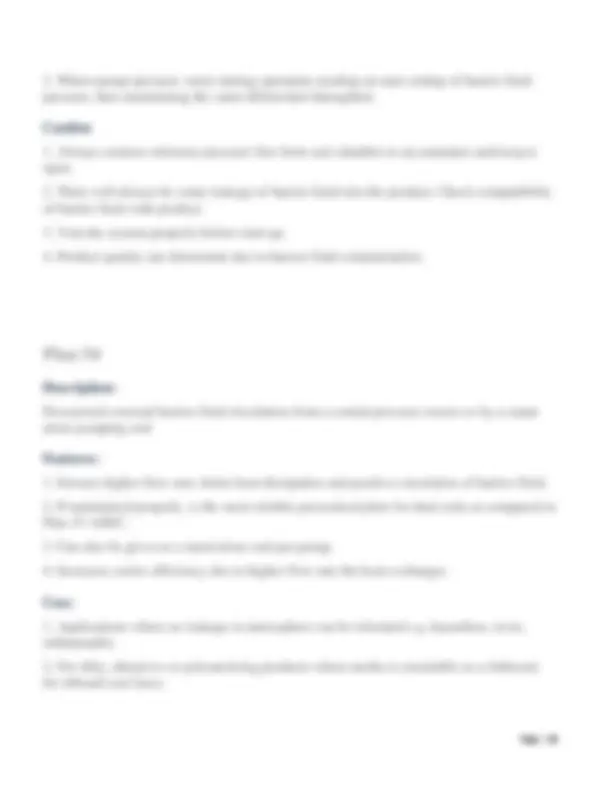
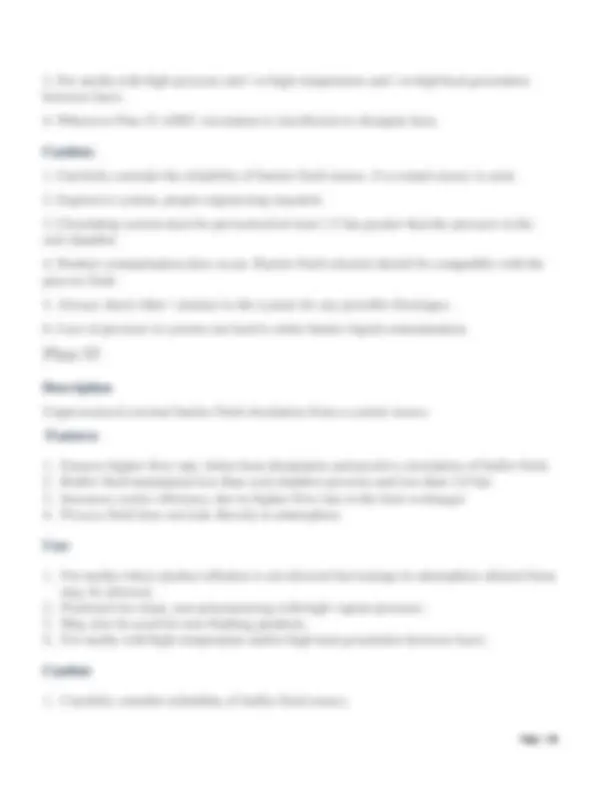
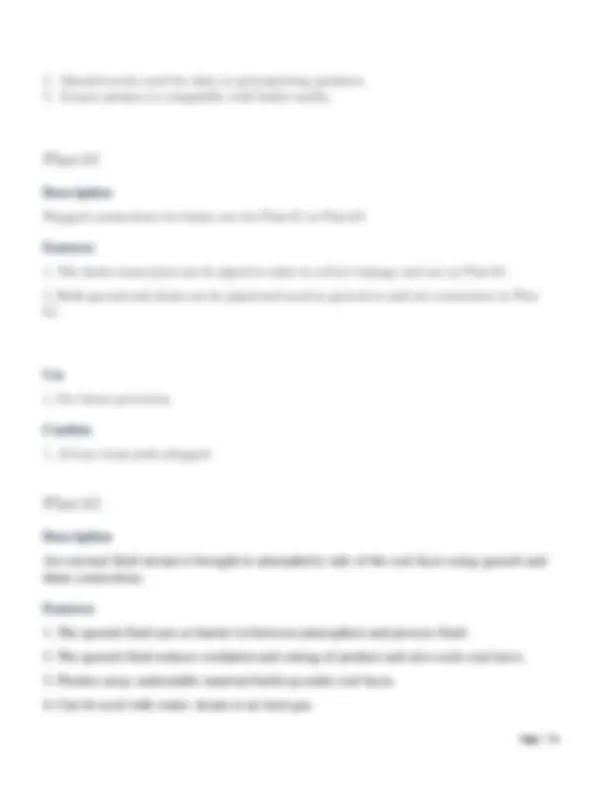
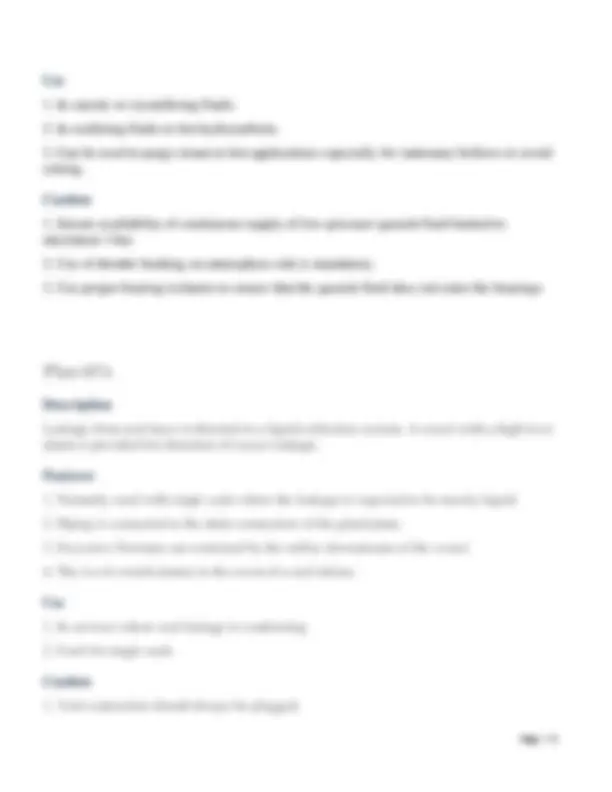
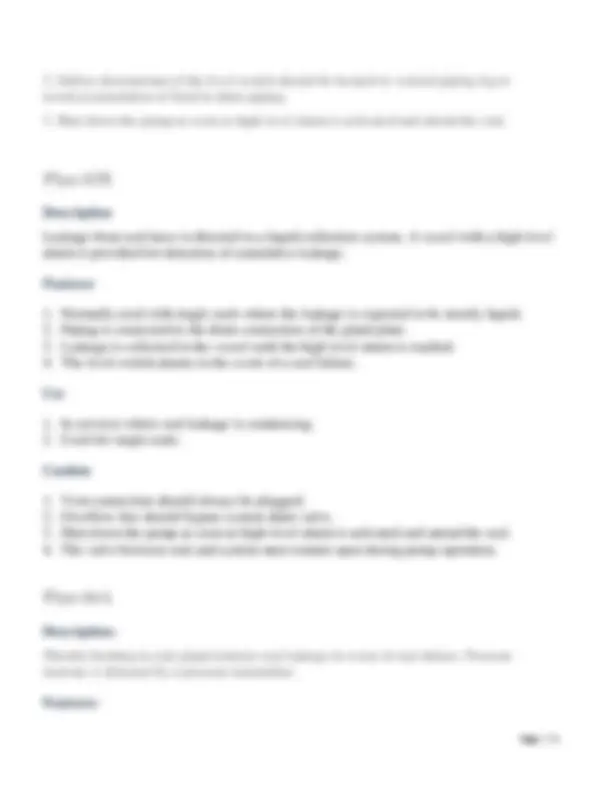
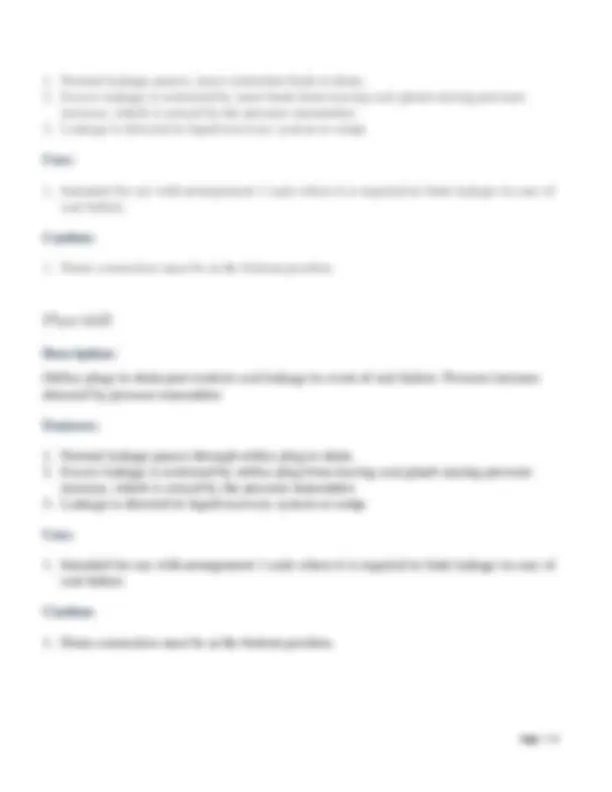
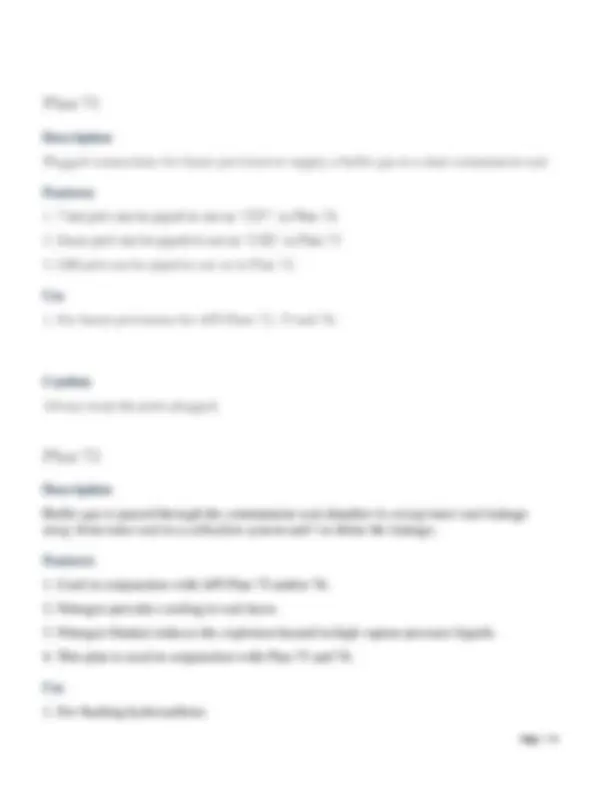
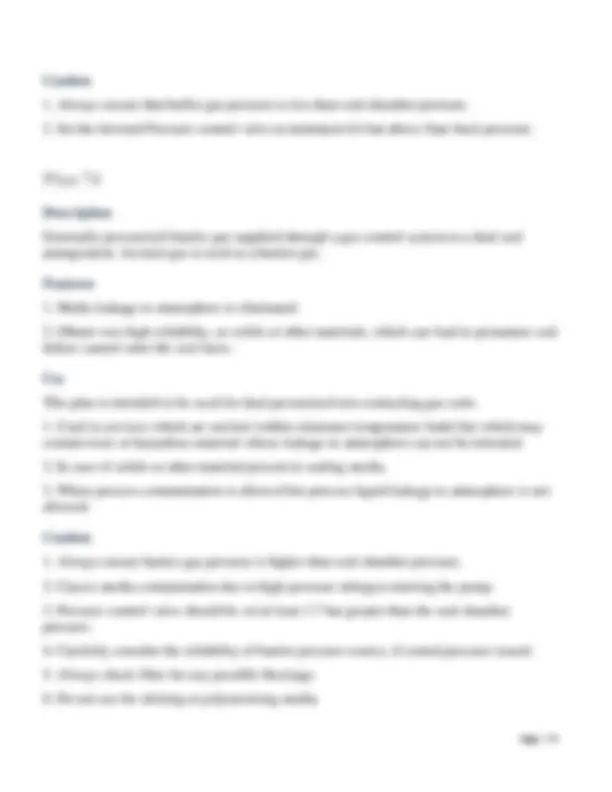
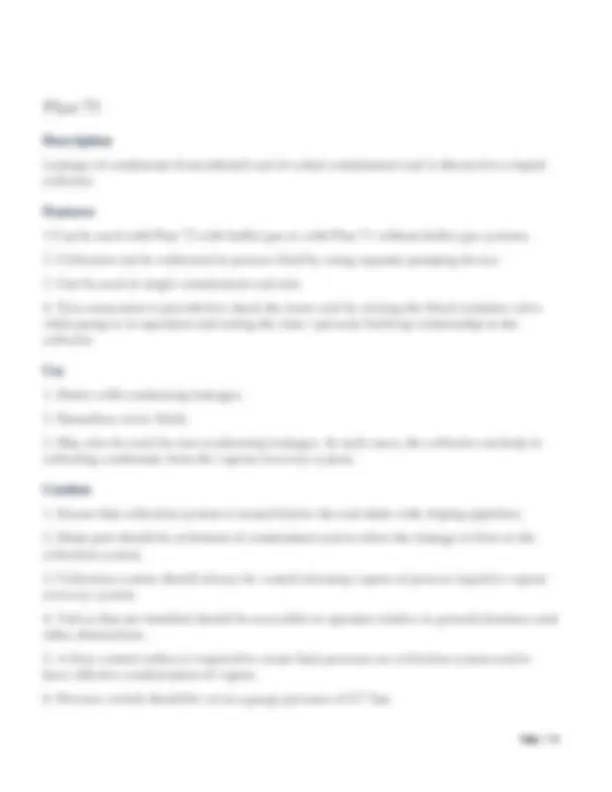
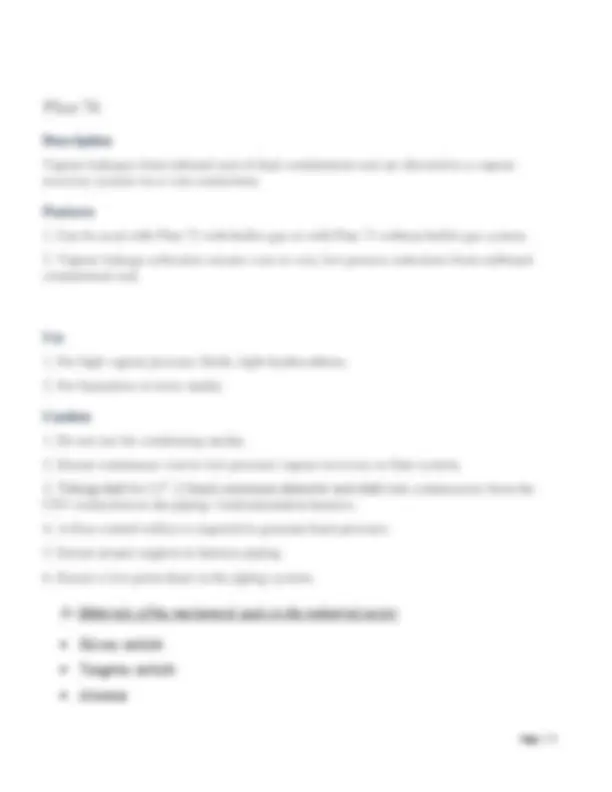
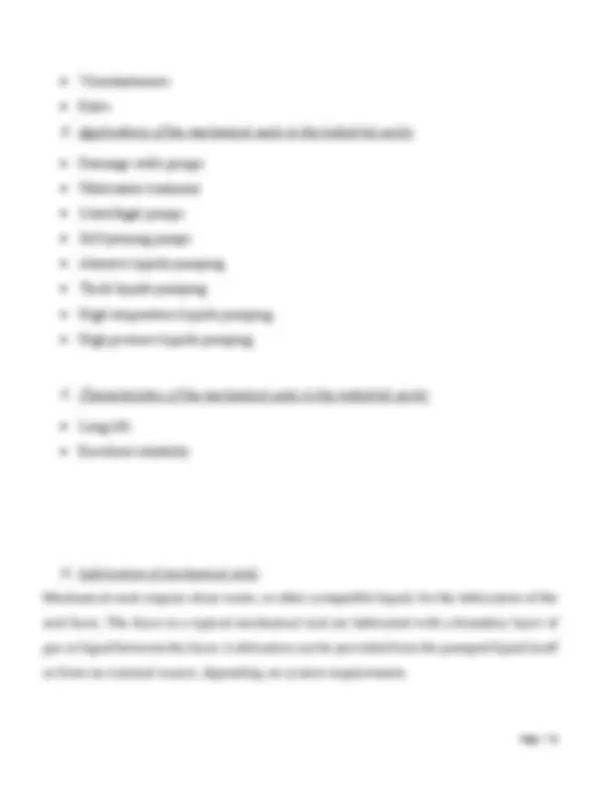
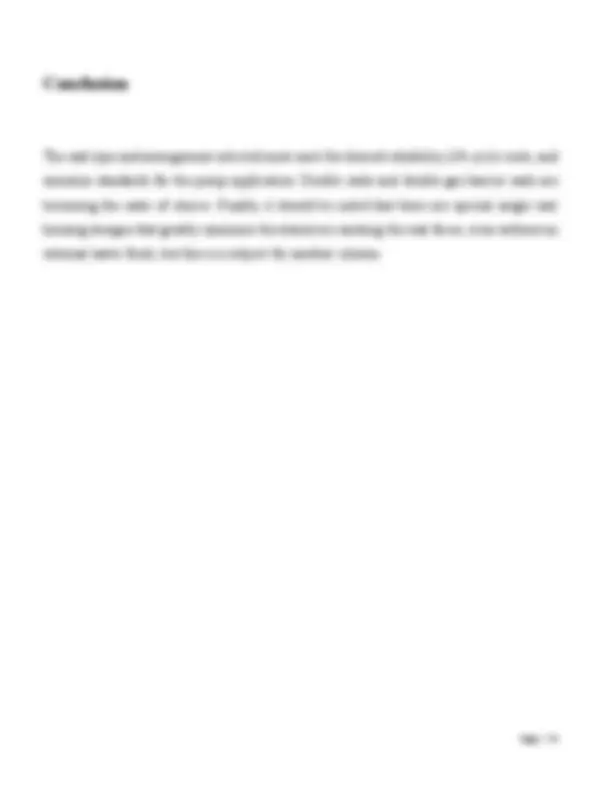
Study with the several resources on Docsity
Earn points by helping other students or get them with a premium plan
Prepare for your exams
Study with the several resources on Docsity
Earn points to download
Earn points by helping other students or get them with a premium plan
Community
Ask the community for help and clear up your study doubts
Discover the best universities in your country according to Docsity users
Free resources
Download our free guides on studying techniques, anxiety management strategies, and thesis advice from Docsity tutors
Mechanical seals, their role in industrial applications such as pumps and compressors, and various sealing solutions for overpressure events. Topics include different types of mechanical seals, their functions, and sealing plans for handling different types of fluids and pressures. The document also touches upon materials used in mechanical seals and their applications.
Typology: Lab Reports
1 / 79
This page cannot be seen from the preview
Don't miss anything!
This Public Enterprise Represents India's Energy Security Through its Pioneering Efforts. Maharatna ONGC is the largest crude oil and natural gas Company in India, contributing around 70 per cent to Indian domestic production. Crude oil is the raw material used by downstream companies like IOC, BPCL, and HPCL to produce petroleum products like Petrol, Diesel, Kerosene, Naphtha, and Cooking Gas-LPG. This largest natural gas company ranks 11th among global energy majors (Platts). It is the only public sector Indian company to feature in Fortune’s ‘Most Admired Energy Companies’ list. ONGC ranks 18th in ‘Oil and Gas operations’ and 183rd overall in Forbes Global 2000. Acclaimed for its Corporate Governance practices, Transparency International has ranked ONGC 26th among the biggest publicly traded global giants. It is most valued and largest E&P Company in the world, and one of the highest profitmaking and dividend-paying enterprise. ONGC has a unique distinction of being a company with in-house service capabilities in all areas of Exploration and Production of oil & gas and related oil-field services. Winner of the Best Employer award, this public sector enterprise has a dedicated team of over 33,500 professionals who toil round the clock in challenging locations.
ONGC is the only fully–integrated oil and gas company in India, operating along the entire hydrocarbon value chain. It has single-handedly scripted India's hydrocarbon saga. Some key pointers:
Any process industry can be solely divided into 4 parts:
The Hazira Gas Processing Complex or HGPC, Surat is first of its kind in India and Asia’s largest gas processing facility. It is situated near Bhatpore Village, on Surat Dumas Road, 18 Km to the western side from Surat Railway Station. The Plant covers an area of 705 Hectares of land; it is situated at the bank of Tapti River connecting Kachchh track pipeline originating from the south Basin in the off shore Vasai gas field of ONGC Mumbai and Panna, Mukta & Tapti fields operating under joint venture. About 776 ONGC Employees and Officers and 1422 contract workers are working inside the Plant. The Plant was set up in September, 1985. The total facilities which have been installed are Gas Terminal, Condensate, and Fractionation Units. Liquefied Petroleum Gas Plant, Gas Sweetening Unit, Unit for Gas Dehydration, Dew Point Depression. Sulphur Recovery Unit, Kerosene recovery unit and Co-Generation Unit. The Project is set up at a capital investment of Rs. 1337 Crores approx. including Phase-III (A). In view of ageing of Phase-I & Phase-II facilities (commissioned in 1988 & 1990 respectively) and likely increase of gas production from ONGC’s Western Offshore fields, as part of Phase-IV of expansion of Hazira Complex, ONGC has installed Additional Gas Processing Facilities (AGPF Project).
The ONGC Gas processing unit is located at Hazira on the suburbs of Surat city in Gujarat. HGPC plant was specifically laid for processing Natural gas, which is found at Bombay High. This plant comes under the Mumbai Region Business Centre (MRBC). Hazira Gas Processing Complex was set up in September 1985 to receive gas from Mumbai High initially and subsequently to process sour Natural Gas from Basin and other offshore fields. Sour gas along with associate condensate is transported through two sub-sea pipelines: one 36” diameter (231 kms) and the other 42” diameter (244 kms) from basin offshore process platform to Hazira plant. From here the natural gas production is carried out which on earlier stage is supplied to GAIL and HBJ (Hazira Bijapur Jagdishpur) pipeline. With the discovery of Bombay High begun the growth of Mumbai region. From a small beginning Exploratory Bombay High with India’s first offshore Sagar-Samrat. ONGC has come a long way. After its success in Bombay High ONGC discovered various other fields in western offshore. Among the various discoveries in western offshore, South Basin proved to be one of the biggest gas fields in Asia. Total recoverable reserves are estimated to be of order of 200 billion cubic meters which is phenomenal when compared to such fields in the world. The exploration of basin Field paved way for development of units’ plants built with state of the art technology at a cost of Rs. 1300 crores and process of growth is continued. It has gas processing capacity of 41MMSCMD (Million Metric Standard Cubic Meter per Day). The whole Plant is completely automated where no one can find a single person working in the field area. This fully automated plant is maintained and inspected regularly with the responsible group of people. Number of gas based industries in Gujarat and Northern India, covering Delhi to bring gas to shore and the process before it is distributed to consumers, ONGC had chosen a 625 hectares of land in Hazira plant about 20 km away from surat town which has now grown to gigantic complex sprawling in 705 hectares.
The plant receives gas in 36” and 42” pipelines through 217 km long submarine pipes from South Basin to Umbhrat and then 14 km long lines from Umbhrat to the Gas Terminal. Here gas and any condensates formed are separated. The gas goes to Gas Sweetening Unit or GSU and the condensate is sent to Condensate Fractionation Unit or CFU. In GSU the feed gas is freed of hydrogen sulphide and is hence “sweetened”. The hydrogen sulphide recovered is sent to Sulphur Recovery Unit or SRU, where it is converted into elemental sulphur and dried into bricks. Commercial production of the same is not done. Sweet gas is sent to Gas Dehydration Unit or GDU for removal of any moisture. Product of GDU is sent to the Dew Point Depression or DPD Unit, where the sweet and dry fuel gas is freed from any condensates, and then is sent for packaging and dispatch. A part of sweet gas from GSU is taken within the plant and sent to the LPG recovery unit to obtain LPG and Propane, latter being required for refrigeration within the plant. The condensate sent to the CFU is separated into Naphtha and Natural Gasoline Liquid or NGL. The former is packed and dispatched. The latter is sent to Kerosene Recovery Unit or KRU where value added products like Superior Kerosene Oil (SKO), Aviation Turbine Fuel (ATF), and High Speed Diesel (HSD) are formed. The LPG, SKO, and ATF from CFU and KRU are
a) KRIBHCO b) ESSAR c) GAIL d) IOCL e) HPCL f) BPCL
a. Rail b. Road c. Pipeline d. Ship
b. Naphtha – Ship, Pipeline, Rail c. SKO – Road, Pipeline d. Sulphur – Road
This unit removes water vapors from sweetened gas from GSU. The sweet gas enters inlet knock out drum of gas dehydration unit, where gas comes in contact with lean Tri-Ethylene Glycol solution in Absorption column. The dry gas liberated from top of Absorber forms feed for DPDU. The rich Tri-Ethylene Glycol coming out of bottom of Absorber passes through set of cartridge filter, charcoal filter and sent to Reboiler and Regenerated to remove absorbed moisture. The regenerated Tri-Ethylene Glycol is continuously recycled and reused in the system. I.Objective
II.Product Specification LPG: The plant is designed to extract LPG from the feed gas and condensate. Specifications of LPG will be 50:50 by wt. (approx.) of C3:C4 and will conform to IS-4576 for marketing system. Vapour pressure of LPG=16.87 Kg/cm2a (max) at 45 OC. The amount of H2S is maintained less than 4ppm. ARN: By product Aromatic Rich Naphtha is a mixture of pentane and heavier hydrocarbons as present in feed streams. Vapour pressure=0.9 Kg/cm2a (max) at 40 OC. Lean Gas: Composition of Lean Gas from LPG recovery facility will depend on the feed gas composition and is expected to vary with time. III.Process Description Feed gas from gas sweetening unit available at the LPG plant B/L at a pressure range of 75- 52 Kg/ cm2abs (around 60 Kg/ cm2abs presently) and a temperature of around 38 OC (32-34 OC presently) flows to a Knock Out Drum where any liquid present in the gas is knocked off. Bulk of the water is removed from the gas by cooling it up to 25 OC (presently 22-24 OC). After this, the gas flows through a molecular sieve dryer where the moisture is reduced to up to 1 ppm level.
This dried gas is cooled to - 30 OC in a Cold Box and the condensed liquid is separated out in Separator-I. Vapours from separator are expanded almost isentropically in result of which the temperature further falls down to - 54 OC (presently around - 53.6 OC). Liquid condensed on cooling is separated out in Separator-II. The refrigeration of the vapour stream from Separator-II is recovered to cool down the feed gas stream. Further, this lean gas is compressed by expander compressor to about 37 Kg/ cm2abs (from 30 kg/cm2) and finally to 48.5 Kg/ cm2abs (presently 46.5 Kg/ cm2abs) by the lean gas compressor and supplied to consumers as high-pressure lean gas. Condensate from Dew Point Depression unit available at plant B/L at 73-50 Kg/cm2abs ( Kg/ cm2abs at present) pressure is flashed into surge drum after heating to 25 OC (28- 30 OC presently) to avoid hydrate formation. Condensate is passed through a Coalescer where most of the free water present in the condensate is separated out. Hydrocarbon liquid from Coalescer flows to liquid dryers where the moisture content is brought down to 5 ppm.
Purpose of NFU: Purpose of this plant is to produce kerosene, naptha, ATF, HSD etc., products from the condensate coming from CFU plant.
The purpose is to remove hydrocarbon condensate from the sweetened and dehydrated gas by chilling to avoid hydrate formation in long distance HBJ pipeline. The feed gas from GDU train is chilled to about - 5 °C in a chilled with the help of propane refrigerant in close circulation cycle. The cooled gas condensate is pumped to LPG plant for distillation. This treated gas is then sent to GAIL for onward transmission to HBJ pipeline and partly to local consumers. The DPD unit Phase- I consists of two (2) identical trains no. 51 & 52, Phase-II consists of two (2) identical train no. 53 & 54 and Phase-III consists of four (4) identical train no. 55, 56, 57 & 58 and Phase-IV Consist of One Identical Train no. 59. The unit is designed to process 5.4 MMNM3 / day of sweetened and dehydrated gas The dew point depression unit is designed, as the name suggests lowering or depressing the dew point of the gas. This objective is achieved by lowering the gas temperature well below the minimum temperature which the gas may attain in the HVJ pipeline. I. Process description: Sweet and dehydrated gas is treated in this DPD unit to lower hydrocarbon dew point of gas well below the minimum temperature which the gas may attain in the HVJ pipeline. Expected minimum temperature that the gas may attain in HVJ pipeline is 11°C. Dew point depression unit is designed to chill the gas up to 5°C and recover condensate formed due to gas chilling. The process description for dew point depression unit is described in two sections: