
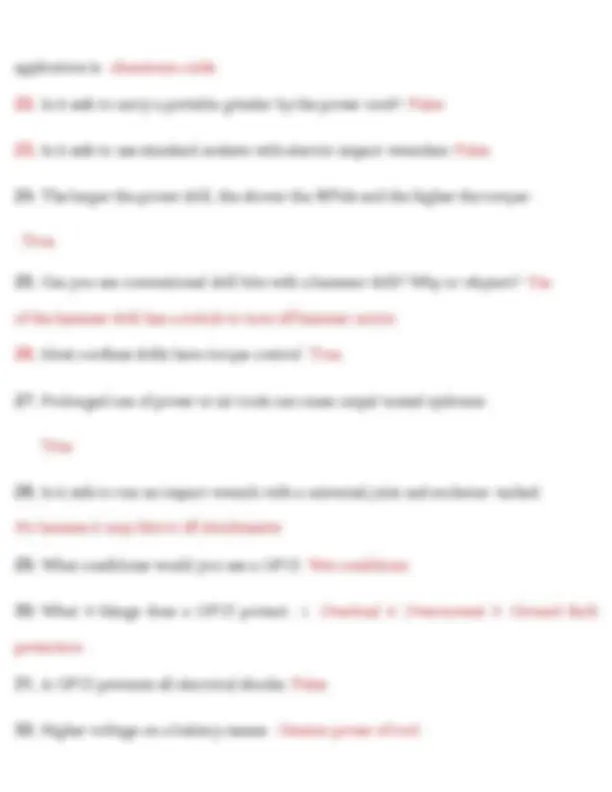
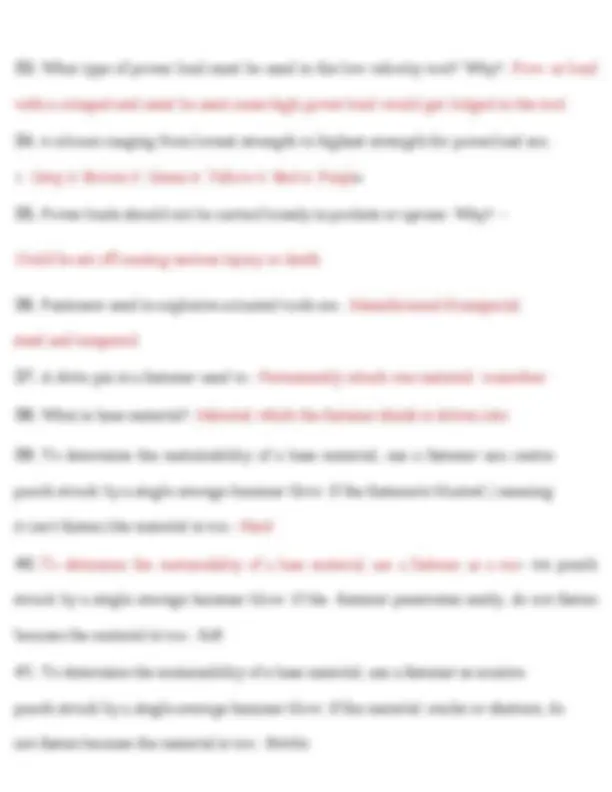
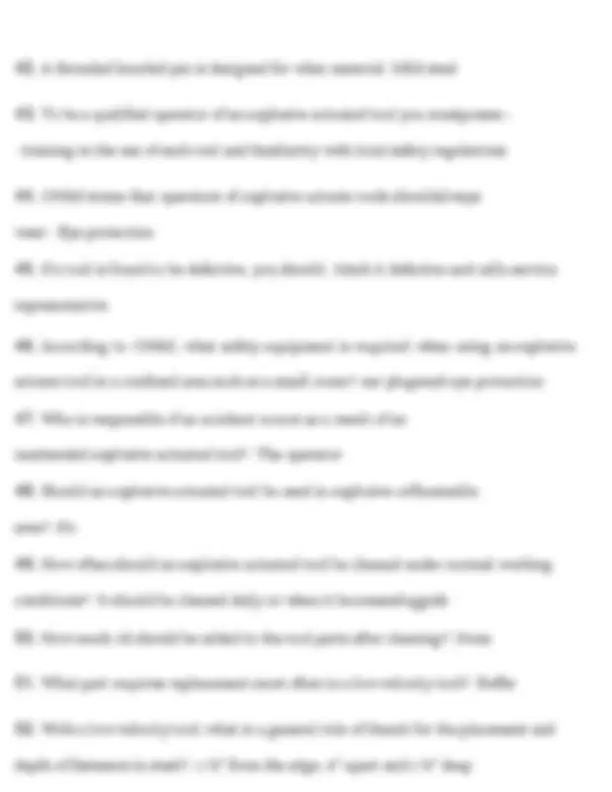
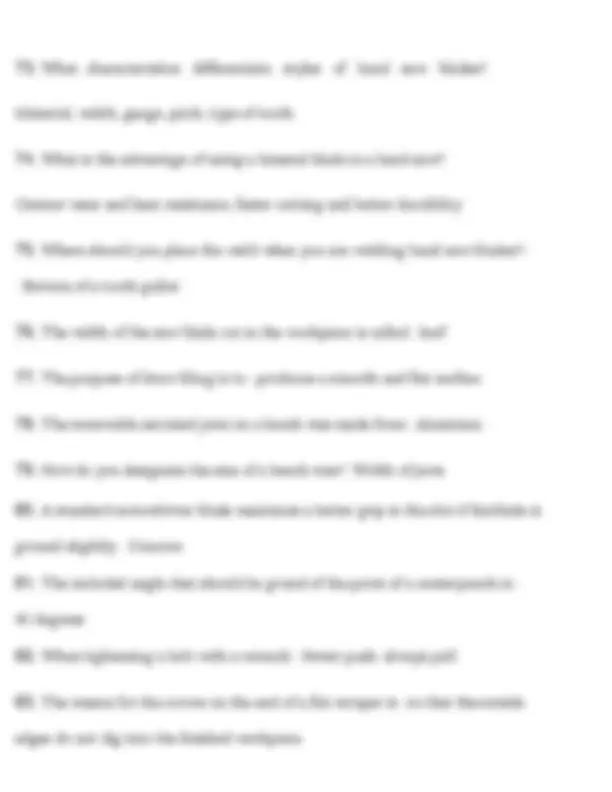
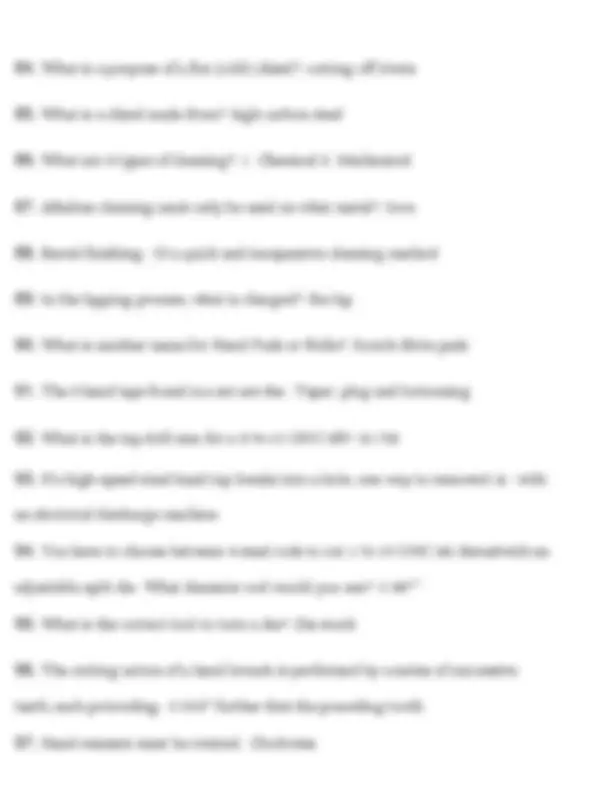
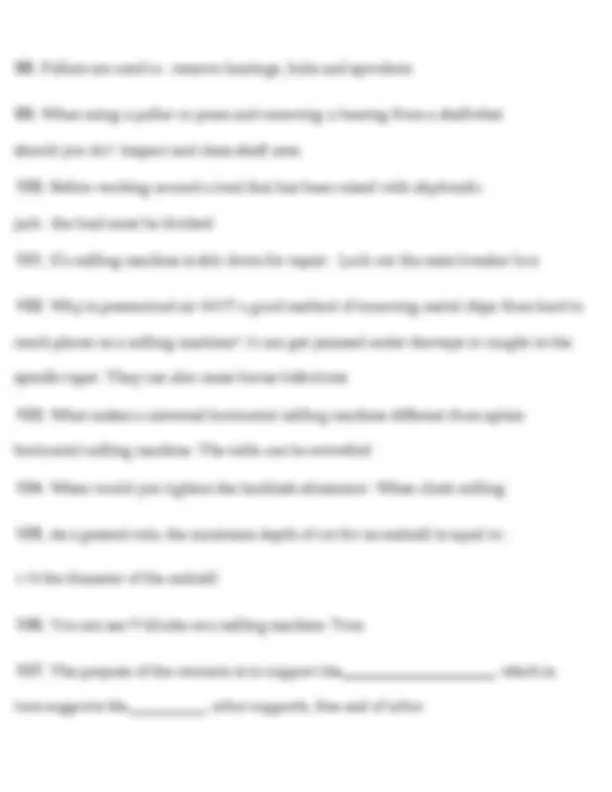
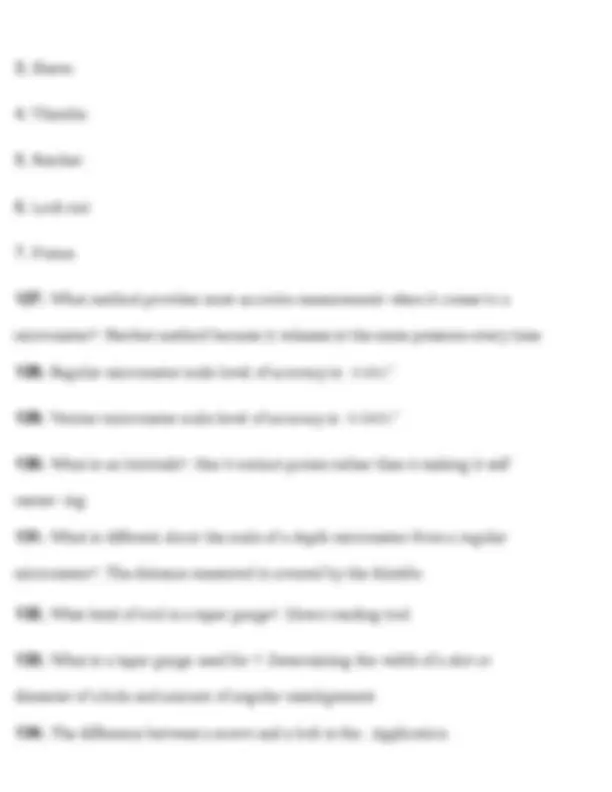
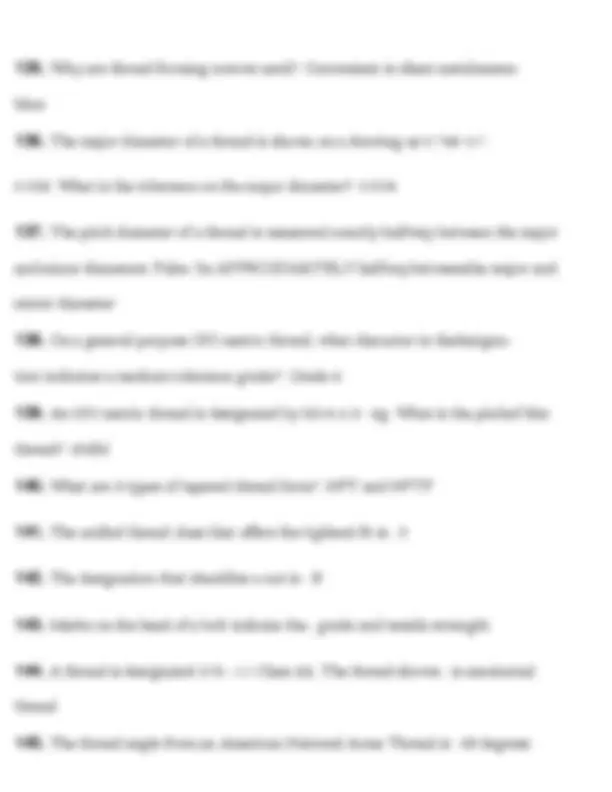
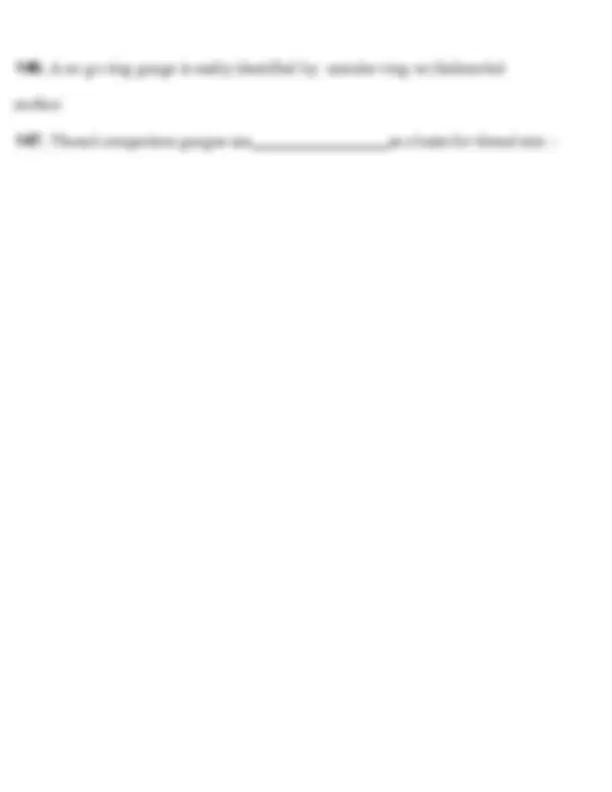
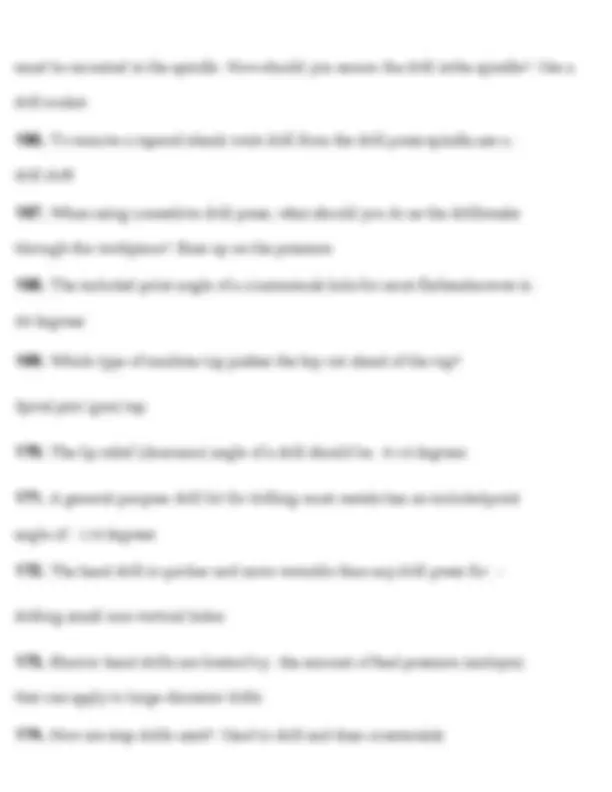
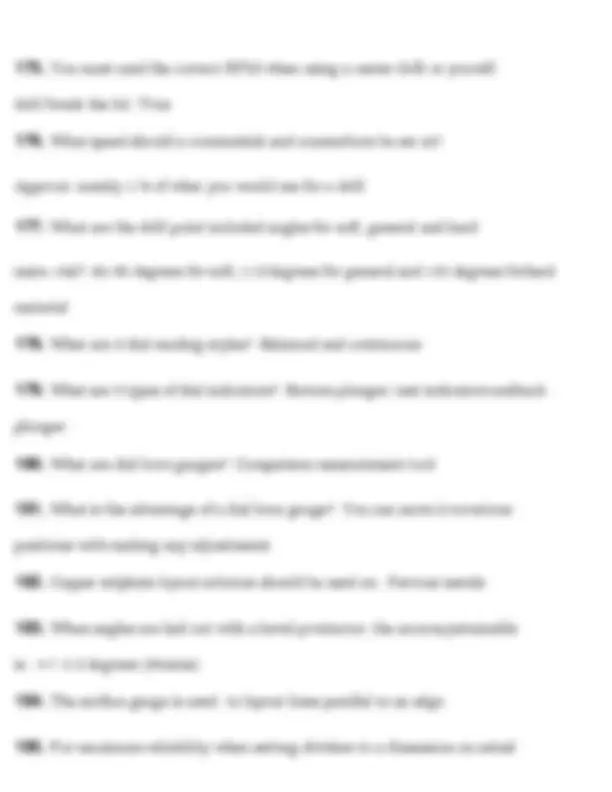
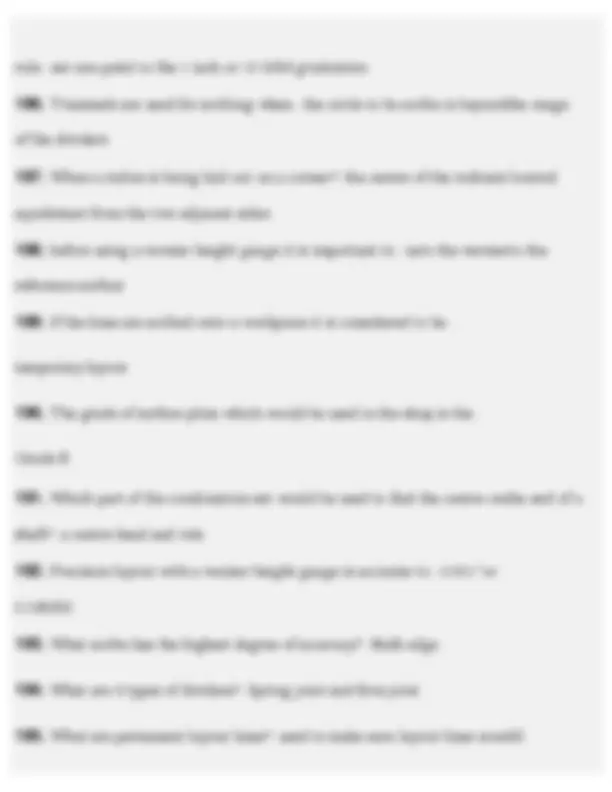
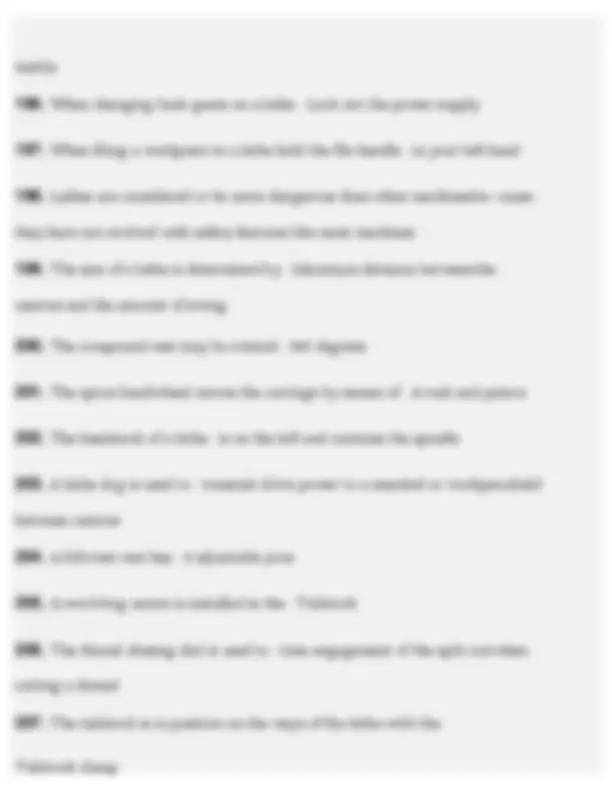
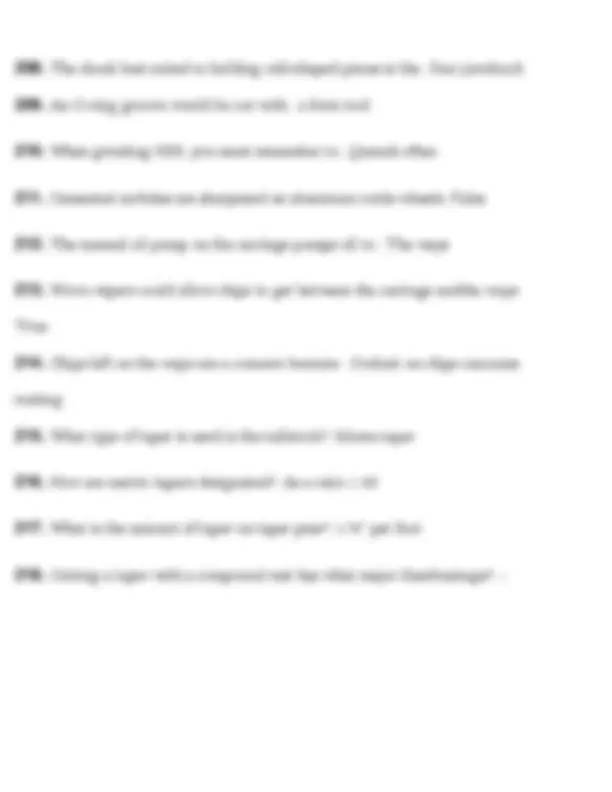
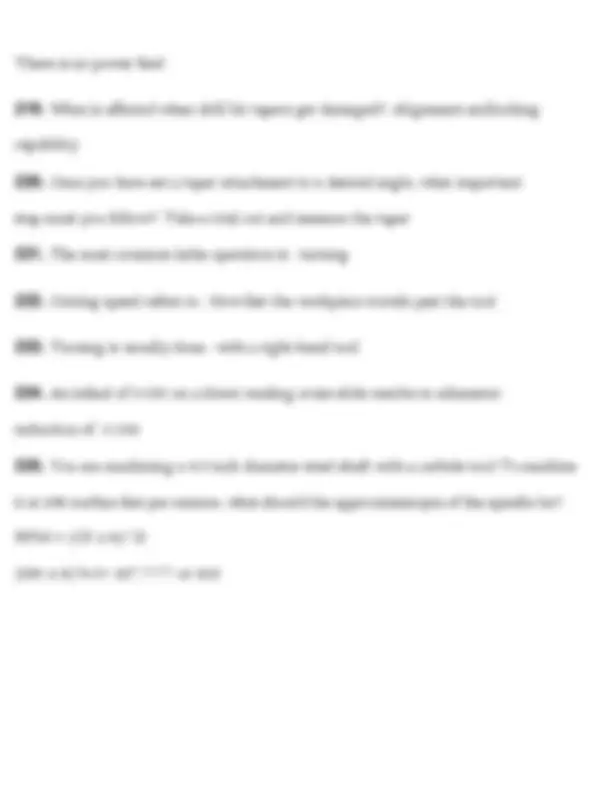
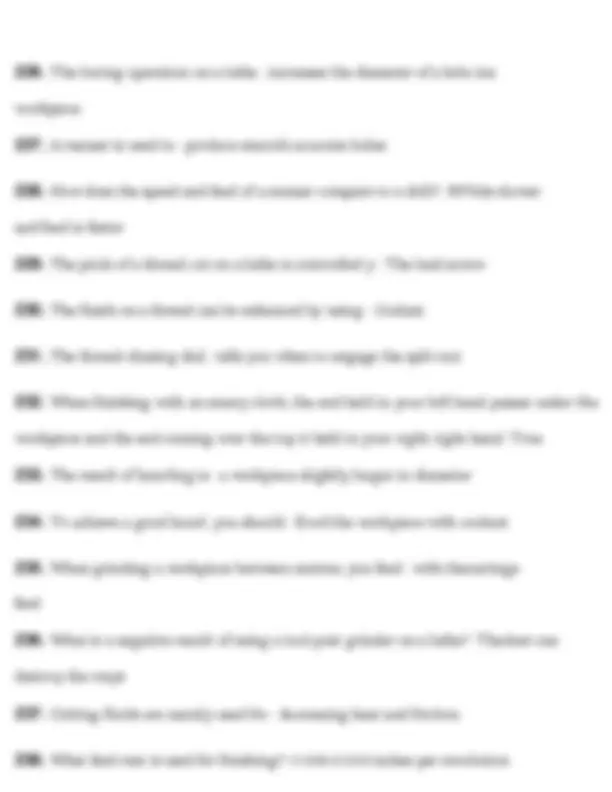
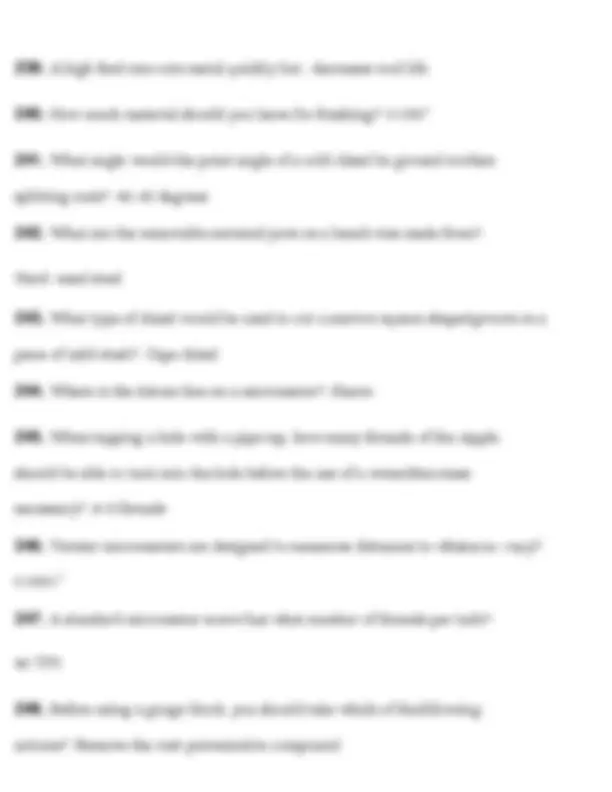
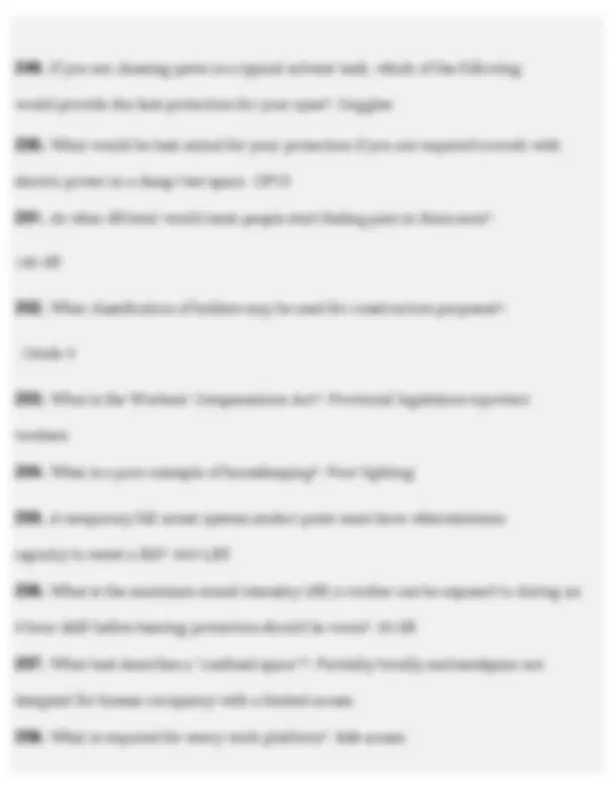
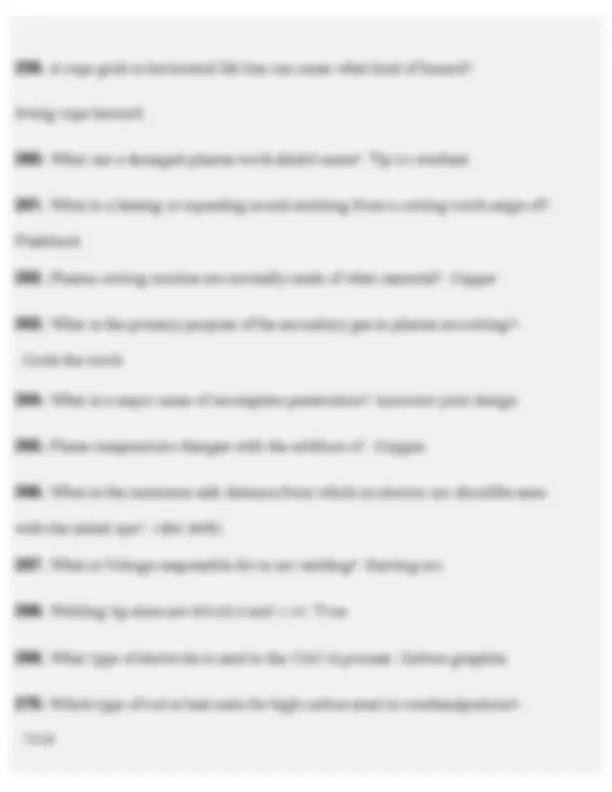
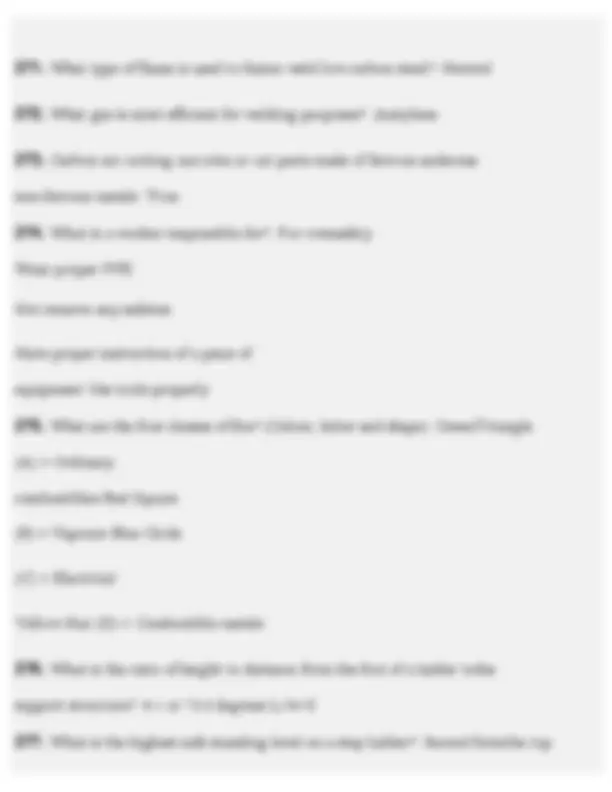
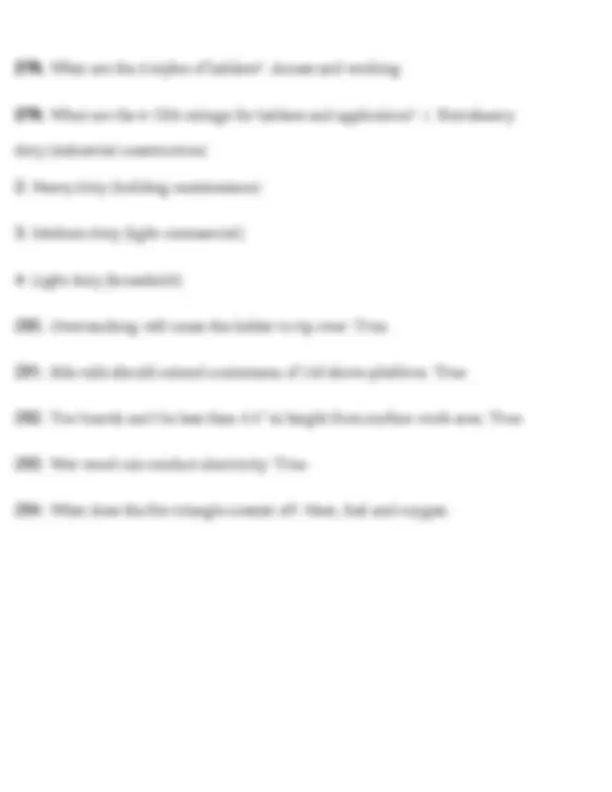
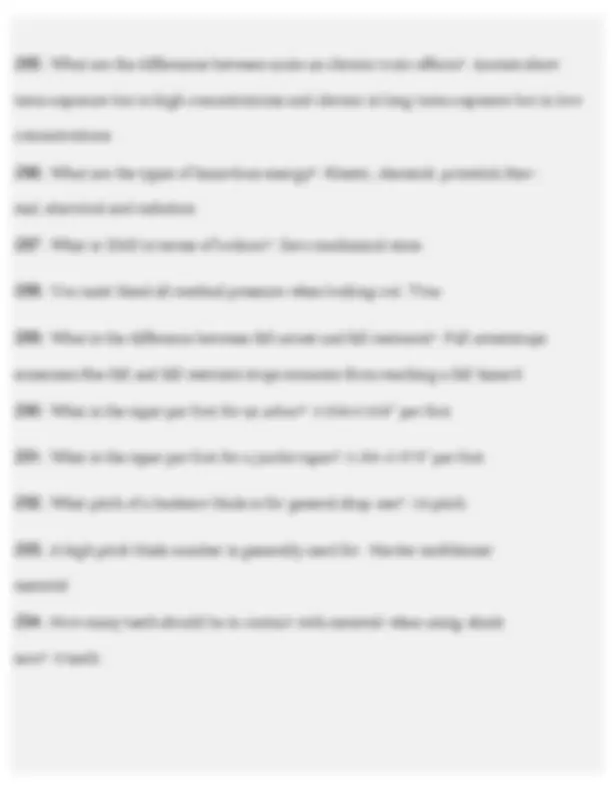
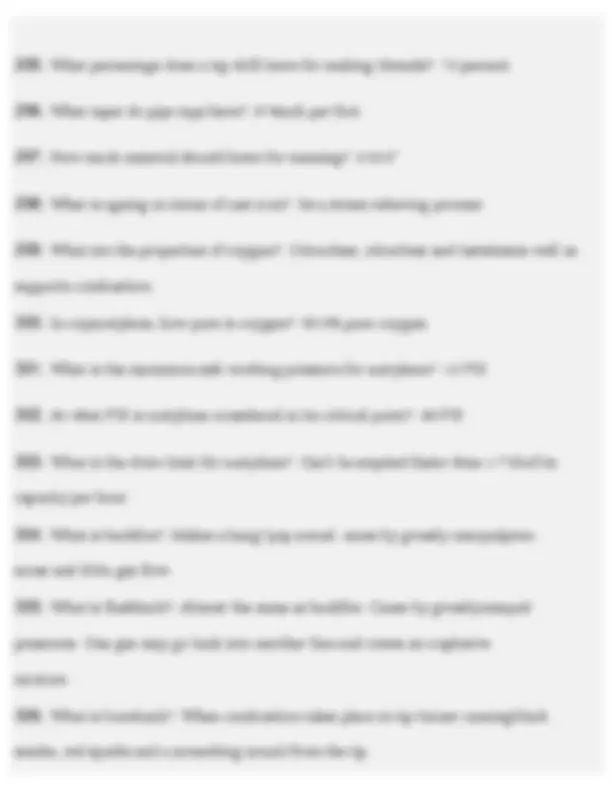
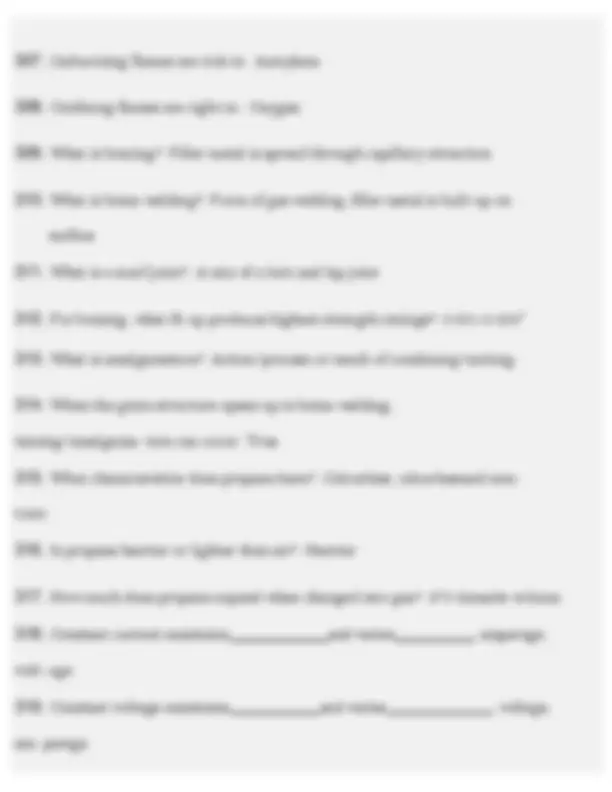
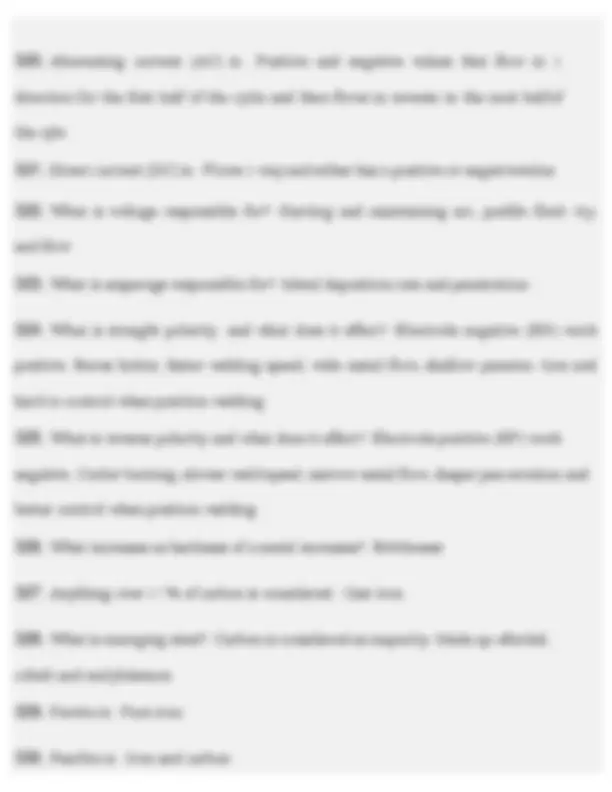
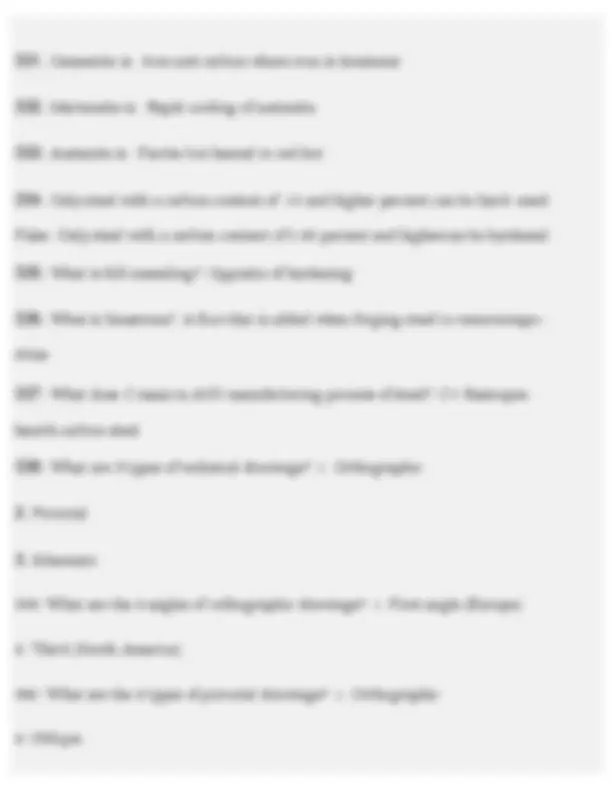
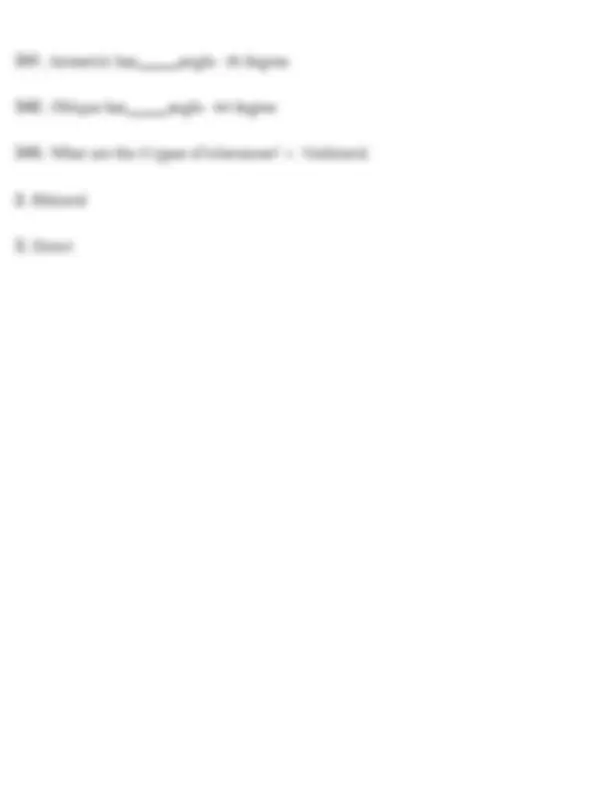
Study with the several resources on Docsity
Earn points by helping other students or get them with a premium plan
Prepare for your exams
Study with the several resources on Docsity
Earn points to download
Earn points by helping other students or get them with a premium plan
Community
Ask the community for help and clear up your study doubts
Discover the best universities in your country according to Docsity users
Free resources
Download our free guides on studying techniques, anxiety management strategies, and thesis advice from Docsity tutors
This comprehensive document provides a thorough review of millwrighting principles and practices, covering topics such as grinding wheels, power tools, explosive actuated tools, and hand tools. it includes over 340 questions and answers, ideal for students preparing for a level 1 millwright final exam. The questions test knowledge of safety procedures, tool operation, and material properties, ensuring a well-rounded understanding of the subject matter.
Typology: Exams
1 / 35
This page cannot be seen from the preview
Don't miss anything!
2 / 15 Blotter
135. Why are thread forming screws used?: Convenient in sheet metal assem- blies 136. The major diameter of a thread is shown on a drawing as 0.748 +/- 0.002. What is the tolerance on the major diameter?: 0. 137. The pitch diameter of a thread is measured exactly halfway between the major and minor diameters: False. Its APPROXIMATELY halfway betweenthe major and minor diameter 138. On a general purpose ISO metric thread, what character in thedesigna- tion indicates a medium tolerance grade?: Grade 6 139. An ISO metric thread is designated by M14 x 2 - 6g. What is the pitchof this thread?: 2MM 140. What are 2 types of tapered thread form?: NPT and NPTF 141. The unified thread class that offers the tightest fit is:: 3 142. The designation that identifies a nut is:: B 143. Marks on the head of a bolt indicate the:: grade and tensile strength 144. A thread is designated 5/8 - 11 Class 2A. The thread shown:: is anexternal thread 145. The thread angle from an American National Acme Thread is:: 29 degress
Pitch diameter
148. Rolled threads are advantageous over machined threads because:: They have increased tensile strength They produce a burnished thread finish They have better wear resistance which reduces fatigue and shear problems 149. What does API stand for: American Petroleum Institue 150. What kind of threads do Acme threads have?: 29 degree angle and the root and crests are flat 151. Hex set screws may sometimes be doubled up: True 152. What are cap screws made of?: High tensile steel 153. How is a Woodruff key sized?: First 2 numbers are multiplied by 1/32"and second set of numbers are multiplied by 1/8" 154. A rivet is:: a permanent fastener 155. What is the taper per foot of a tapered gib head key?: 1/8" per foot
156. What is the taper per foot of a tapered dowel pin?: 1/4" per foot 157. Cotter pins can be reused: False. Cotter pins are a one time use 158. Which variable is the most important when determining spindle speed?- : diameter of the drill 159. Any machined surfaces on a drill press that could rust must be:: Kept clean and oiled 160. When installing a taper shank drill into the spindle bore, you must takeseveral precautions. What are they and why?: Ensure taper and bore are clean, wipe with a rag without scraping/marking internal taper, any burrs are removed or it'll throw the bit off center 161. Cutting speed refers to:: Peripheral speed 162. How fast should a 1/2" drill turn when drilling mild steel if the cutting speed is 90 sfpm?: 720 RPM 163. Small drills require a higher feed per revolution than larger ones.: False 164. Which abbreviations is used to express the feed rate on a drill press?: IPR 165. A drill press has a #2 Morse taper. A twist drill with a #3 Morse taper shank
175. You must used the correct RPM when using a center drill or youwill dull/break the bit: True 176. What speed should a countersink and counterbore be set at?: Approxi- mately 1/4 of what you would use for a drill 177. What are the drill point included angles for soft, general and hard mate- rial?: 60 - 90 degrees for soft, 118 degrees for general and 150 degrees forhard material 178. What are 2 dial reading styles?: Balanced and continuous 179. What are 3 types of dial indicators?: Bottom plunger, test indicators andback plunger 180. What are dial bore gauges?: Comparison measurement tool 181. What is the advantage of a dial bore gauge?: You can move it tovarious positions with making any adjustments 182. Copper sulphate layout solution should be used on:: Ferrous metals 183. When angles are laid out with a bevel protractor, the accuracyattainable is:: +/- 0.5 degrees (30mins) 184. The surface gauge is used:: to layout lines parallel to an edge 185. For maximum reliability when setting dividers to a dimension on a steel
rule:: set one point to the 1 inch or 10 MM graduation
186. Trammels are used for scribing when:: the circle to be scribe is beyondthe range of the dividers 187. When a radius is being laid out on a corner?: the centre of the radius is located equidistant from the two adjacent sides 188. before using a vernier height gauge it is important to:: zero the vernierto the reference surface 189. If the lines are scribed onto a workpiece it is considered to be:: temporary layout 190. The grade of surface plate which would be used in the shop is the:: Grade B 191. Which part of the combination set would be used to find the centre on the end of a shaft?: a centre head and rule 192. Precision layout with a vernier height gauge is accurate to:: 0.001" or 0.02MM 193. What scribe has the highest degree of accuracy?: Knife edge 194. What are 2 types of dividers?: Spring joint and firm joint 195. What are permanent layout lines?: used to make sure layout lines are still